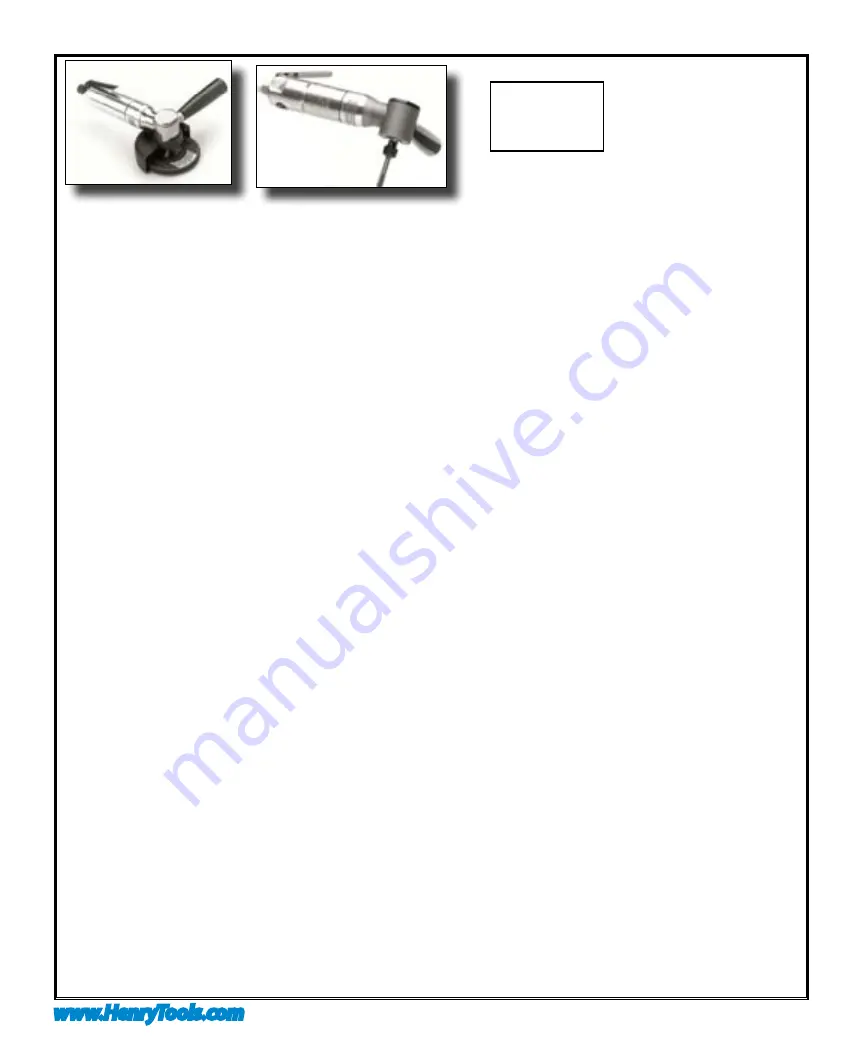
HENR
Y
T
OOLS,
INC.
Ph:
(216) 291-1011 or (800) 826-5257
General Operators Instructions and Service Manual
www.HenryTools.com | Page 79
Revised 03/05/12
For additional product information visit our website.
tightened before use.
•
Always replace a damaged, bent or severely worn wheel guard.
Do not use a wheel guard that has been subjected to wheel failure.
• • Guard opening must face away from the operator. Bottom of
wheel must not project beyond guard.
•
DO NOT MODIFY THE TOOL, SAFETY DEVICES, OR ACCES-
SORIES.
• Use accessories recommended by Henry tools.
• Do not use this tool if the actual free speed exceeds the rated rpm.
Check the free speed of the Grinder
before mounting a wheel, after all tool repairs, before each job and after
every 8 hours of use. Check speed with a calibrated tachometer, without
the abrasive product installed.
• Do not use any wheel or other abrasive accessory whose maximum
operating speed, as defined by its manufacturer, is less than the rated
speed of the Grinder.
• Inspect all grinding wheels for chips or cracks prior to mounting. Do
not use a wheel that is chipped, cracked or otherwise damaged.
• Inspect arbor, threads & clamping devices for damage & wear prior to
mounting wheel or other abrasive accessory.
• Do not use a grinding wheel that has been exposed to freezing tem
-
peratures, extreme temperature changes, high humidity, solvents, water
or other liquids.
• Make certain grinding wheel or other abrasive accessory properly fits
the spindle. The wheel should not fit too snugly or too loosely. Plain
hole wheels should have about .007” (0.17 mm) maximum diametral
clearance. Do not use reducing bushings to adapt a wheel to any arbor
unless such bushings are supplied by and recommended by the wheel
manufacturer.
• Always use the wheel flanges furnished by the manufacturer and ap
-
propriate for the wheel size and type.
Never use a makeshift flange or plain washer. Flanges should be in good
condition and free of nicks, burrs and sharp edges.
