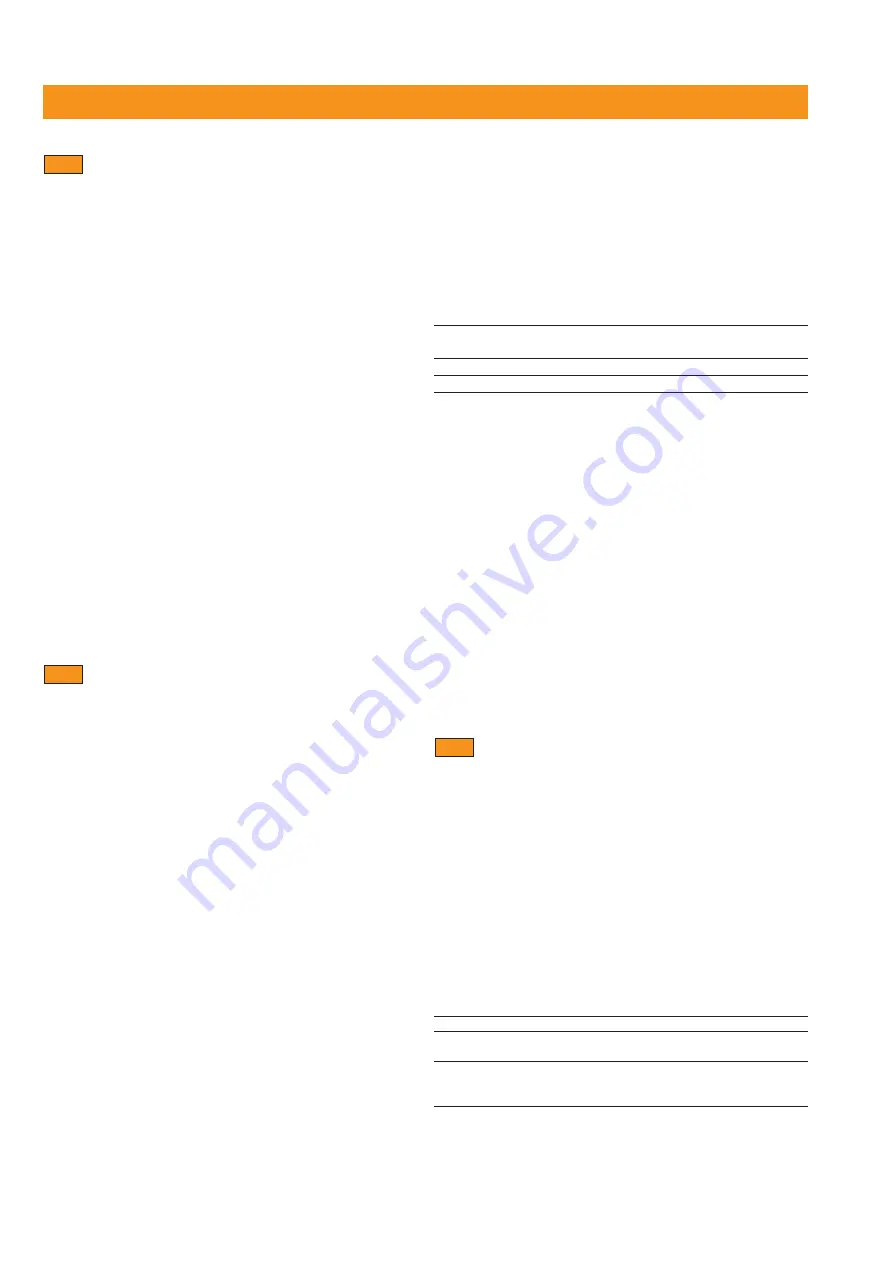
40
7. Operating the equipment
Checks prior to beginning sawing
■
On-site preparatory work should be completed (sup-
ports, cordoning off the danger zone, arrangements for
water collection etc.)
