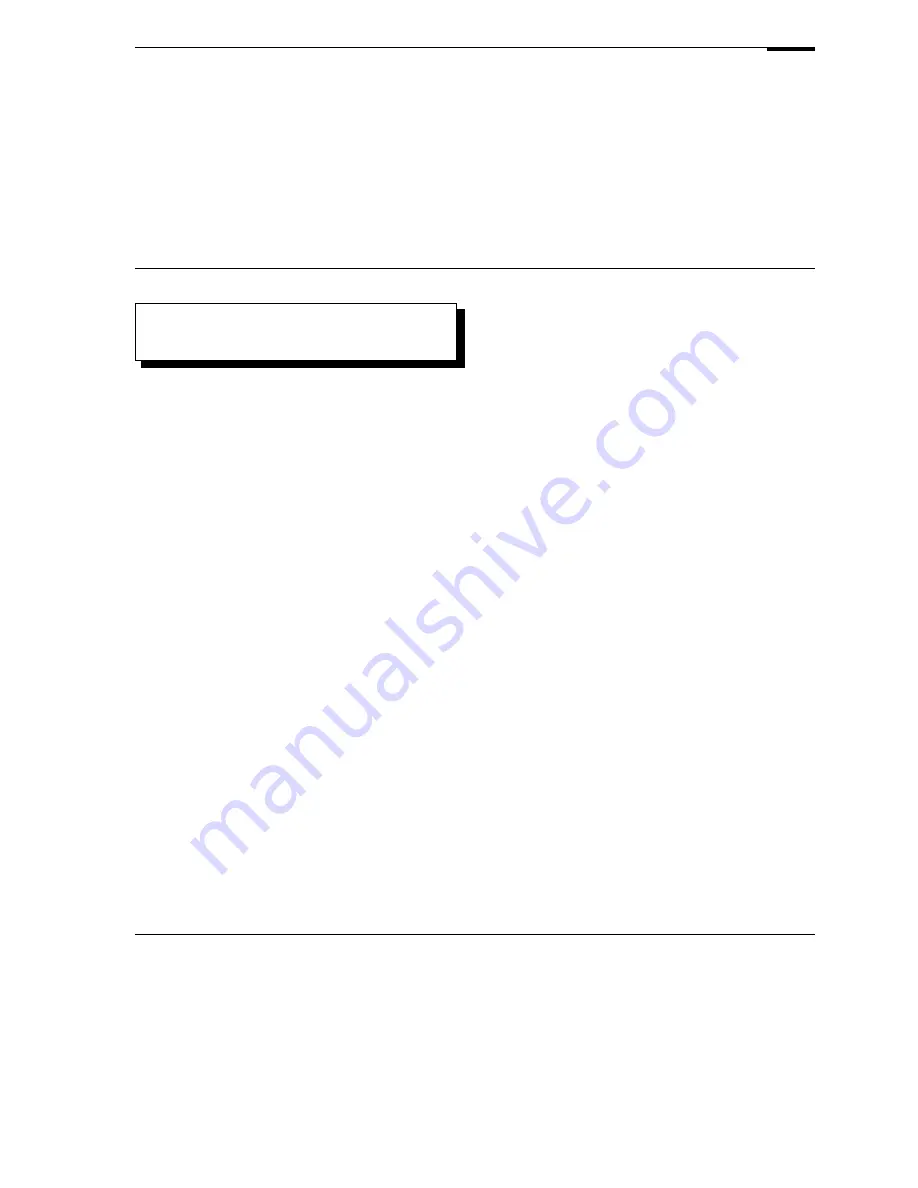
13
Fitting the Burner
Fitting the Burner
The burner is normally attached to the boiler and is
pre-wired. In the event that the burner is supplied
separately, then the following procedure should be
used. An adaptor plate suitable for the type of burner
being used is supplied fitted to the boiler door.
Important
Check from the nameplate that the burner received
is the one indicated on the advice note and that the
electrical supply details and the fuel shown agree with
those available on site.
Most burners can be lifted manually, but care should
be taken not to damage components and help should
be sought for handling the larger burners.
Fitting the burner
• Fit the burner to the door using the gasket
and studs provided. If an acoustic shroud with
a backplate is being used, refer to the notes
below before fitting the burner.
• When the burner is securely fixed, check that
the boiler door will open fully 90
o
.
• In the case of oil fired burner, the position of
the oil strainer at the end of the fixed oil supply
pipe should allow the door to open fully when
the flexible oil piping is connected.
Dual fuel burners - important note
For dual fuel burners, the installer should fit solenoid
oil supply valves with micro switches to interlock with
the burner and similarly the gas supply valve should
have micro switches.
Check for shrouds with wheels that space has been
allowed to wheel the shroud away from the burner on
a flat and level floor in front of the burner.
Fire Sensor for gas or oil burners
This should be located just in front of the boiler door
and above it so that the door can be opened without
hindrance. This applies whether an acoustic shroud
is fitted or not.
For dual fuel burners which do not have a clutch
release system for the oil supply when operating on
gas, arrangements should be made to circulate the oil
through flexible piping for at least 5 metres so that the
pump does not overheat.
Gas burner valve trains should be located within
300mm of the burner and supported independently of
the boiler at the opposite side to the door hinge so that
the door can open after 'breaking' a connecting joint.
Sealing of the burner draught tube
A small annular space is necessary around the burner
draught tube in the door refractory to enable the burner
to be withdrawn. Seal this gap with the ceramic strip
supplied.
Acoustic Shrouds
Acoustic shrouds are available to special order for the
burner and gas booster.
Check that the shroud instructions for fitting and space
requirements are to hand and studied before fitting.
These instructions are not in this manual.
Water flow & return temperatures
Consideration will already have been given to the system flow and return temperatures but please note:-
1) The flow temperature can be adjusted to the maximum operating temperature, as outlined in page 5.
2) The return temperatures should be controlled to be not less than 60
o
C for oil and 55
o
C for gas at all times
by the use of suitable bypass/diverting controls.
3) Differentials between the flow and return should not exceed 25K. Where a differential is to exceed 20K
advise Hoval as considerations are necessary and alternative solutions can be suggested.
Burner matching
The boiler will normally be supplied by Hoval complete with a burner which is CE marked and is CE approved
for firing with the boiler. Where it is required to fit an alternative burner, to comply with CE Directives, the boiler
must only be used with a burner having CE marking in accordance with Directive 90/396/EEC and Standard
EN 676 (Gas) or EN 267 (Oil). The fuel suppy requirements will be stated on the burner data plate.
The burner CE approval must also be based on a test in a test tank having dimensions no larger than the rel-
evant boiler combustion chamber dimensions.
Please consult Hoval Technical Department for further information, if required.
Always fit the front casing before burner on
SR plus boilers up to and including the SR
plus 600.
August 2014