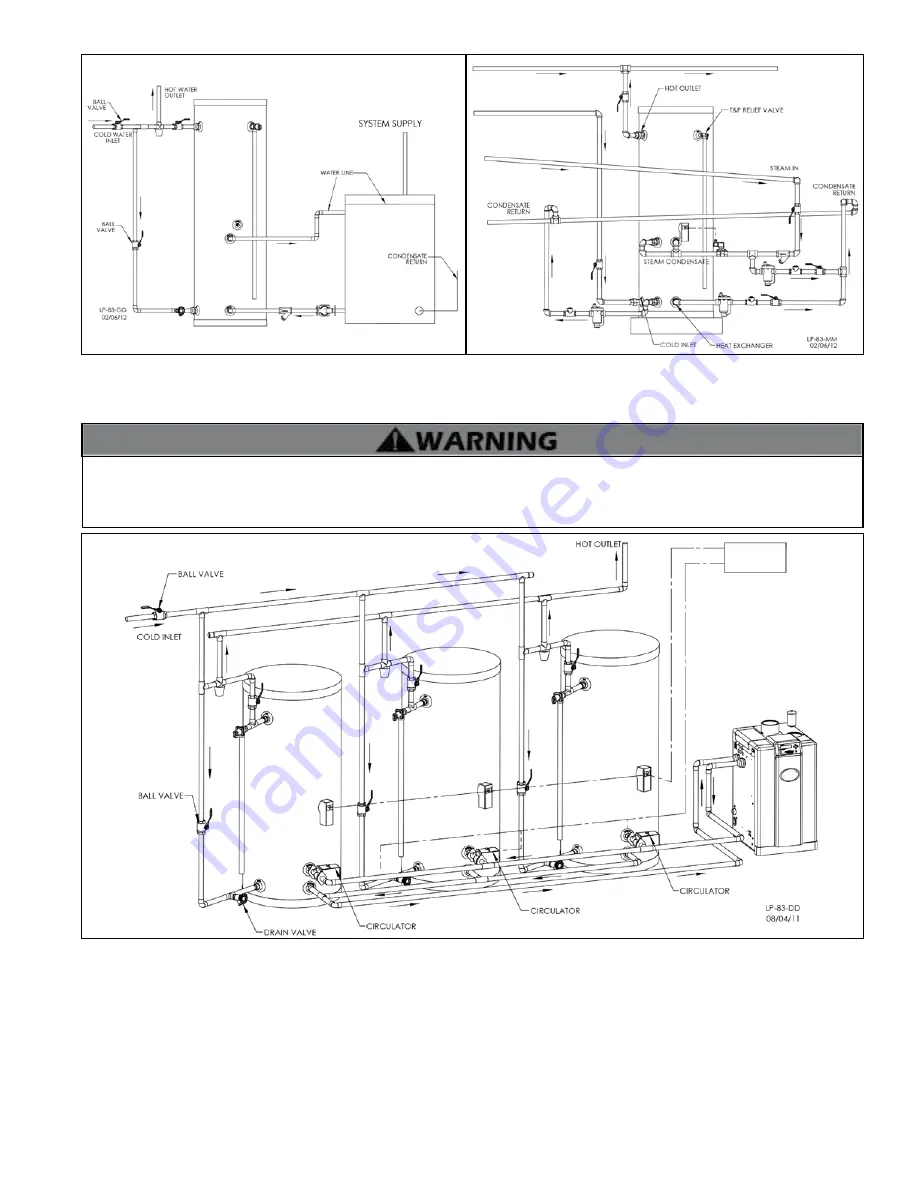
lp-83 Rev. 006 Rel. 005 Date 12.18.17
13
Figure 13 - Steam Boiler
NOTE:
On Steam Boiler Applications, the indirect heat exchanger supply and return connections must be below the water line from the boiler
connection. The internal flow check or spring check must be used to avoid thermal siphoning from the connected boiler. A basket strainer
should also be used to avoid sludge and sediment getting into the pump or heat exchanger.
Figure 14 - Live Steam Installation
Figure 15 - Multiple Tank Installation
NOTES:
1. Minimum pipe size should match connection size. Upsize pipe accordingly if greater flow is required.
2. A thermal expansion tank suitable for potable water must be sized and installed within this piping system between the backflow preventer
and the cold water inlet.
3. All circulators should have an integral flow check.
4. Drains and check valve between heating appliance and water heater will assist in purging air from system.
5. This drawing is meant to demonstrate system piping only. The installer is responsible for all equipment and detailing required by local
codes. In Massachusetts, you must install a vacuum relief valve per 248 CMR.
6. Mixing valve application is optional, but recommended to help prevent scalding. See Part 3, Section E for more information.
7. All piping in parallel used for large dumps of hot water, high usage, and short duration.
8. Massachusetts requires a limit of four (4) tanks per mechanical room. Consult with your local inspector.
Live Steam Applications are allowed ONLY on 80 and 119 gallon SSU / SSU-C models. Using any other SSU model in live steam applications
will result in product failure and void the warranty. Pressure of steam in the indirect heat exchanger MUST NOT EXCEED 10 PSI. Failure to
follow these instructions could result in product failure, substantial property damage, severe personal injury, or death, and WILL VOID
product warranty.