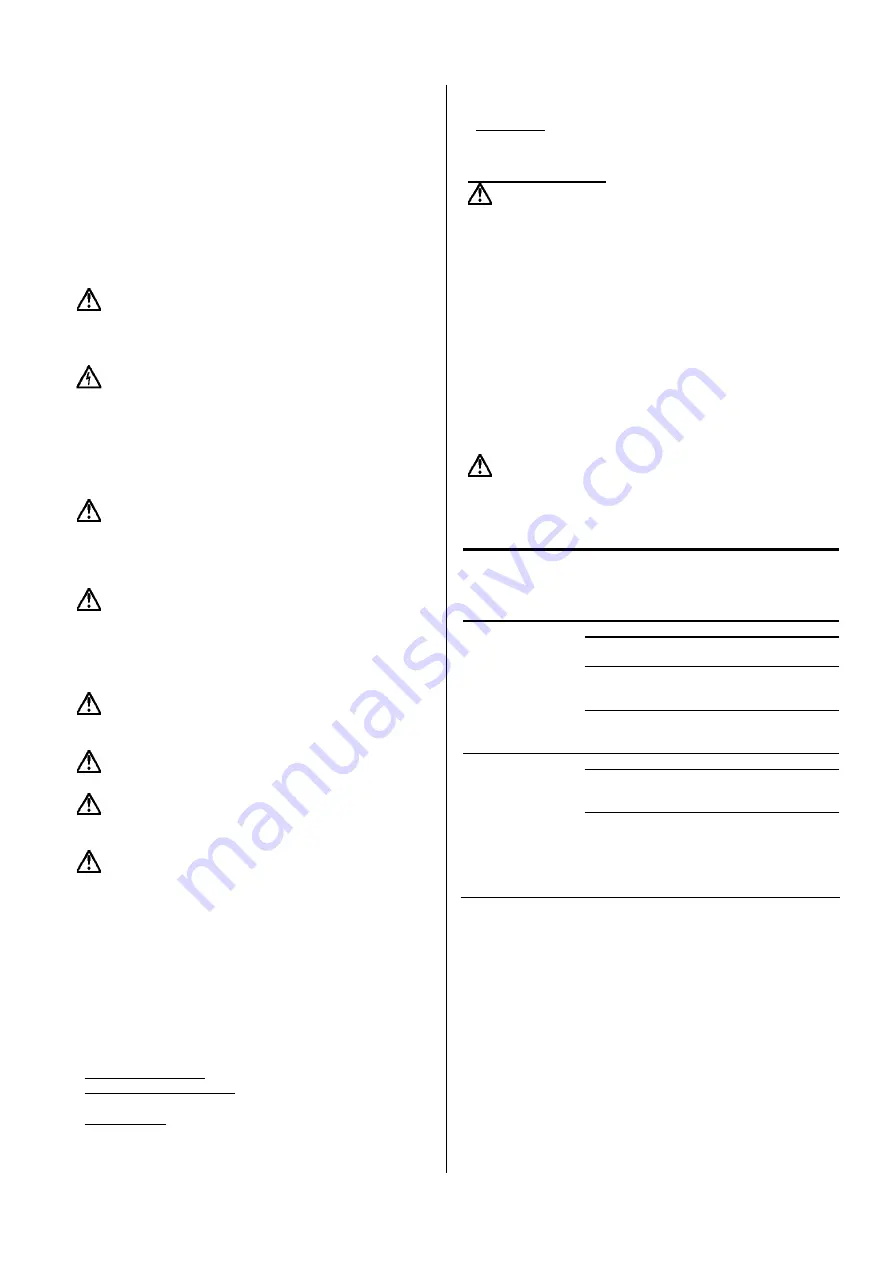
10
In order to prevent a return of the water by disconnected
pump, additionally a check valve should be installed. The
discharge pipe must be installed without tension.
The pump may be installed with a flexible discharge hose
or a rigid pipe, non-return valve and isolating valve. If a
flexible hose is used, make sure that the hose has the
same diameter like the pump discharge and does not
buckle.
Fix a rope or a chain to the pump handle and lower the
pump into the liquid. If the pump is installed on muddy
ground, support it on bricks to prevent it from sinking in.
Pay attention to the maximum depth of immersion
(see pump label).
8. Start-Up
Never let the pump run dry for a long time of period,
as it will destroy the pump (danger of overheating).
Open the isolating valves. Connect the pump with the
mains supply. C 135 W starts running irrespective of the
liquid level.
9. Maintenance and Repair
In case of a defect of the pump, a repair shall be
carried out only by the manufacturer or through an author-
ized workshop. Modifications of the pump must be con-
firmed by the manufacturer. Only HOMA spare parts shall
be used.
In accordance with the product liability law we point
out that we shall not be liable for damages caused by our
product due to unauthorized repair by persons other than
the manufacturer or an authorized workshop or due to the
use of spare parts other than original HOMA parts. The
same product liability limitations are valid for accessories.
Before maintenance or repair disconnect the pump
from the power supply to avoid accidental starting of the
pump!
Before maintenance or repair make sure that all rotat-
ing parts stand still!
Before carrying out maintenance and service, the
pump must be thoroughly flushed with clean water. Rinse
the pump parts in clean water after dismanteling.
At pump types with oil chamber an overpressure can
escape with loosening of the oil chamber control screw.
Screw only when pressure balance took place.
Pumps running under normal operation conditions should
be inspected at least once a year. If the pumped liquid is
very muddy or sandy or if the pump is operating continu-
ously, the pump should be inspected every 1.000 operat-
ing hours.
For long and trouble-free operation of the pump, following
points should be checked regularly:
- Nominal current (A): Check with amp-meter.
- Pump parts and impeller: Check for possible wear.
Replace defective parts.
- Ball bearings: Check the shaft for noisy or heavy opera-
tion (turn the shaft by hand). Replace defective ball bear-
ings. A general overhaul of the pump is usually required in
case of defective ball bearings or poor motor function.
This work must be carried out by an authorized
service workshop.
- Cable entry: Make sure that the cable entry is watertight
and that the cables are not bent sharply and/or pinched.
Contaminated pumps
If a pump has been used for a liquid which is injurious
to health or toxic, the pump will be classified as contami-
nated.
If HOMA is requested to service the pump, HOMA must
be contacted with details about the pumped liquid, etc.
before the pump is returned for service. Otherwise HOMA
can refuse to accept the pump for service (see attache-
ment).
Possible costs of returning the pump are paid by the cus-
tomer. However, any application for service (no matter to
whom it may be made) must include details about the
pumped liquid if the pump has been used for liquids which
are injurious to health or toxic.
10. Fault Finding Chart
Before maintenance or repair disconnect the pump
from the power supply to avoid accidental starting of the
pump!
Fault Cause Remedy
Motor does not start.
•
Supply failure;
short-circuit; earth-
leakage; fault in
cable or motor
winding
•
Have the cable and
motor checked and
repaired by a quali-
fied electrician
Pump operates at
•
Voltage drop
•
Check the voltage
•
Leakage in the
discharge pipe
•
Check the discharge
pipe and seal up
•
Suction sieve
blocked by impuri-
ties
•
Clean the suction
sieve
below-standard
performance
•
Pump does not
reach the required
head
•
Compare the pump
performance with
the required head
Pump operates, but
•
Voltage drop
•
Check the voltage
motor starter trips
out after a short
while
•
Impeller is blocked
by impurities
•
Clean the impeller
•
Temperature of the
pumped medium is
too high
•
Please check the
temperature of the
medium. The tem-
perature of the
pumped medium
must be < 35
o
C