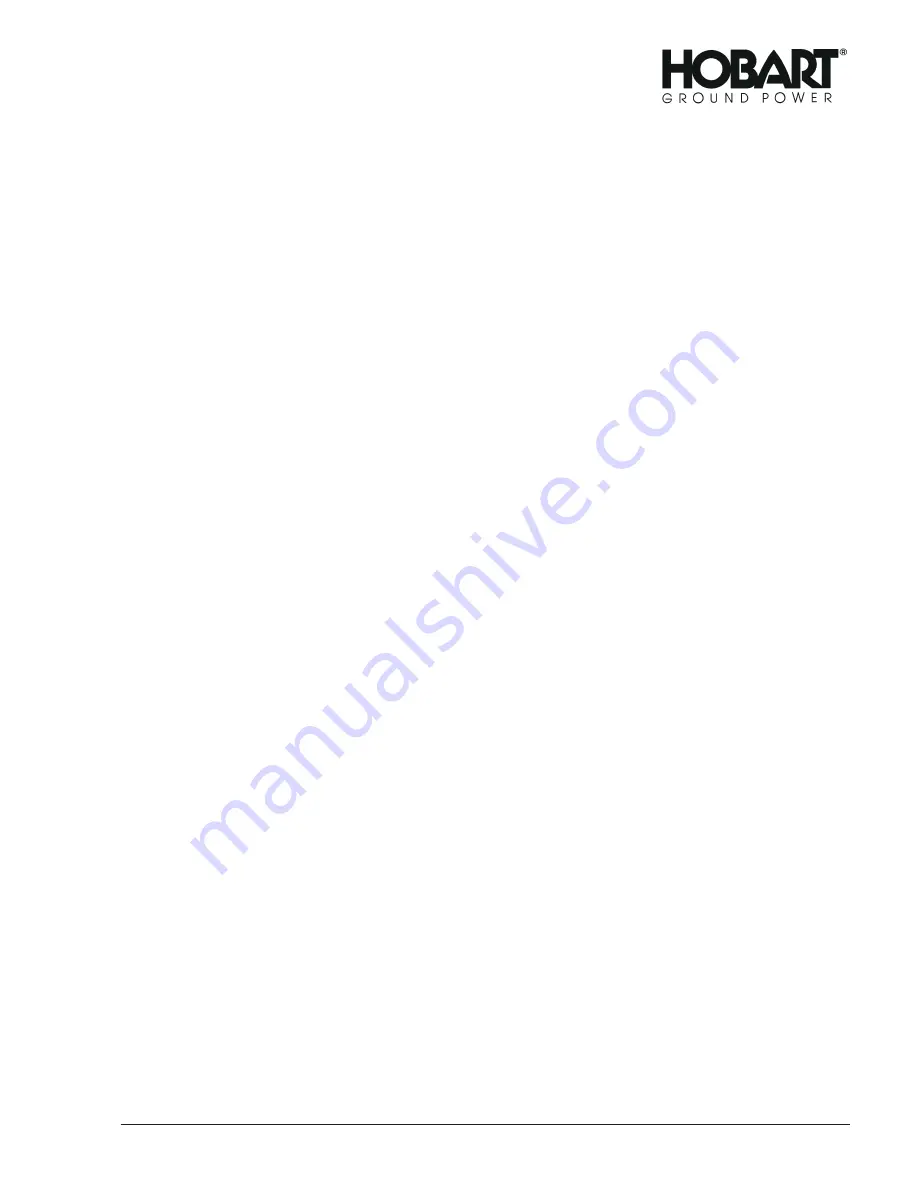
(4)
Cylinder, or its replacement, should be reinstalled by turning cylinder clockwise until the o-ring
contacts the valve. Tighten an additional 1-1/2 turns.
DO NOT OVER TIGHTEN CYLINDER!
b. Check of electrical system.
(1)
Check to see if fuse is blown. Check all wiring for loose connections, shorts, and broken wires.
(2)
Check that the dieselmatic system is wired correctly (See Figure 2).
NOTE:
To check system for proper operation, the Engine Temperature Sensor (ETS) must be below
40º F (4º C) or be bypassed by connecting the valve’s black lead directly to a good ground.
After checking be sure to reconnect the black lead as it was originally connected.
(3)
Test valve by removing fluid cylinder and momentarily engaging cranking motor. Valve plunger
should move up and remain up while cranking motor is engaged. If valve operates, proceed to
step (5).
(4)
If valve plunger did not function, check valve by disconnecting leads from cranking motor and
ground. Momentarily touch leads directly across battery across battery terminals. The valve
plunger should move up and remain up until the leads are disconnected. If the valve does not
activate when connected across the battery it is faulty and should be replaced.
(5)
Check Engine Temperature Sensors (ETS) switch by chilling to sub-freezing temperatures. At
cold temperatures, the ETS Switch should close (i.e. show continuity when checked with a DC
powered test light or ohmmeter.) The closing and opening temperature should be about 40º F
(4º C). If either continuity test fails, the ETS Switch should be replaced.
c. Check for clogging of flow metering orifice fitting.
The Dieselmatic’s fluid flow rate is controlled by serviceable filtered metering orifice inside the fitting
at the bottom of the valve assembly. See Figure 7. The following procedure is recommended when
checking for clogging
(1)
Remove system’s nozzle from engine.
(2)
If starting fluid does not spray from nozzle when the system is activated, disconnect tubing from
valve fitting. If starting fluid sprays from the fitting when the system is activated, check tubing for
kinks, burns, cuts, clogs, or check for a clogged nozzle. When performing these two operations,
be sure to spray fluid into and appropriate container.
(3)
If starting fluid does not spray from valve fitting, it should be removed from valve and cleaned.
Remember, left hand threads.
(4)
The filter may be removed from the fitting, and the o-ring removed from the filter. It can be
washed in clean solvent and blown with compressed air. For best results, replace filter with a
new one KBI Part Number 240005. Reassemble filter with o-ring into fitting.
(5)
It is suggested before cleaned filter assembly is reinserted into valve, that valve be flushed by
activating the system. When performing this operation, be sure to spray fluid into an appropriate
container.
(6)
Reinsert clean filtered fitting assembly into valve. Remember: left hand threads. Reinstall
system’s nozzle into engine. Reconnect tubing to valve fitting and nozzle.
(7)
Check all fitting and tubing connections for leaks.
OM-2084 / Operation and Maintenance Manual
90CU24 / Series 500392 Generator Sets
Chapter 2-1
Page 13
Содержание 90CU24
Страница 193: ......
Страница 194: ......
Страница 195: ......
Страница 196: ......
Страница 197: ......
Страница 198: ......
Страница 199: ......
Страница 200: ......
Страница 201: ......
Страница 202: ......
Страница 203: ......
Страница 204: ......
Страница 205: ......
Страница 206: ......
Страница 207: ......
Страница 208: ......