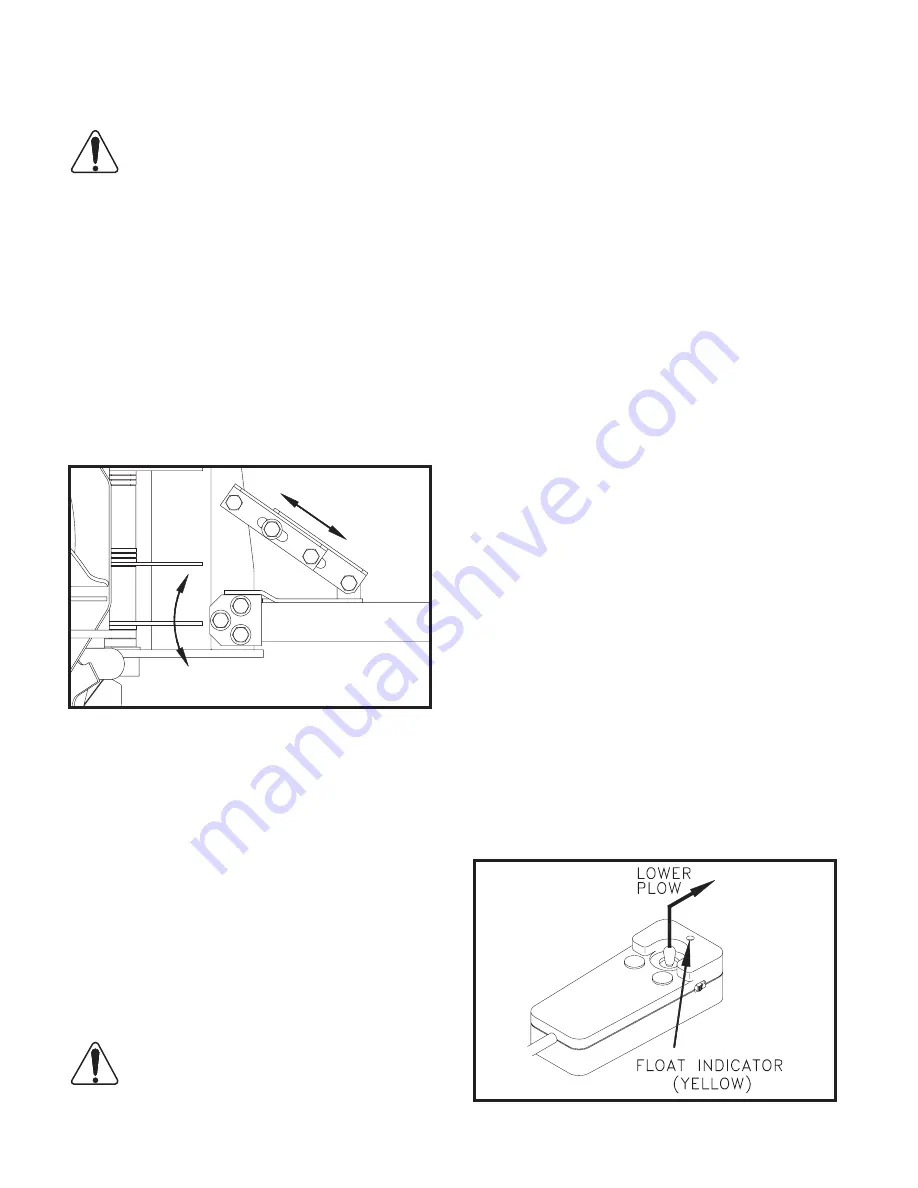
PLOWING SNOW
WARNING: Always wear a seat belt when
plowing snow. Sudden contact with a hid-
den object can result in serious personal
injury.
Inspect areas to be plowed before snowfall for poten-
tial hazards, and mark obstructions with stakes that
will be seen when snow covers the ground. Identify
any emergency equipment and utility outlets that
may need to be cleared in the event of a storm. Pre-
pare a plan beforehand for clearing snow from tight
or enclosed areas and locate sites for stacking snow.
Level the plow in the scoop position by loosening
the hardware through the front of the pushframe and
through the diagonal braces to allow the plow to set-
tle to the ground. Retighten the hardware once the
plow is level.
DWG. NO. 5996
Adjust the skids at the back of the moldboard ac-
cording to the surface to be plowed. The bottom of
the skids should be about 1/2” below the cutting edge
when plowing gravel roads or lots. Skids should be
even with the cutting edge on hard surfaces such as
asphalt or concrete.
Always plow snow as it is accumulating. Wet snow
may weigh about 12 pounds per cubic foot. The weight
of snow being pushed by your plow may increase to
several tons.
Allowing snow depth to grow to unmanageable lev-
els can cause difficult removal problems and can be
costly in terms of wear on equipment.
WARNING: Serious personal injury can re-
sult from plowing at excessive speeds, as
well as costly damage to equipment and
property, if an obstruction is encountered while
plowing. Do not exceed 10 mph while plowing.
Plow snow in the lowest truck gear to transfer maxi-
mum power to the cutting edge. Clear areas in front
of buildings first. Backdrag snow away from buildings
by driving to the building with the plow raised, then
dropping the blade to pull snow away. Push snow to
outer edges of the lot after snow is away from build-
ings.
Begin clearing large lots by putting the plow in the V-
position and creating a single path. Roll snow to the
outer edges of the lot by taking successive passes
with the blade angled, or put the plow in the scoop
position and push snow to the end of the lot. Break
up hard snowbanks with the plow in the V-position.
When plowing very deep snow, it may be necessary
to raise the blade and shear off layers of snow until a
working area is cleared. Work small areas in multiple
passes to push snow to outer edges. Generally, 6
inch snow can be plowed with the entire blade width;
9 inch snow with 3/4 of the blade width; 12 inch snow
with 1/2 of the blade width. Local conditions will de-
termine how much work can be done before stalling
or getting stuck.
PARKING
Lower the plow to the ground when parking your
truck for a long period of time with the plow attached.
Place the on/off switch in the “off’ position to prevent
the plow from drawing power from the truck battery.
The plow’s power unit may continue to draw electri-
cal current from the truck battery if the control switch
is left on; possibly resulting in insufficient charge to
start the truck.
REMOVING THE PLOW
To remove the snowplow from your truck, park on a
solid level surface with the blade straight across the
truck. Lower the plow to the ground and leave the
controller in the “float’ mode.
Lower Plow, Leave Controller In “Float” DWG. NO. 4163
6 Operating Procedures
Содержание 9850
Страница 2: ......
Страница 28: ...26 Wiring Harness ...
Страница 29: ...Wiring Harness 27 DWG NO 5857 ...
Страница 30: ...28 V Plow Power Unit DWG NO 6457A ...
Страница 31: ...Power Unit Hydraulic Circuit Diagram 29 DWG NO 6459 ...