• Ensure that the thread type and size of the threaded abrasive product
exactly matches the thread type and size of the spindle.
• Prevent the spindle end from touching the bottom of the hole of cups,
cones or plugs with threaded holes, intended to be mounted on machine
spindles, by comparing dimensions and other relevant data for them.
• Do not use an unguarded grinder unless used for internal work and
only operated when the work offers protection.
Original Style
Tools Pre-Year
2009
DISASSEMBLY
PLEASE NOTE
: The brass spacers that were installed by the factory are
necessary for this tool to operate efficiently. When disassembling this
tool examine how spacers are arranged. They must be installed exactly
the same way. Failure to do this will cause improper gear spacing, which
causes pre-mature tool failure.
1. Disconnect air & remove all wheels and accessories.
2. Remove dead handle (404-40). Secure anglehead vertically in vise
on dead handle boss. Never squeeze anglehead(404-1) in vise. This
will distort bearings and ruin gear alignment.
3. Unscrew backhead (400-G-4). Unscrew case (400-G-1).
4.
Remove deflector (400-G-17).
5. Pull motor from right angle head. Be careful to note location of
shims.
6. Remove snap ring (404-39),wafer(404-38),O-ring(594016), and
snap ring (592016).(Some of these parts may or maynot be present).
7. Install brass or aluminum jaws in vise. Grasp the O.D. of
cylinder(400-2-G) and end plate(404-19). Using a 3/16” punch, tap
spindle out rear bearing (404-9).
8. Remove cylinder, blades(400-6). 8. With rotor (400-5) still in
spindle (404-14), grasp the rotor in vise snugly and remove pinion
gear(405-10).
9. Remove rotor(400-5) Remove key and front thrust plate(400-7).
Press bearing (400-G-11) off of spindle.
10. Secure angle head in vise and unscrew cap (404-2).
11. Remove from vise and tap on spindle with a plastic hammer. The
spindle assembly and spring washers (404-6) will slide out.
12.
Clamp flats of spindle(405-17) in vise.
MODELS
45 RA
45 RAC
45 RAZ
45 RAS
13. Using a 9/64” T-Handle hex wrench unscrew (591028) screw. Using a
plastic hammer tap on O.D. of bearing cap, until it is free of bearing(404-3).
N
ote
positioN
of
shims
.
14. Press bearing (404-3) off spindle. Support bearing (404-7) and
press spindle through with 1/4” punch. This will remove spacer (405-15),
gear(405-10) and bearing. Remove key (404-4).
ASSEMBLY
1. Support front bearing(400-G-11) on drill block. Press spindle (404-14)
through bearing until it bottoms on shoulder.
2. Slide front thrust(400-7)over the spindle and onto front bearing.
3. Place key(400-10) into keyway in spindle. Slide rotor down over shaft.
4. Grasp rotor in vise snugly and replace pinion gear(405-10) and wrench
firmly.
5.
Support bearing and pinion gear in downward position. Place five
blades(400-6) in slots. Slip cylinder(400-2-G) over rotor. Install rear
thrust(404-19) locating cylinder pin in small hole of rear thrust plate (404-
19).
6. Place bearing (404-9) in rear thrust and tap into place with a suitable
bearing driver. Using snap ring pliers, place snap ring(404-39) in end plate
groove.
7. Support bearing(404-7) on inner race. Press spindle (405-17) through
bearing until it bottoms on shoulder. Install key (404-4) and line up with
keyway of ring gear(405-10). Support gear on inner diameter and press
spindle through. Slide spacer(405-15) on spindle.
8. Support threaded end of spindle and press on bearing(404-3). Tighten
screw (591028) into end of spindle. Press spindle assembly into cap(404-2).
Grease gear.
9. Install spring washers(404-6) (
rouNded
side
dowN
) into angle head(404-
1).
10. Install spindle assembly into angle head housing, secure in vise and
tighten cap (404-2).
11. Re-Locate angle head in vise-so that the motor can be installed verti-
cally.
12. Replace shim(404-20) exactly as it was originally installed.
13. Jiggle greased pinion assembly into angle head while turning spindle
(405-17)-so that gears mesh. Tap lightly on rear of motor to insure that is
fully seated.
14.
Install muffler (402-134) inside exhaust deflector (400-G-17-S). Place
O-ring(400-51) on motor case(400-G-1), then slide case (400-G-1) over
motor assembly and screw onto anglehead(404-1). The deflector (400-G-
17) should be snug, but can be turned. Place a few drops of oil into motor
inlet. Replace backhead assembly (400-G-4).
15. (
o
ptioNal
s
tep
): To check throttle valve, unscrew plug(869311) and lift
out spring and valve. Replace O-ring if worn.
16. Replace guard on tool.
17. CHECK RPM WITH TACHOMETER.TOOL MUST RUN AT OR BELOW
SPEED THAT IS STAMPED ON TOOL.