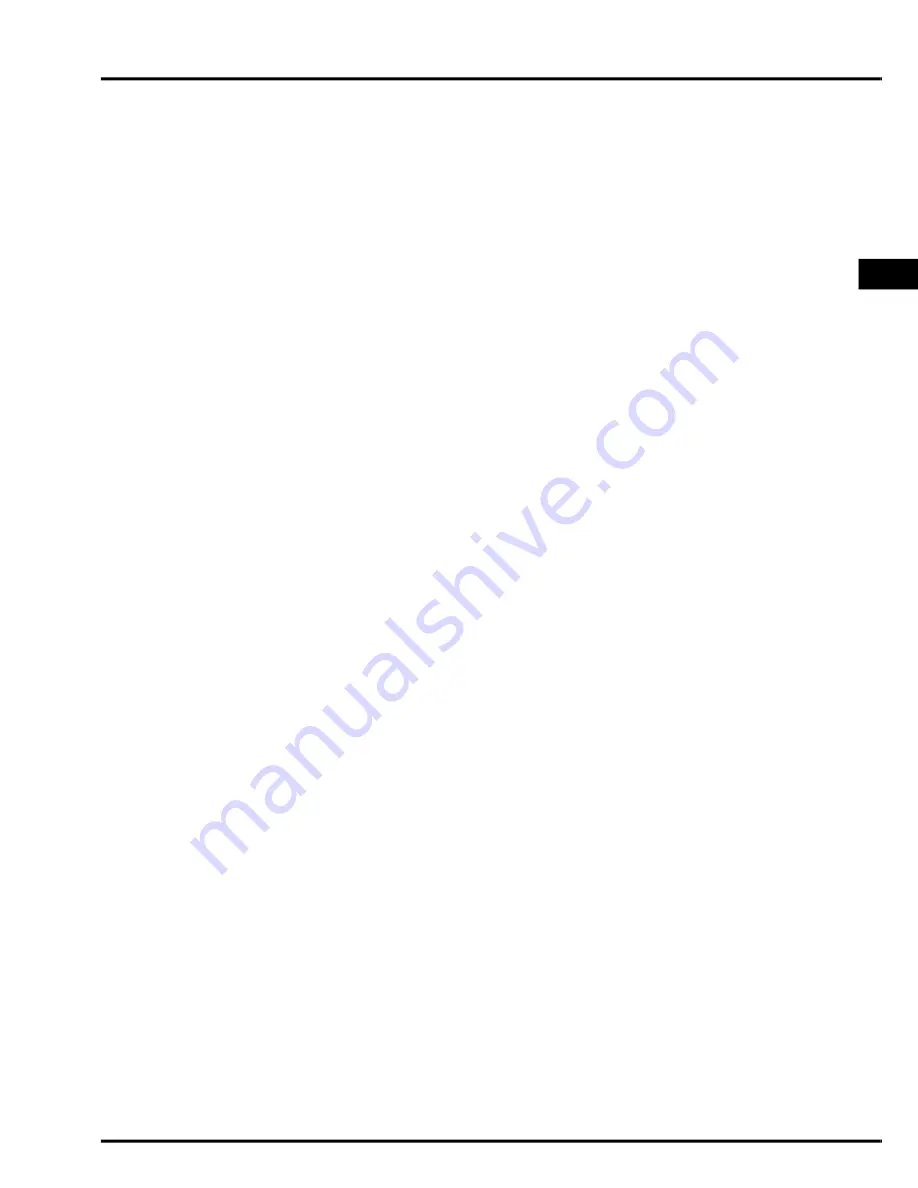
5-1
5
dummytext
TOOLS ················································ 5-2
FUEL TANK REMOVAL/INSTALLATION ··· 5-3
REMOVAL/INSTALLATION ····················· 5-4
REMOVAL/INSTALLATION ····················· 5-5
DISASSEMBLY/ASSEMBLY···················· 5-6
CARBURETOR BODY CLEANING ··········· 5-7
CARBURETOR INSPECTION ·················· 5-7
PILOT SCREW REPLACEMENT ·············· 5-8
Содержание FQ650
Страница 7: ...MEMO ...
Страница 13: ...SPECIFICATIONS 1 6 WIRING DIAGRAM R SPARK PLUG Bl R Bl UNIT IGNITION COIL ENGINE STOP SWITCH Bl BLACK R RED ...
Страница 21: ...SERVICE INFORMATION 2 8 TUBE ROUTING FUEL TUBE BREATHER TUBE HIGH TENSION CORD ...
Страница 37: ...MEMO ...
Страница 43: ...MEMO ...
Страница 45: ...FUEL SYSTEM 5 2 FUEL SYSTEM TOOLS Float level gauge 07401 0010000 ...
Страница 53: ...MEMO ...
Страница 67: ...MEMO ...
Страница 74: ...9 1 9 dummytext 9 MUFFLER MUFFLER REMOVAL INSTALLATION 9 2 ...
Страница 76: ...10 1 10 dummytext 10 ENGINE REMOVAL INSTALLATION ENGINE REMOVAL INSTALLATION 10 2 ...
Страница 78: ...11 1 11 dummytext 11 CLUTCH PULLEY V BELT REMOVAL INSTALLATION 11 2 ...
Страница 81: ...MEMO ...
Страница 111: ...MEMO ...
Страница 129: ...MEMO ...