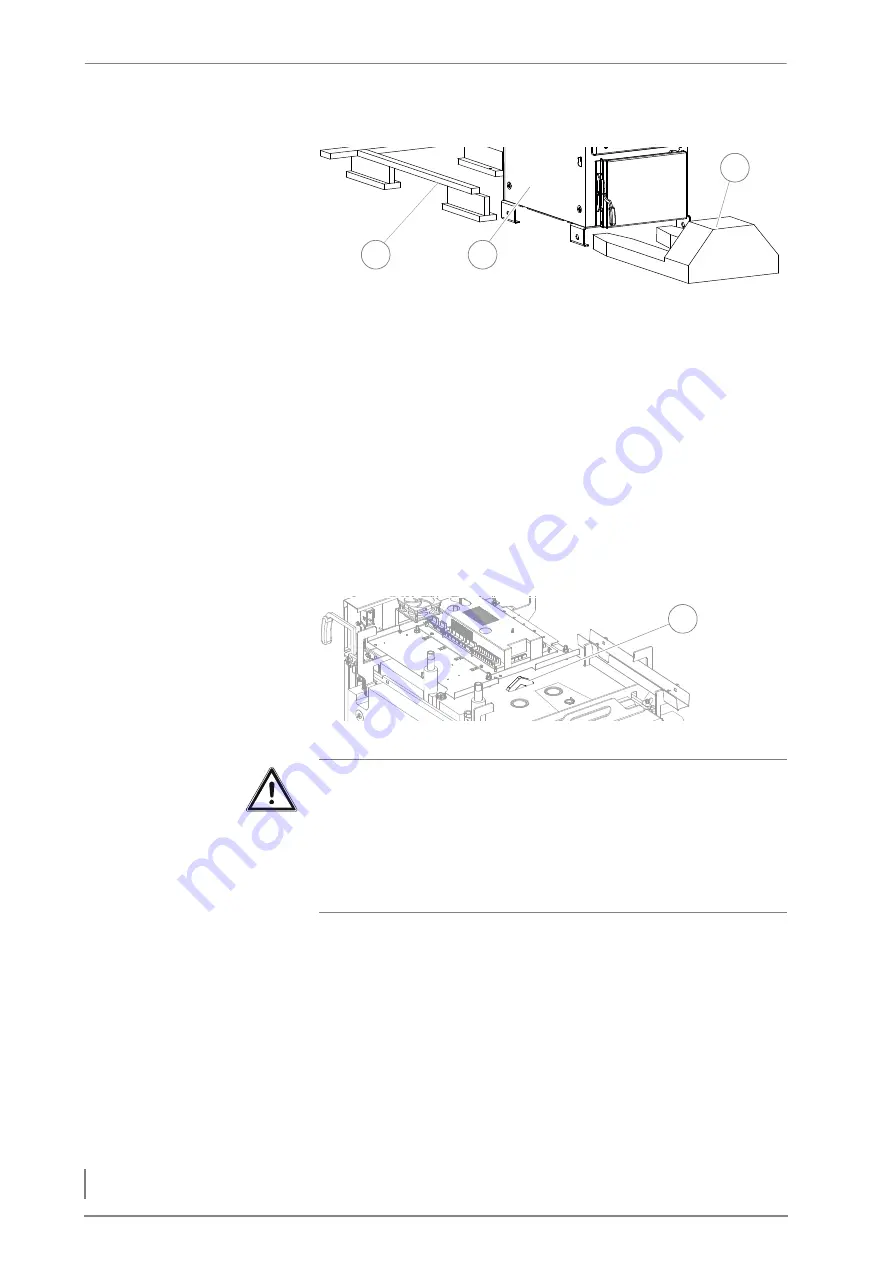
4 Planning and installation – Installing the heating system
32
7.
Pull the pallet (1) out from under the boiler (2).
8.
Transport the boiler (2) to the desired installation site.
9.
Set down the boiler (2) at the planned location while observing
the minimum clearances.
✎
See section “4.2 Structural requirements”, under “Required room
sizes and minimum clearances”.
10.
Remove the lifting truck (3).
11.
Align the boiler with plastic plates or flat steel strips (not included
in the scope of delivery) so that it is horizontal.
✓
The HDG F20-50 boiler has been placed in position.
T
RANSPORT
WITH
A
CRANE
1.
Attach suitable lifting equipment to the crane eyelet (1) provided
for this purpose.
✓
The boiler can now be moved with a crane.
2.
Remove the transport pallet.
✎
See section "Transporting with a pallet truck".
3.
Transport the boiler to the desired installation site.
4.
Place the boiler at the planned location while observing the
minimum clearances.
Figure 4/6 - Transporting with a pallet truck
2
3
1
Figure 4/7 - Crane eyelet
1
Warning!
Damage caused by improper assembly
The crane eyelet is located very close to the central module. It can
be damaged if the lifting equipment is not attached carefully.
When attaching the lifting equipment and during transport, ensure
that the central module is not damaged.
Содержание F20
Страница 1: ...hdg bavaria com HDG F20 25 30 HDG F40 50 Operating manual ...
Страница 2: ......
Страница 87: ......