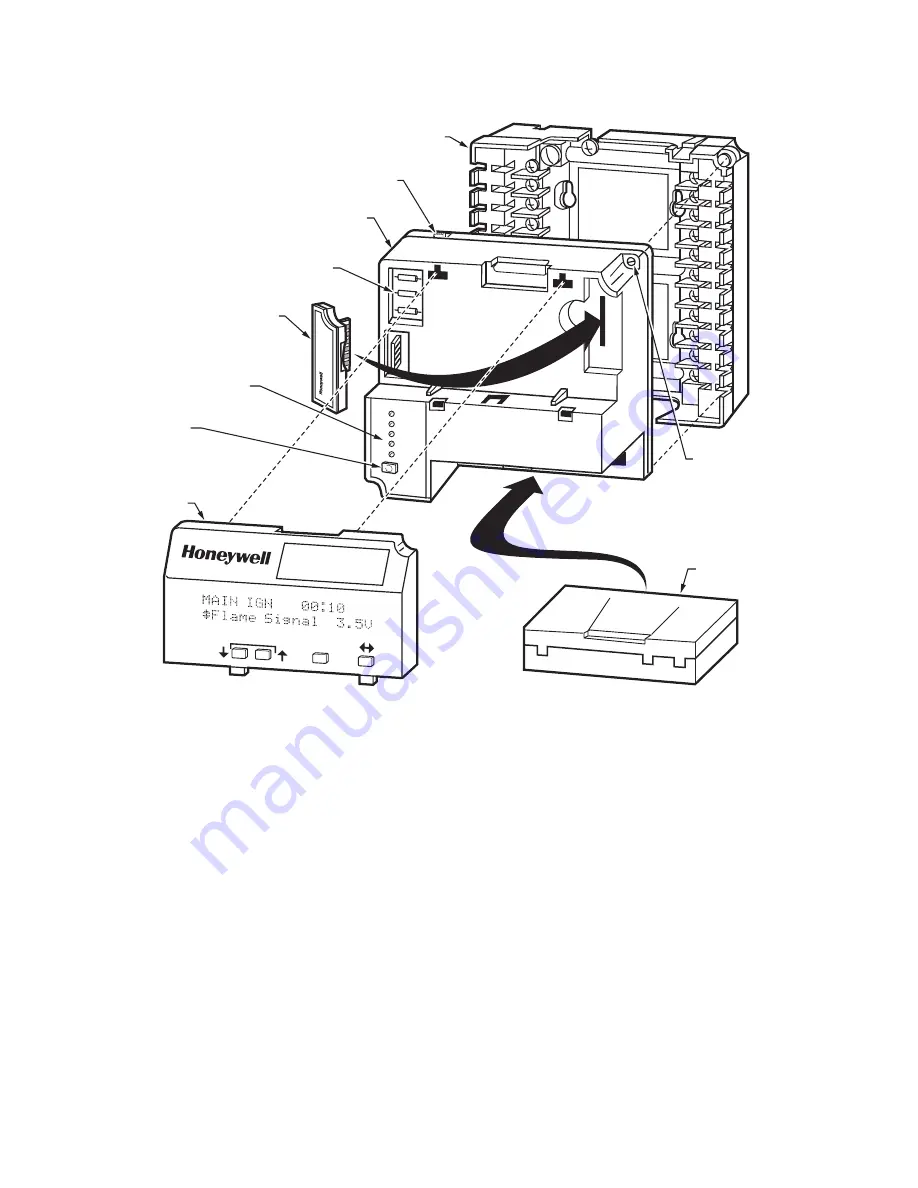
RM7800L1087; RM7840G1022,L1075; EC7840L1014 RELAY MODULES WITH VALVE PROVING
66-1162—2
12
Fig. 8. RM7800L/40L, EC7840L Relay Module exploded view.
VALVE PROVING SYSTEM
The Valve Proving System feature provides a systematic way
of testing the valve seat integrity to assure the valves are in
the closed state whenever the sequence of operation requires
them to be closed. It is designed to detect a leak greater than
0.1% of the burner input capacity. For example, a 10 million
Btu/hr natural gas-fueled burner would have a fuel input
capacity of approximately 1,000 ft
3
/hr. A leak rate greater than
0.1% of 1,000 ft
3
/hr or 1 ft
3
/hr in either valve will be detected
with the Valve Proving System. Smaller leaks will not be
detected.
At commissioning time, the Valve Proving System may be
scheduled to occur at one of five different times: Never,
Before, After, Both, and Split.
Never
—Device default as received: in this case Valve
Proving does not occur.
Before
—Valve Proving occurs concurrently with Pre-
Purge.
After
—Valve Proving occurs after the Run state before the
internal Safety Relay dropout state and concurrent with
Post Purge (if configured).
Both
—Valve proving occurs at both times Before and After
noted above.
Split
—The downstream seat (high pressure) test is per-
formed at the Before time and the upstream seat (low
pressure) test is performed during the After time.
The Valve Proving items programmed are:
1.
Specify when to perform Valve Proving. Demand input
to terminal 17 actually enables the function of Valve
Proving.
2.
Specify the time duration of the test (calculated from
Appendix A).
HONEYWELL
POWER
PILOT
FLAME
MAIN
ALARM
RESET
KEYBOARD
DISPLAY
MODULE
(STANDARD ON
RM7800E,G,L,M)
PURGE
TIMER
WIRING
SUBBASE
CAPTIVE
MOUNTING
SCREW
RUN/TEST
SWITCH
CONFIGURATION
JUMPERS
RELAY
MODULE
SEQUENCE
STATUS
LED PANEL
RESET
BUTTON
FLAME
AMPLIFIER
SCROLL
MODE
- SAVE -
BURNER CONTROL
M16353