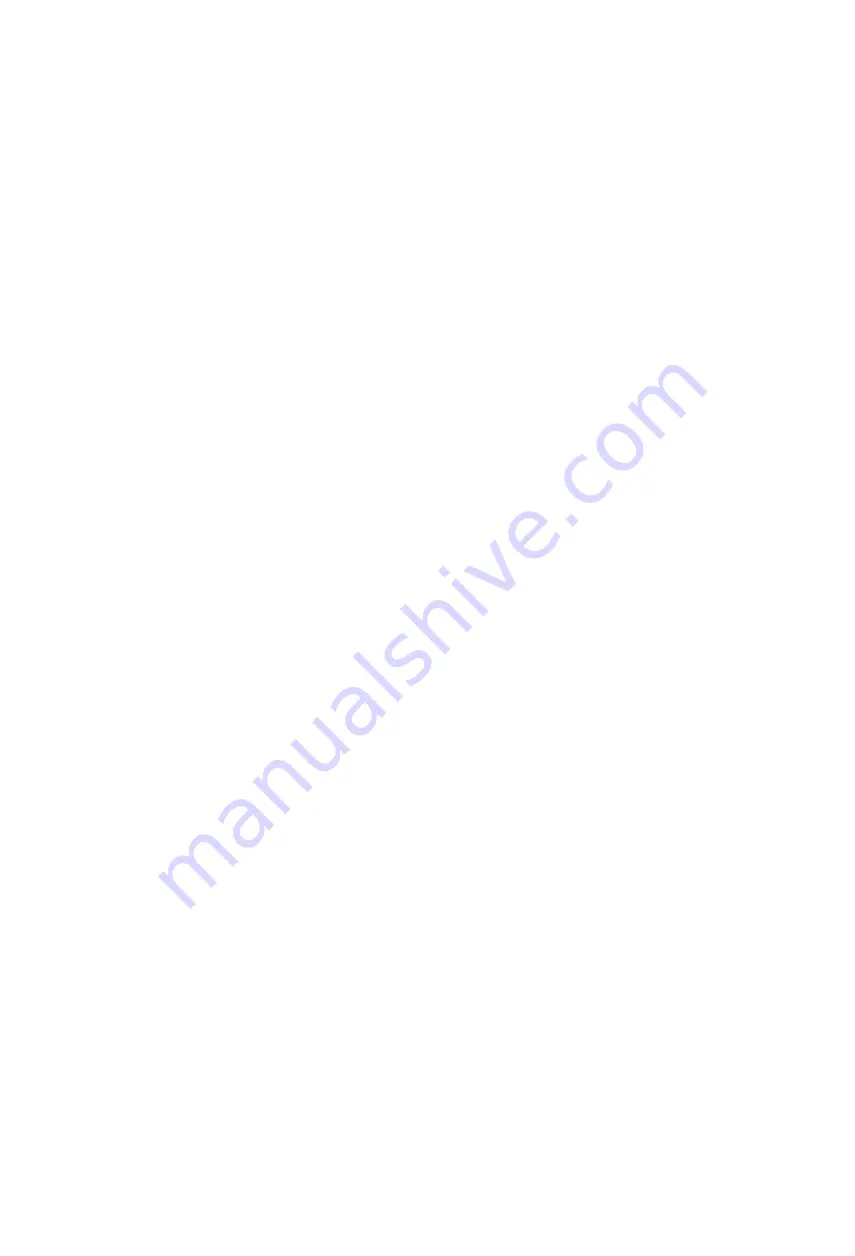
GEN III V8 ENGINE MANAGEMENT
ELECTRONIC TRACTION CONTROL
When the ABS/ETC control module senses spin from the drive wheels due to too much engine torque for the
road conditions, it enters the traction control mode.
The ABS/ETC module monitors both front and rear wheel speeds through the wheel speed sensors. If at any
time during acceleration the ABS/ETC module detects drive wheel slip, it will request:
• The PCM, via the spark retard circuit, to retard the amount of spark advance.
• The PCM, to restrict transmission downshifting.
• The throttle relaxer control module to reduce the engine throttle opening by a certain percentage to bring
engine torque into a specific range.
The throttle relaxer control module accomplishes this by commanding the throttle relaxer to override the
accelerator pedal cable and physically reduce the throttle body butterfly opening by winding the throttle
cable back.
This is achieved via two high speed Pulse Width Modulated (PWM) circuits between the ABS/ETC module
and the throttle relaxer control module. The ABS/ETC control module sends a message to the throttle
relaxer control module on the requested throttle position (DKR) circuit. The throttle relaxer control module
then reports the modified throttle position opening back to the ABS/ETC control module via the actual
throttle position (DKI) circuit.
Simultaneously with engine spark retard and throttle position intervention, the ABS/ETC control module will
activate the ABS isolation valves, turn on the ABS pump motor and supply brake pressure to the over spinning
wheel(s).
