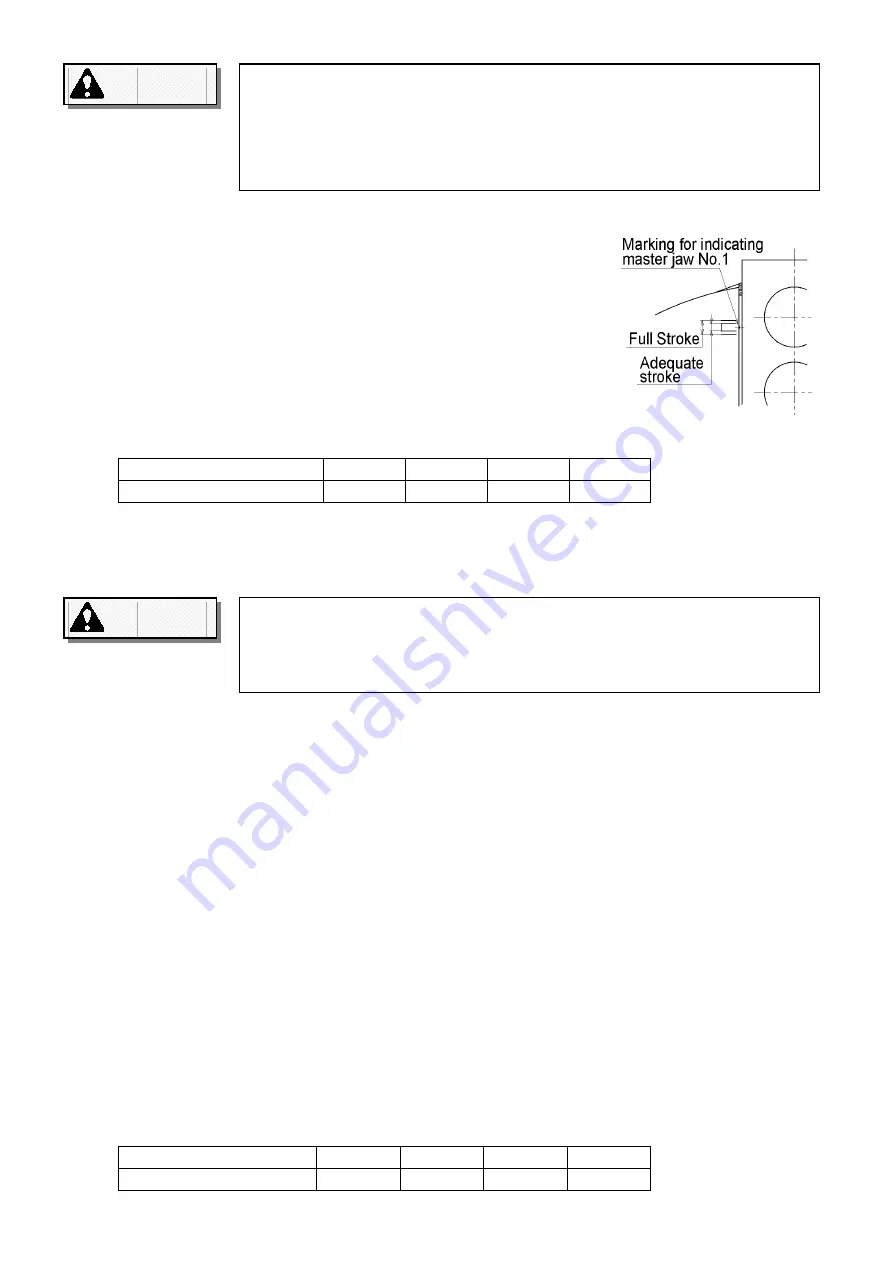
- 8 -
(7) Turn the draw screw with a special wrench, and adjust the
location of the master jaw to the wedge plunger position.
Appropriate location of the wedge plunger at the advance end
is where the dimension A from the clamp face of the pilot
bushing indicated in Fig. 6 becomes the value indicated in
Table 6.
