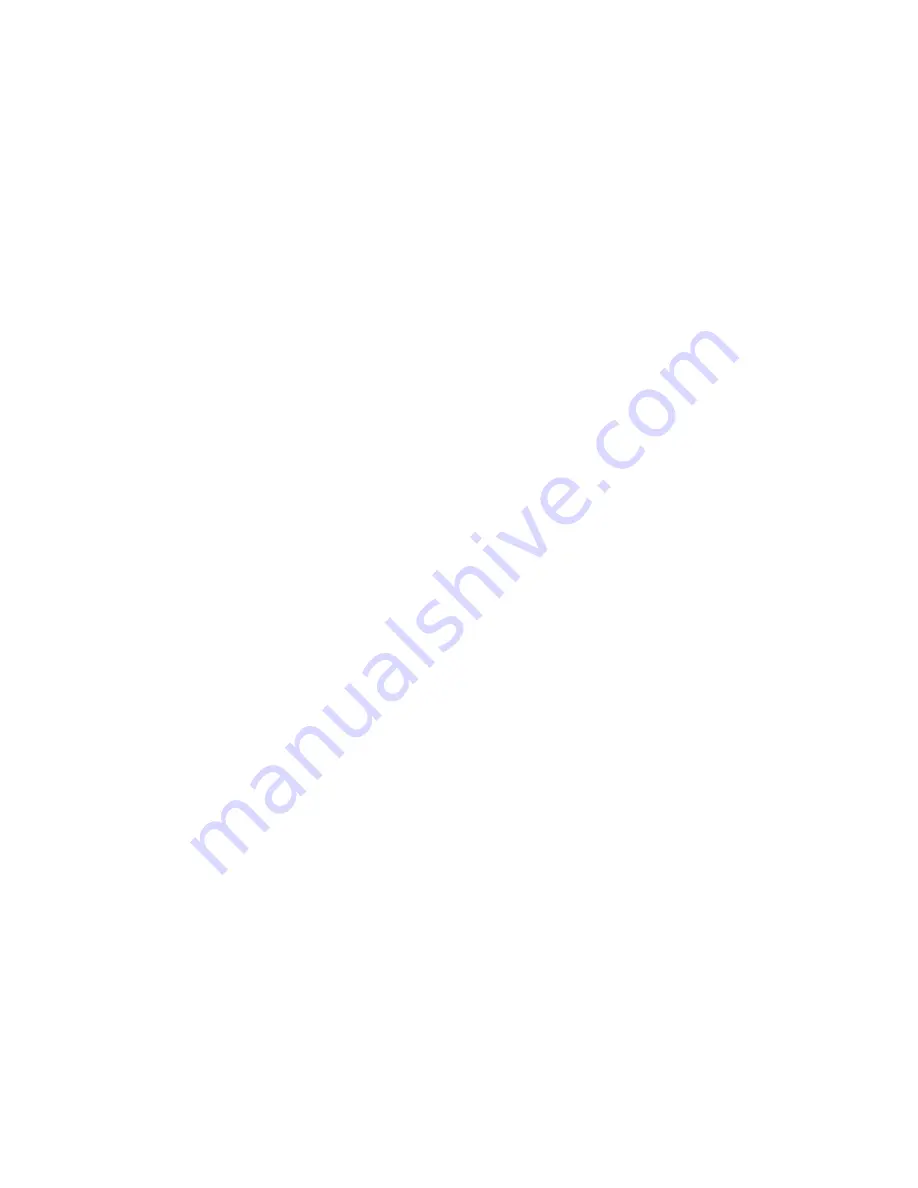
63
T a i l
The setting of the neutral position has already been described on page 55, so that only the maximum deflections have to
be limited. To do this, move the control stick to the maximum level, and adjust the percentages so that the control sleeve
with the brass inner part touches the ball bearing in the right-hand side tail fin when the control stick is fully right.
When the control stick is fully extended to the left side, the brass part of the control sleeve should just touching the
flattened surface of the tail rotor hub
0936
.
Finally, check once again whether all servo deflections, both the swash plate and the tail rotor are moving the right way
around and also control wheather the sensors work in the correct direction.
The swash plate always has to tilt in the opposite direction on all sides, into which you move the helicopter.
The tail rotor control bridge must move towards the gearbox housing when you rotate the fuselage to the left (counter-
clockwise) as viewed from the top of the helicopter (rotor shaft axis).
E S C
I always make the basic programming of the Kontronik ESC (Mode 4) for helicopters. Refer to the Jive guide and follow
the instructions.
For this, the transmitter and the receiving system must be switched on and you must at least be able to switch 0% and
100% on the gas channel to program the ESC for the setting.
Since you have to program different gas curves anyway (in this case, it is actually gas straights) for the individual flight
conditions, you can do this right away.
I recommend to program 3 speeds, the percentage values on the controller being between 40% and 85%.
Depending on the setup and individual preferences used, revs of 1000 rpm to 1850 rpm are recommended. Higher revs
makes no sense with the light TDF, since here no flying advantage is achieved, but only unnecessary energy is wasted.
The system is only loud and restless, and any midi servos that may be used will then reach their performance limits under
unfavorable circumstances.
The tail rotor performance is also high enough at moderate speeds due to the high gear ratio of the belt drive.
Now two parameters should be adjusted. Once, the BEC voltage for the recommended HV servos should be set to 8V,
and you may need to change the rotation direction of the motor when the motor is running in the wrong way.
Place the helicopter without rotor blades on the table so that it is stable and free. Switch off the engine on the transmitter
and connect the flight battery. Switch the throttle to Idle Up1.
When the rotor rotates now, the motor runs right. If the motor rotates, but the rotor is not, the direction of rotation is
wrong.
Attention!
Do not run the engine in the wrong direction. This can damage the freewheel.
If the rotor does not rotate switch off the motor quickly, program the ESC for the right direction of rotation, or replace two
wires of the controller motor connection so that the motor rotates correctly.
Note: When looking at the helicopter from above, the engine rotates to the left (counterclockwise) and the rotor to the
right (clockwise).
R o t o r b l a d e s
The main rotor blades should have a length of approx. 680mm to 710mm with a weight of 175g to 210g.
Also blades wich are swinging to much forward during flight are not favorable, especially if one uses Midi-Servos.
For a 6S or 7S setup I recommend rather the somewhat shorter blades.
The DH tail blades with a length of 107mm have proven to be a good tail rotor blade. More than 115mm makes no sense
because of the high tail gear ratio.
Содержание Three-Dee-Fun TDR-II
Страница 66: ...66 Jan Henseleit ...
Страница 67: ...67 D i m e n s i o n s TDF equipped with 712mm long baldes ...