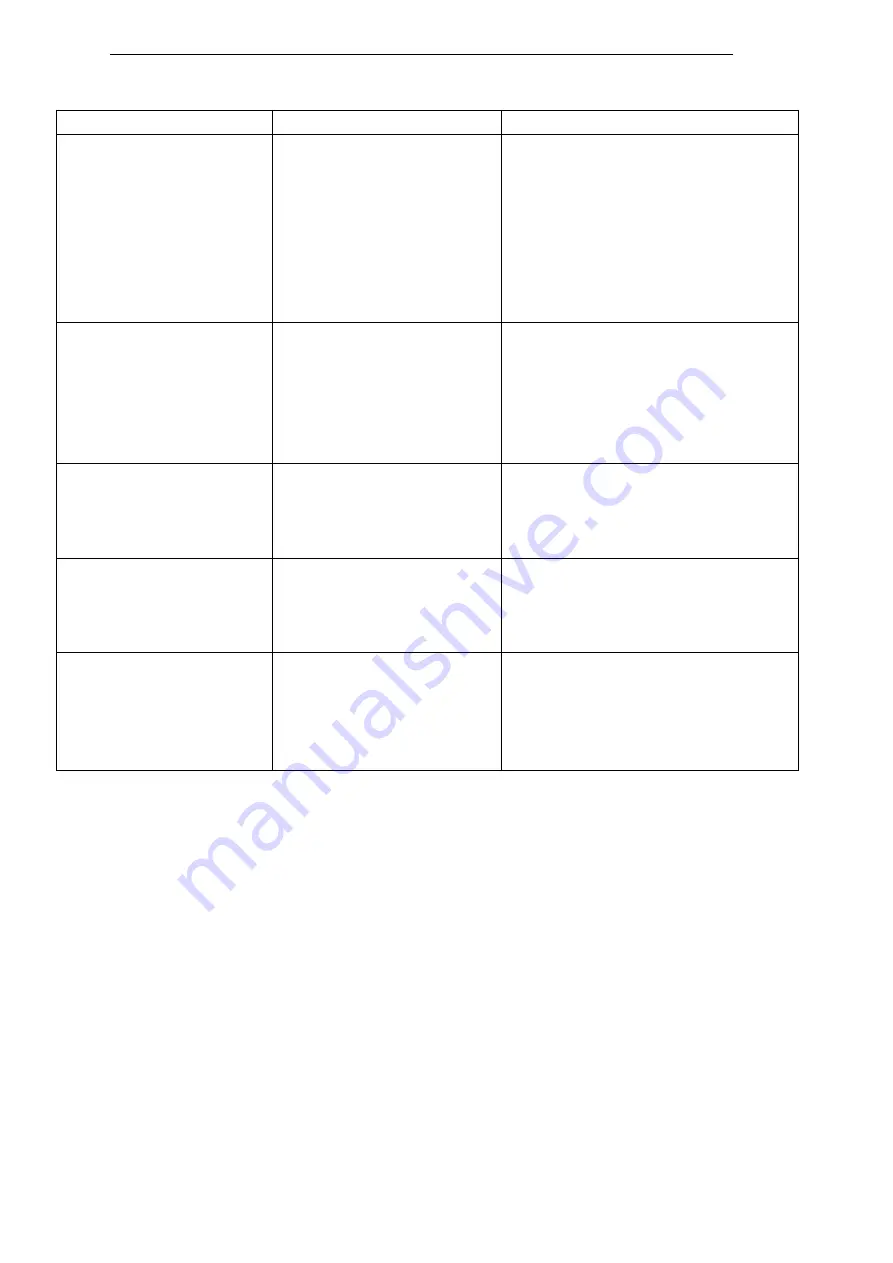
24
7. Resolving abnormalities
Problems
Possible causes
Remedies
Cutting position is deviated
from the color marks
1. Color mark follow up is not
used
2. The film color mark is weak.
3
.
Film is slipping.
1. Change follow up method into “follow up
cut” in the follow up method display of
the human-machine interface.
2. Refer to the magic eye instruction
manual attached to adjust the sensitivity
of the magic eye.
3
.
Adjust the tension of the rubber roller or
the degree of tightness of the brake.
The cutter cut on products
1. The push rod and the cutter are
asynchronous.
2. The height of the cutter seat
is improper.
3
.
Packing speed is too high.
1. Refer to section 4.6.4 about push finger
position.
2
.
Adjust he height of the end-sealing parts,
adjust the sealing knife meshing center to
the half of the product height.
3. Decrease the packing speed.
Burnt crimples appear on the
seal
1. Temperature is too high.
2. Speed is too low.
3. The thermal endurance of the
film’s outer layer is poor.
1. Bring down the temperature.
2. Increase the speed
3. Replace with better film
Sealing is loose or missed
1
.
Temperature is too low.
2
.
Speed is too high.
3
.
The thermal endurance of the
film’s inner layer is poor.
1
.
Increase the temperature.
2
.
Decrease the speed
3
.
Replace with better film.
Thermostat does not control
temperature
1. Heating element is damaged
2. Solid state relay is burnt.
3. Thermocouple is damaged
4.T
emperature control meter
is damaged
1. Replace the heating element.
2. Replace the solid state relay
3. Replace the thermocouple
4. Replace the thermostat