At this time, make sure that the stroke mark of the master jaw
matches the outside line of the full stroke mark.
The draw screw has a click (steel ball and spring for
anti-rotation), and therefore stop the draw screw at a point
where its revolution becomes heavy, and adjust the master jaw position.
Table 6
Chuck size
6
8
10
12
Dimension A (mm)
17.5
21.5
22.5
26
(8) Install the pilot bushing and the top jaws to complete the chuck installation.
(9) If you installed the chuck by screwing the eyebolt into the chuck periphery, remove the bolt.
2.4.7 Inspection
Operational resistance develops when there is some abnormality in the installation procedure. If
the chuck is used without removal of the resistance, parts seizure or abnormal wear may occur,
causing marked shortening of service life. Once the installation has been completed, be sure to
check out the minimum operating pressure. If it is too high, remove the chuck and solve the
trouble.
2.4.8 Balance
When the chuck is additionally machined or equipped with jigs, ensure that the chuck weight is
balanced. Unbalanced chuck will cause vibration and fail to maintain required machining
accuracy.
When machining an unbalanced work piece, take the eccentric mass of the work piece into
consideration and rotate the chuck at a low speed. This is because the centrifugal force due to
eccentric mass applies to the top jaws.
The chuck balance described in this manual is based on the standard balance quality (4 mm/s)
defined in JIS B0905-1992, and the unbalance amount of the chuck periphery is specified as
shown in Table 7.
(International Standards that correspond to JIS B0905-1992 are ISO1940-1: 1986 and
ISO8821: 1989.)
Table 7
Chuck size
6
8
10
12
Max. unbalance (g)
2
3
4
6
Fig. 7
WARNING
WARNING
Fasten the chuck installing bolts with recommended tightening
torque.
If the torque is largely different from the recommended value, lower or
higher, the bolts may break and the chuck and/or work piece may fall out;
this presents a hazard that may cause severe personal injury or death to
the operator or bystanders.
Be sure remove the eyebolt, when the installation is carried out
with using an eyebolt.
If you rotate the chuck with the eyebolt being screwed, you may be
caught by the part of your body or clothing and get injured.
Содержание H3KB
Страница 4: ...2 M5 M M8 M10 M12 M16 M20 N m 7 1 12 1 29 4 57 9 101 161 251...
Страница 5: ...3 8 1 4 1 EP...
Страница 6: ...4 1 1 1 1 1 1 1 1 H3K H3K H3K H3KB B B B JIS A5 A6 A8 A11 6 8 10 12 1 2 1 2 1 2 1 2 2 1 2 1 2 1 2 1...
Страница 11: ...9 3 1 3 1 3 1 3 1 3 3 3 3 H 8...
Страница 12: ...10 O 6 1 8 8 M10 M12 M16 57 9 101 161 2 2mm 3 3 3 3 3 3 3 3 1 4 1 4 1 4 10 No 1 2 7 11 8 2 2 2 2 2 1 9 10...
Страница 13: ...11 11 D D d d D d 0 75 D D d d D d 0 75 D D d d H7 1 6a d d h6 1 6a...
Страница 14: ...12 12 13 3 4 3 4 3 4 3 4 3 5 3 5 3 5 3 5 VDI No 3106 VDI No 3106 VDI No 3106 1 3 1 3 1 3 1 3 12 13...
Страница 15: ...13 3 5 1 3 5 1 3 5 1 3 5 1 3 5 2 3 5 2 3 5 2 3 5 2 6 3 6 3 6 3 6 3 6 ANSI B11 6 ANSI 1 2 1 2 1 2 1 2 14...
Страница 18: ...16 4 1 4 1 4 1 4 1 EP 8 1 4 1 EP 100 0004 1 5 1 23F TEL 0120 77 6278 FAX 03 3287 1203 4 2 4 2 4 2 4 2 1000...
Страница 19: ...17 4 3 4 3 4 3 4 3 ANSI B11 6 1984 section 7 1 9...
Страница 21: ...19...
Страница 50: ......
Страница 51: ......
Страница 52: ......