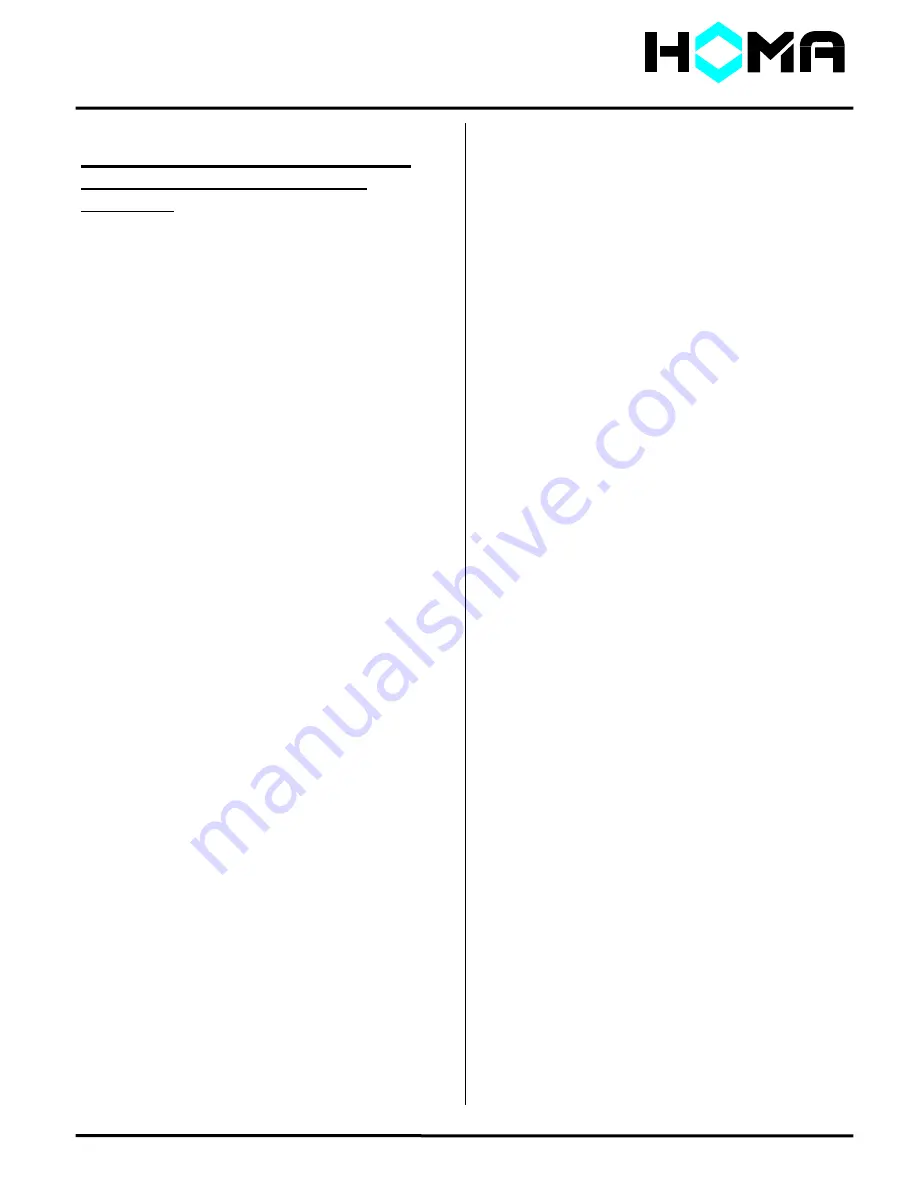
CH Series
Installation, Operation & Maintenance Manual
MECHANICAL INSTALLATION:
PUMPS WITH AUTOCOUPLING
SYSTEMS
In the AutoCoupling installation mode the pump
is installed on a stationary component and
operates completely or partially submerged
(min. 8” above volute) in the pumping media.
The HOMA AutoCoupling kit base, guide claw
flange, upper guide rail bracket, profile seal.
Refer to dimensional drawing for details.
For Threaded Discharge CH Series pumps,
attach the guide claw flange to the pump
discharge flange as follows:
1. Inspect threaded assemblies for damage.
2. Clean threaded portions of pump discharge
flange and guide claw flange.
3. Apply hardening thread sealer (for example
Loctite thread locker 242) to pump discharge
threads.
4. Thread guide claw flange on to pump
discharge fully.
DISCHARGE THREADS ARE
NOT NPT. DO NOT OVER TIGHTEN.
5. Loosen guide claw flange full turn to expose
some threads.
6. Re-apply sealant on exposed threads .
7. Tighten guide claw flange until the claw is in
upright (horizontal) position.
For Flanged Discharge CH Series pumps, attach
the guide claw flange to the pump discharge
flange with the fasteners and gaskets
recommended in the accessory fastener
selection table. Use tightening torque’s indicated
in the table.
Install suitable lifting chain of an adequate size
and length to permit proper lowering and raising
of the pump. Lower the pump into the area
where it is required.
Install upper guide bar bracket as shown on
outline drawing located in the appendix. Do not
tighten mounting bolts completely at this point.
Properly locate the base anchor bolts into the
floor of the pump station. Make sure when
locating and securing the anchor bolts that the
base will align properly with the access cover at
the top elevation of the station.(Refer to outline
drawing in appendix). Place the base in position,
and level the base.
If base is not level, proper
sealing of the pump to base will not occur!
Fully tighten all anchor and mounting bolts, and
verify that the profile seal is in position.
Place the guide rails in to the rings of the base
and cut them to a length that will allow the rails
to be secured at the top of the pump station with
the upper guide bar bracket and to extend down
to the sump floor. Loosen bracket mounting
bolts, install guide pipes into bracket and tighten
mounting bolts.
For stations exceeding ten feet
in depth intermediate guide bar brackets are
recommended. One bracket is recommended for
each additional 10 feet of station depth.
Check that the guide system is properly installed
in the vertical orientation by using levels and a
plumb line. Connect the station riser piping to
the outlet flange of the base.
Before lowering the pump, verify the direction of
impeller rotation (refer to start-up section for
procedure).
Also it is recommended that the
stationary fitting be visible before lowering the
unit. If this is not possible, ensure all debris is
removed from wet well.
Make sure to use lifting equipment that has
adequate capacity for the pump that will be
handled.
Before installing pump, check to be
certain the profile seal (rubber ring) is properly
positioned in the guide claw flange. Lift, then
position pump so the guides on the discharge
flange engage the rails. Slowly lower the pump
along the guide rail. Once the pump reaches its
bottom location it will automatically connect to
the base.
Pg. 4