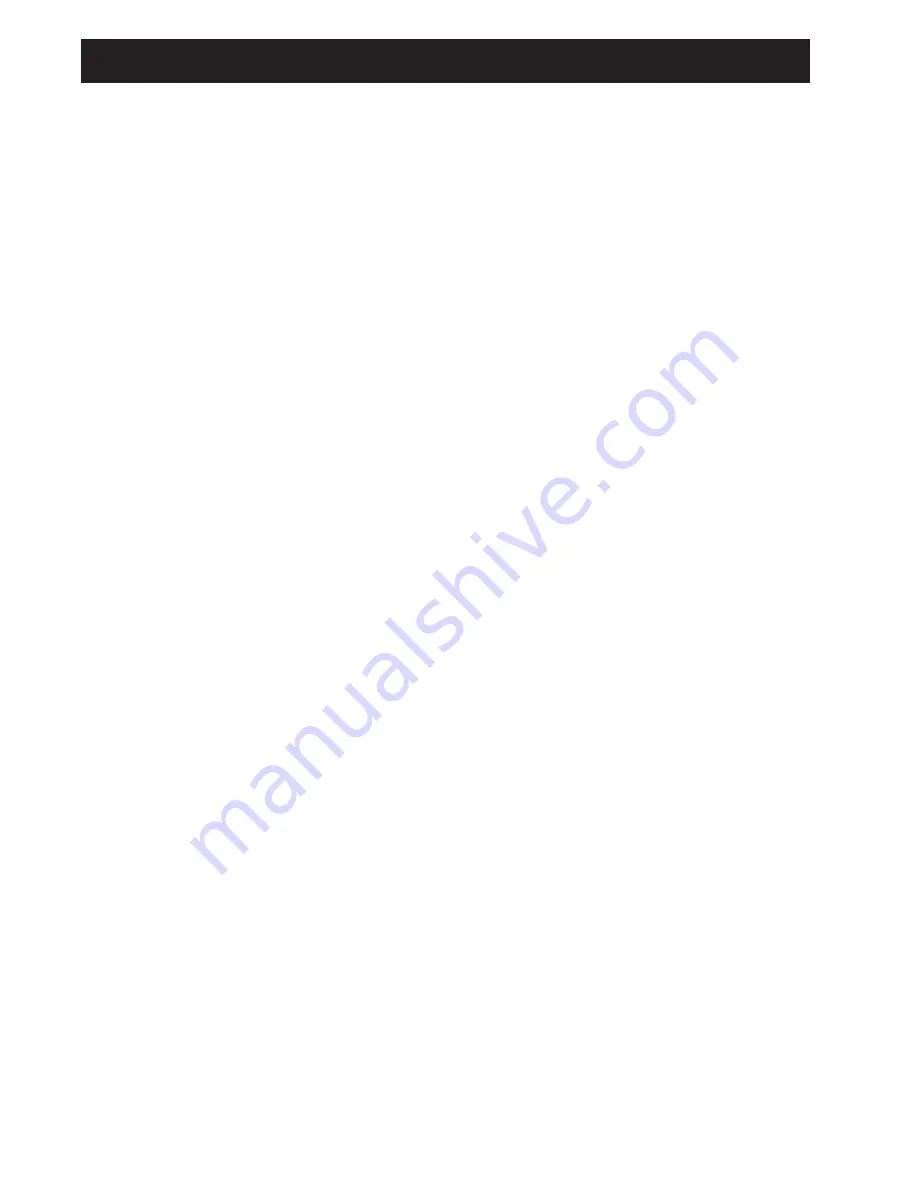
48
RECORD
OUTDOOR TEMPERATURE
______°F.
SYSTEM VOLTAGE
______Volts
______PH
______Hz
Cooler compressor amps
______L1
______L2
______L3
Freezer compressor amps
______L1
______L2
______L3
Cooler discharge pressure
______PSIG
Freezer discharge pressure
______PSIG
Cooler suction pressure
______PSIG
Freezer suction pressure
______PSIG
Cooler suction temperature
______°F.
Freezer suction temperature
______°F.
Cooler refrigerant charge
______lbs.
Freezer refrigerant charge
______lbs.
Cooler compressor superheat
______°F.
Freezer compressor superheat
______°F.
Cooler evaporator superheat
______°F.
Freezer evaporator superheat
______°F.
Cooler discharge temperature
______°F.
Freezer discharge temperature
______°F.
Startup Checklist