■
The pulley stands and the drive unit should be cor-
rectly secured and the wire rigged on the saw in the cor-
rect direction of travel, the wire guard fitted, wire guid-
ance on the pulleys checked and the guide pulleys tight-
ened. The cooling water supply to the wire should have
been installed.
■
Electric power, compressed air and water should be
connected. The power supply should be equipped with
an earth/ground conductor and ground fault circuit break-
er (PRCD) and should have been checked / tested. Water
and compressed air supplies should be within the per-
mitted pressure range.
■
The control unit should be located outside the dan-
ger zone, hazardous areas in front of and behind the
object to be sawn should have been checked and cor-
doned off and no persons should be present in the haz-
ardous area.
The starting procedure
■
Situation: The main switch is in the ON position. The
“power” indicator light is green. The compressor and
the system are pressurised. The advance lever is in the
“sawing” (advance) position. The remaining switches
are OFF or set at “0”.
■
If necessary, when cutting masonry, the lower advance
compressed air cylinder may be locked in position using
the locking ring provided.
■
Open the 2 water valves on the drive unit for the water
supply to the cutting face.
■
Adjust the advance pressure to approximately 1 bar
at the control unit by means of the control knob (pulled
out), or to the pressure recommended depending on the
wire used for sawing.
■
Switch on the water supply. The white indicator lamp
lights.
■
Switch on the drive (green “DS WS 15 Drive Unit”
push-button).
■
Use the speed regulator to increase speed gradually
and, once the wire is running at a low speed (approxi-
7.1
7.2
mately 3–10 m/s cutting speed), allow the wire to cut
for a few seconds. Check that the wire is running cor-
rectly on all guide pulleys (max. 1 minute).
■
By adjusting the speed regulator, accelerate the motors
until the wire is running at the desired or, respectively,
the optimum cutting speed.
Recommended cutting speeds (approximate)
Cutting Recommended Recommended
method
cutting speed
wire length
Wet
Approx. 20–25 m/s
Keep wire as short as possible
Dry
Approx. 10–20 m/s
Long wire (assists cooling)
■
Set the advance pressure (bar) so that current con-
sumption is 25 – 30 amps. At 400 V it is possible to saw
with only 16 amps, but only with greatly reduced cut-
ting performance.
■
Lock the compressed air control knob (press in).
■
The DS WS 15 now continues sawing automatically.
Monitor the cutting process. Normally, the saw has to
be stopped for a short time soon after beginning cutting.
Stop the saw by switching the drive OFF and then press
in the EMERGENCY STOP button. Check the wire guid-
ance and readjust the water supply.
■
If necessary, release the locking ring on the com-
pressed air cylinder.
The sawing operation
■
Release the EMERGENCY STOP button and start the
drive (the speed and pressure are already set and remain
unchanged). The motors accelerate up to speed. The
wire saw then cuts automatically.
■
Monitor the sawing operation, paying particular atten-
tion to the cooling water supply to the wire. When wet
sawing, the cooling water system must be readjusted as
soon as dust is produced. In most cases, alignment of
the guide pulleys also has to be changed approximate-
ly half-way through the cut.
Wire cooling
Cutting method
Cooling
Comments
Wet
Approx. 5 litres of
NO dust should be produced.
water per min.
Readjust water supply.
Dry
“Air cooling” -
If necessary, use vacuum
long wire
cleaner to remove dust at the
wire exit point.
■
The yellow warning lamp
➜
I lights and the machine
switches off. The drive carriage has reached the end of
its travel, i. e. is at the advance end stop. Press the dri-
7.3
Содержание DS WS15
Страница 1: ...Operating instructions en DS WS15...
Страница 26: ...26...
Страница 38: ...38...
Страница 42: ...42...
Страница 48: ...48 8 Care and maintenance Pneumatic circuit diagram drive unit 8 7 Pneumatic circuit diagram...
Страница 59: ...59...