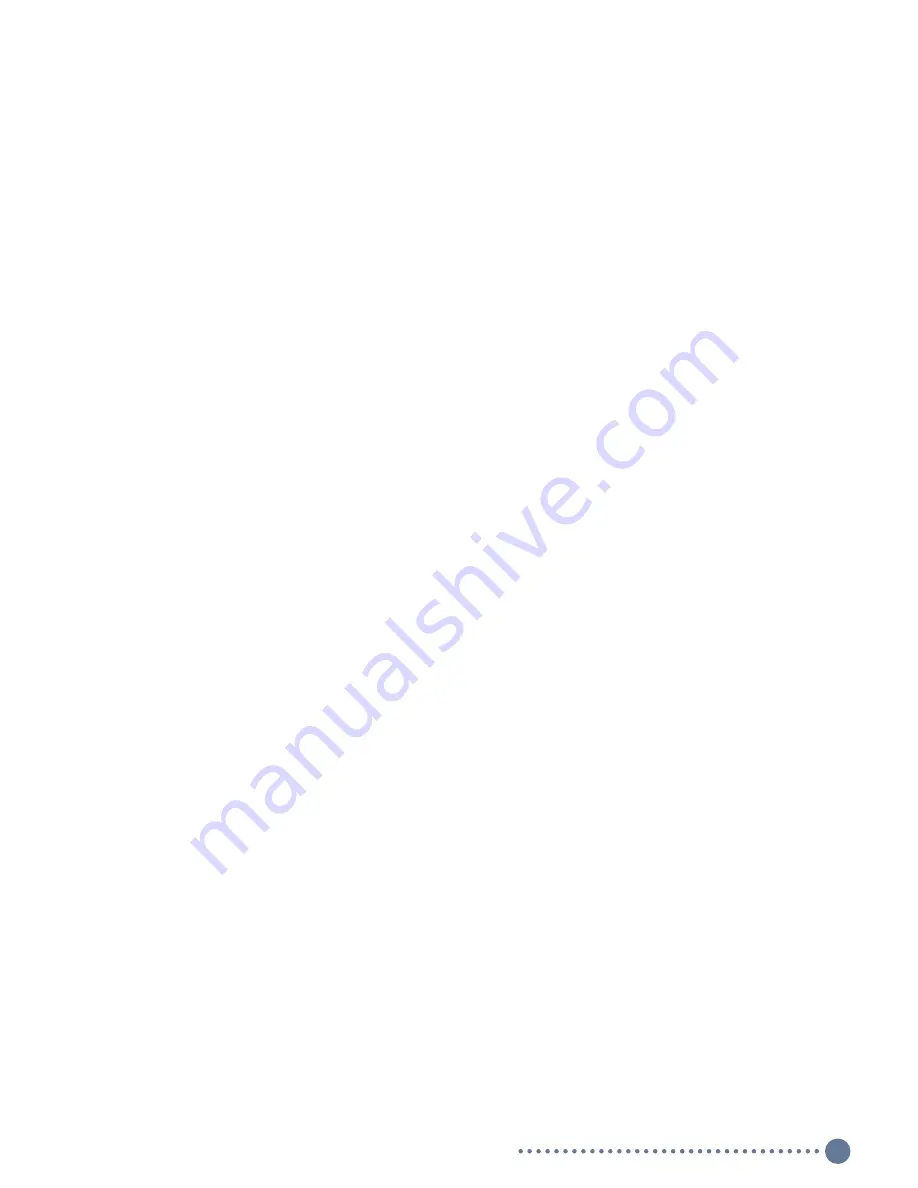
13
© 2022 S. Himmelstein and Company—all rights reserved. www.himmelstein.com
E.3.2 Constant Output Regardless of Shaft
Torque
If the ¶E.3.1 above Cal Checks are performed and found
normal, then the problem is the sensor. Return it for
factory service.
E.3.3 Apparent Zero Drift
• Check the Cabling. See ¶E.2.2.
• Check for Driveline Torque Offsets. Torquemeters
installed in a drive which has hysteresis or friction
torques, may appear to have long term drift when
there is none. For example, when installed between
a pump and a gear drive, the torque reading may not
return to zero after a test because of locked-in fric-
tion torque. The sensor sees and reads that locked-in
torque. Always zero the torquemeter with no torque
on the driveline—in the case cited, with a coupling
disassembled. At the end of the test, the shaft should
be mechanically “shaken” or a coupling broken, to
return to zero torque. Otherwise, the sensor will
read locked-in torque. A rub between any rotating
and stationary part is a common cause of friction.
Verify the shaft couplings and other rotating parts
have adequate clearance.
E.3.4 Signal Instability
• Check the Cabling. See ¶E.2.2 above.
• Check For Driveline Torque Variations. The driveline
may have a low frequency oscillation which the
sensor reads (see Tech Memo 8150). Use the Torque-
meters’ low frequency filter to suppress signals
above 1 Hertz. If the readings become steady, then
you may wish to identify the physical cause of the
shaft torque variation or, remove it with mechanical
filtering techniques. Oscillographic signal analysis
is often helpful under these conditions. Use the 200
Hertz filter for this analysis. If very large, high inertia
machines are used, or large machines are used in a
control loop, torque and speed oscillations can be
present below 1 hertz.
E.3.5 System Will Not Zero
• Check the Cabling. See ¶E.2.2 above.
• Verify the Torque Input is Zero. If the sensor is
installed in a driveline, break or remove one of the
couplings. If the system still can’t be zeroed, then
the problem is either the cable, system grounding
or the Torquemeter. Verify cable integrity, configura-
tion and connections and check the Torquemeter per
¶E.2.1.
• Verify A Good Earth Ground, per ¶B.2.1, is present.
E.4 Speed Pickup Replacement
Speed pickups are threaded into the sensor stator housing
and locked with a jam nut.
E.4.1 Removing A Defective Pickup
• Disconnect the mating cable.
• With shaft motion stopped
, loosen the jam nut.
• Back out the defective speed pickup.
E.4.2 Installing A Replacement Pickup
• With shaft motion stopped
, screw in the new pickup
until it makes contact with the rotor assembly.
• Back off the pickup one quarter of a turn.
• Tighten the jam nut.
• Slowly rotate the shaft to verify no rub occurs. It you
detect a rub, re-adjust the pickup.
• Reconnect the mating cable.
E.4.3 Replacement Part Numbers
• Standard (Code A) Speed Pickup P/N: 900-1001
• Zero Velocity (Code Z) Speed Pickup P/N: 900-1007