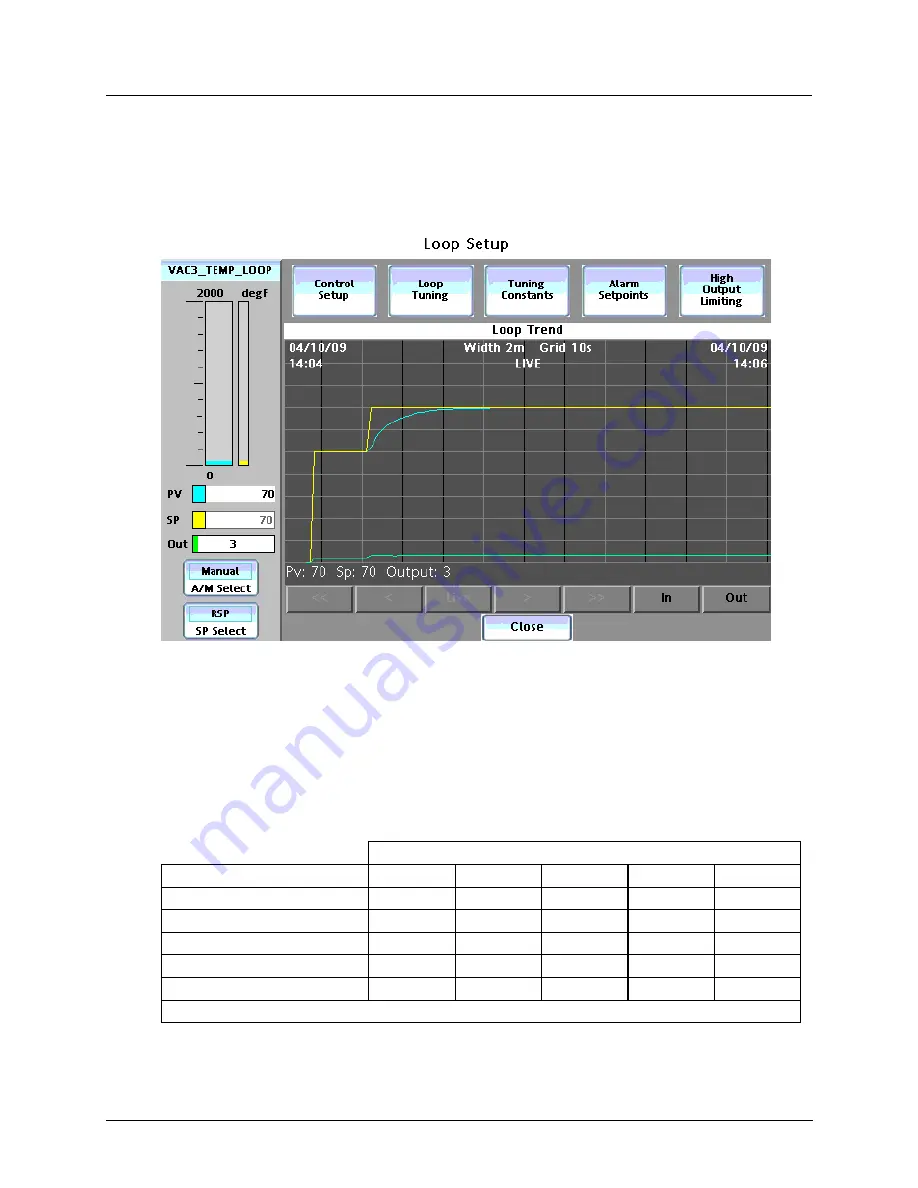
Loops
Loop Setup
148
900 Control Station User Guide
Revision 9
May 2014
Loop Setup
Overview
All the loop widgets let you jump to the Loop Setup display. See example below.
Above is an example of the PID Loop Setup display. At left is the loop widget, with operable buttons and
parameters.
At bottom is a loop trend. The points on the trend typically correspond to PV, SP and Output, whose pen
colors match the values on the left (aqua, yellow, green). Additional points of different colors may be
visible, depending on configuration. Use the gray buttons at the bottom to navigate and zoom.
At the top are buttons that take you to detailed popups for various loop parameters. Buttons are accessible
depending on the loop type, shown below.
Loop type
Button
PID
ON/OFF
3 POS
CARBON
A/M BIAS
Control Setup (p. 150)
X
X
X
X
X
Loop Tuning (p. 151)
X
X
X
Tuning Constants (p. 155
X
X
X
Alarm Setpoints (p. 156)
X
X
X
X
X
High Output Limiting (p. 157)
X
X
X indicates button is accessible
Содержание ControlEdge 900 platform
Страница 128: ...116 900 Control Station User Guide Revision 9 May 2014 This page is intentionally left blank ...
Страница 170: ...Loops Loop Setup 158 900 Control Station User Guide Revision 9 May 2014 This page is intentionally left blank ...
Страница 191: ...Revision 9 900 Control Station User Guide 179 May 2014 ...