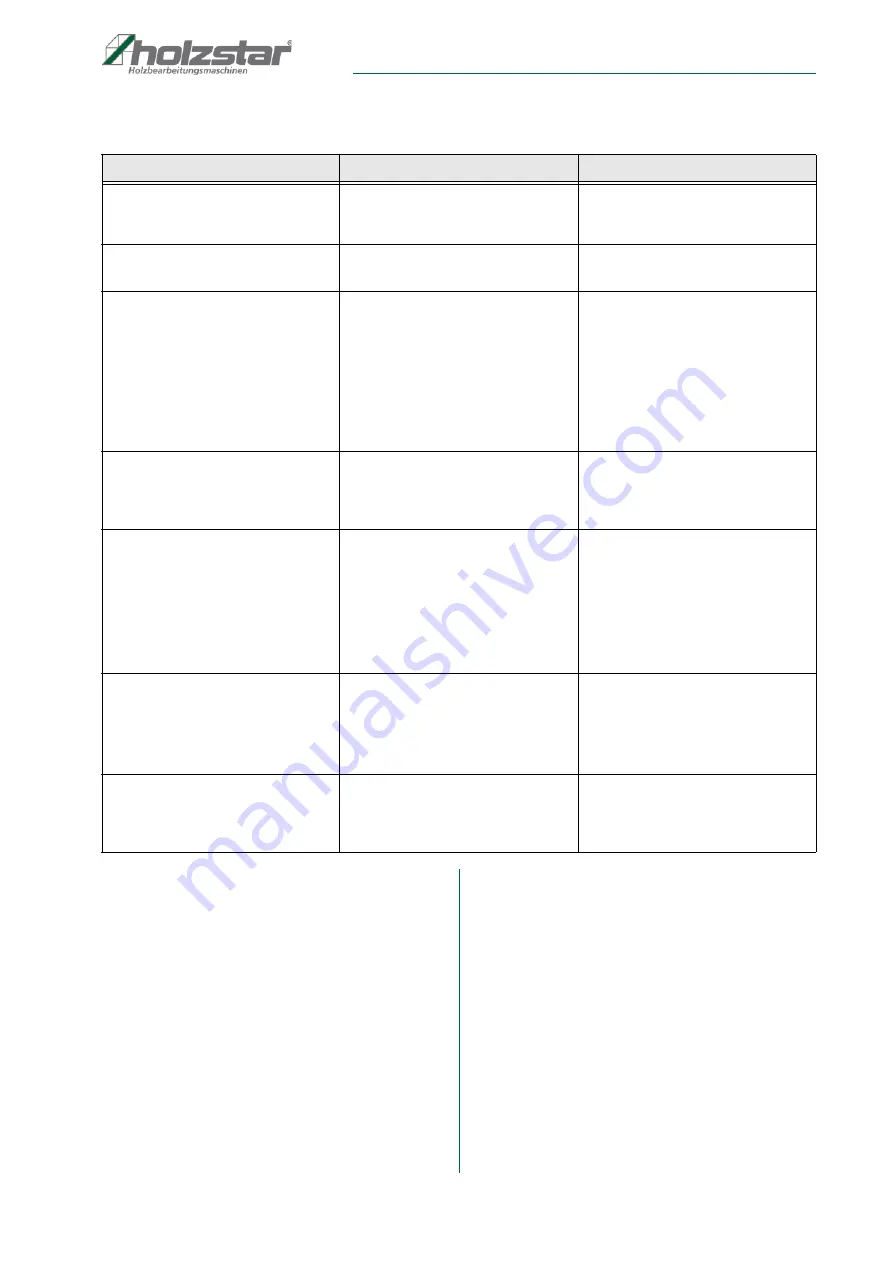
Troubleshooting
TKS Serie | Version 1.04
21
15 Troubleshooting
16 Disposal, recycling of used devices
For environmental benefits it is necessary to ensure that
all components of the machine are only disposed of by
the provided and allowed means.
16.1 Decommissioning
Immediately decommission used machines in order to
avoid later misuse and endangering of the environment
or of persons.
Step 1: Dispose of all environmentally hazardous oper-
ating materials of the used device.
Step 2: If required, disassemble the machine into easy-
to-handle and usable components and parts.
Step 3: Supply the machine components and operating
materials to the provided disposal routes.
Error
Possible causes
Solution
Engine does not start
1. No mains voltage
2. Connection cable defective
3. Engine defective
Have the power connection checked
by qualified personnel.
Engine is running, saw blade is not
turning
Drive shaft defective
Replace the drive shaft
Engine is getting hot
1. Motor short circuit
2. Overload of the engine
1.Disconnect the power plug and
have the machine repaired by qua
-
lified personnel.
2. Check that the saw blade is
suitable for the material to be
cut.Check if the saw blade is still
sufficiently sharp.Take a break
from work and let the engine cool
down.
Saw blade speed too low
1. Engine defective
2. Too low mains voltage
1. Check the engine by qualified per
-
sonnel.
2. Check the mains voltage by quali
-
fied personnel
Saw vibrates, saw blade strikes
1. Saw blade does not match the
specification
2. Saw blade not sufficiently secured
3. Saw blade defective
1. Check on the basis of the specifi
-
cations in the technical data
whether the saw blade is suitable
for installation.
2. Tighten the fixing screw.
3. Check the saw blade for mechani
-
cal damage and replace it if neces
-
sary.
No clean 45 ° or 90 ° cuts
1. Stops not aligned correctly
2. Angle display not set correctly
1. Check the saw blade with stan
-
dard angle and align the stops.
2. Check saw blade with standard
angle and adjust angle display.
Workpiece is knocked back by the
saw blade.
1. Stops not aligned correctly
2. Disconnect blade not aligned with
saw blade
3. Defective saw blade
1. Align the stops.
2. Align the cutting blade with the
saw blade.
3. Replace the saw blade.
Содержание TKS 200
Страница 33: ...Notes TKS Serie Version 1 04 33 20 Notes ...
Страница 34: ...www holzstar de ...