The isolation valves isolate the front brake hydraulic circuits from the master cylinder and rear brake hydraulic
circuits. Once the rear brake hydraulic circuits are isolated, pressure can be applied to the rear wheels without
affecting any other brake hydraulic circuits. The ABS/ETC module opens the priming valve, allowing fluid to be
drawn from the master cylinder to the pump motor, turns on the ABS pump motor to apply pressure, begins
cycling the ABS assembly's inlet and outlet valves, and closes the switching valve, ensuring fluid is directed to
the wheel not back into the master cylinder.
The inlet and outlet valve cycling aids in obtaining maximum road surface traction in the same manner as the
Anti-Lock Brake mode. The difference between Traction Control and Anti-Lock Brake mode is that brake fluid
pressure is increased to lessen wheel spin (Traction Control mode), rather than reduced to allow greater wheel
spin (Anti-Lock Brake mode).
If at any time during Traction Control mode, the brakes are manually applied, the brake switch signals the
ABS/ETC module to inhibit brake intervention and allow for manual braking (throttle reduction and spark retard
intervention can still occur if necessary).
Engine Spark and Throttle Position Intervention
Simultaneously to brake intervention, the ABS/ETC control module communicates with the Powertrain Control
Module (PCM) and the throttle relaxer control module requesting the PCM to retard the spark advance and for
the throttle relaxer control module to reduce the throttle opening.
With the engine running, the PCM continually supplies and monitors a 1 2 volt pull-up to the spark retard circuit.
The ABS/ETC control module requests spark retard by pulling this voltage low. The PCM then responds by
reducing the spark advance of the engine and restricting transmission downshifting.
The ABS/ETC control module constantly sends a Pulse Width Modulated (PWM) signal at 90% with a frequency
of "lOOHz to the throttle relaxer control module on the requested throttle position line (DKR). This signal is to
indicate to the throttle relaxer control module that the traction control system (ETC) is in a state of readiness.
With the engine idling, the ABS/ETC control module constantly sends a Pulse Width Modulated (PMW) signal
with a duty cycle of 90% to the throttle relaxer control module via the requested throttle position line (DKR). The
throttle relaxer control module responds on the actual throttle position line (DKI) with a PWM signal with a duty
cycle of 9%.
When the ABS/ETC control module determines that a reduction in throttle is required, it reduces the PWM signal
on the requested throttle position line (DKR), from 90% (no throttle reduction) to as low as approximately 14%
(maximum throttle reduction). The throttle relaxer control module then drives the throttle relaxer motor,
overriding the accelerator pedal command (drivers foot), pulling the throttle cable back, and thus, closing the
amount of throttle opening.
Page - 98 GEN III V8 ENGINE MANAGEMENT
Содержание GEN III V8
Страница 1: ...HOLDEN GEN III V8 ENGINE MANAGEMENT...
Страница 3: ......
Страница 4: ...GEN III V8 ENGINE MANAGEMENT CONTENTS SUBJECT GEN III V8 ENGINE MANAGEMENT...
Страница 5: ...GEN III V8 ENGINE MANAGEMENT NOTES GEN III V8 ENGINE MANAGEMENT...
Страница 7: ...GEN III V8 ENGINE MANAGEMENT Page 2 GEN III V8 ENGINE MANAGEMENT...
Страница 8: ...GEN III V8 ENGINE MANAGEMENT Page 3...
Страница 14: ...GEN III V8 ENGINE MANAGEMENT GEN III V8 ENGINE MANAGEMENT Page 9...
Страница 16: ...GEN III V8 ENGINE MANAGEMENT GEN III V8 ENGINE MANAGEMENT Page 1 1...
Страница 20: ...GEN III V8 ENGINE MANAGEMENT GEN III V8 ENGINE MANAGEMENT Page 15...
Страница 25: ...GEN III V8 ENGINE MANAGEMENT NOTES Page 20 GEN III V8 ENGINE MANAGEMENT...
Страница 29: ...GEN III V8 ENGINE MANAGEMENT Paqe 24 GEN III V8 ENGINE MANAGEMENT...
Страница 30: ...GEN III V8 ENGINE MANAGEMENT GEN III V8 ENGINE MANAGEMENT Page 25...
Страница 31: ...GEN III V8 ENGINE MANAGEMENT Page 26 GEN III V8 ENGINE MANAGEMENT...
Страница 72: ...GEN III V8 ENGINE MANAGEMENT GEN III V8 ENGINE MANAGEMENT Page 67...
Страница 85: ...GEN III V8 ENGINE MANAGEMENT Page 80 GEN III V8 ENGINE MANAGEMENT...
Страница 90: ...GEN III V8 ENGINE MANAGEMENT GEN III V8 ENGINE MANAGEMENT Page 85...
Страница 94: ...GEN III V8 ENGINE MANAGEMENT GEN III V8 ENGINE MANAGEMENT Page 89...
Страница 104: ...GEN III V8 ENGINE MANAGEMENT GEN III V8 ENGINE MANAGEMENT Page 99...
Страница 113: ...GEN III V8 ENGINE MANAGEMENT NOTES Page 108 GEN III V8 ENGINE MANAGEMENT...