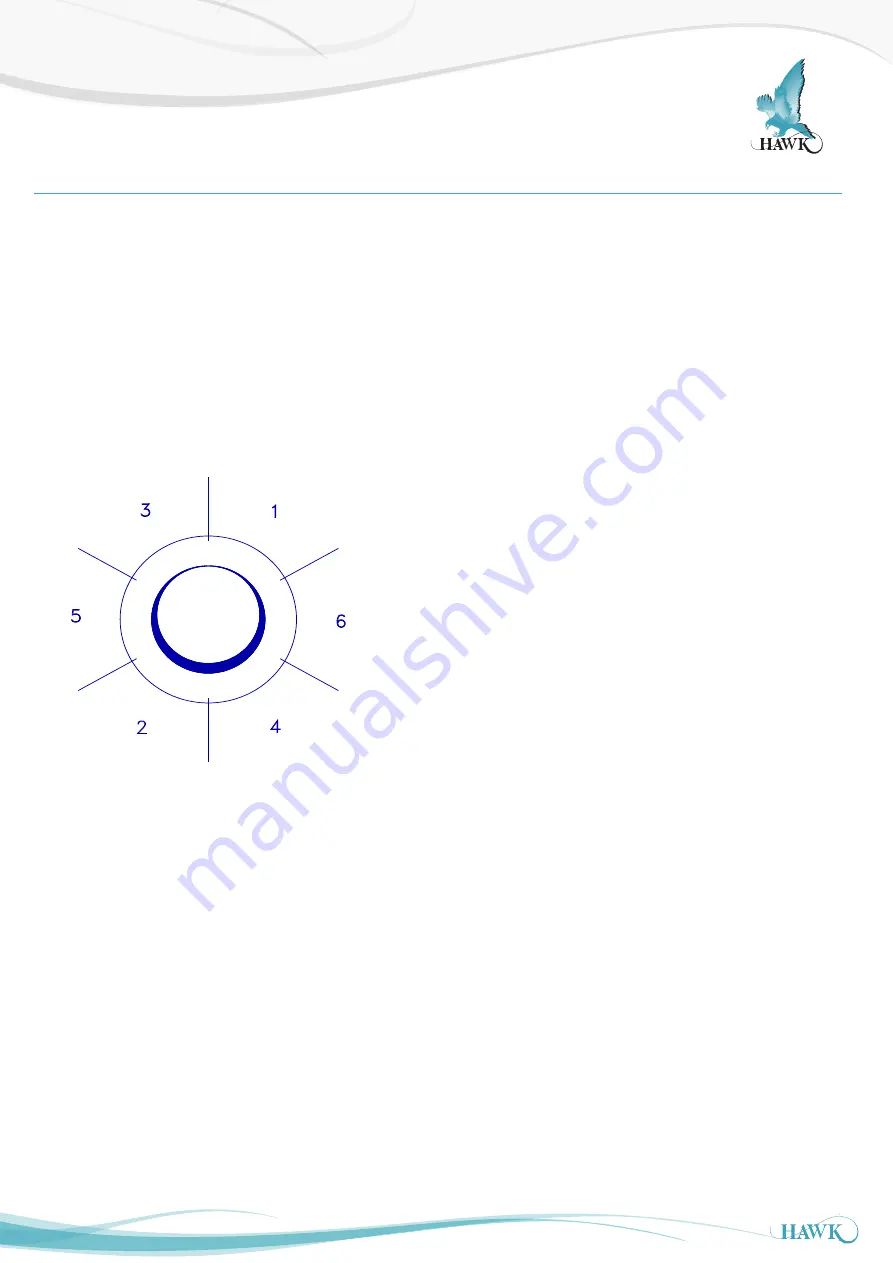
6
Overview
3. Installation transmitter
The diaphragm of the transmitter is protected with a special protection cap. Protect the diaphragm until installation takes place.
* DO NOT DAMAGE THE DIAPHRAGM. *.
3.1 Installing Weld-On Nipple
A skilled machinist or certified welder should perform installation of the weld-on nipple.
Weld Argon, MIG or TIG with the smallest welding pin.
1. Cut a hole in the process vessel/pipe to accept the weld-on nipple. The hole should produce a tight fit when coupled with the
weld-on nipple.
2. Prepare the vessel hole by beveling the edge to accept filler material.
3. Remove the weld-on nipple from the transmitter.
4. Remove the PTFE packing of the SERIES 2000-SAN.
5. Position the weld-on nipple in the vessel hole and tack six places. The weld sequence is shown in the figure above.
6. Weld the weld-on nipple in place using 0,03 to 0,045 in. (0,762 to 1,143 mm) stainless rod as filler material in the beveled area.
Adjust amperage for penetration.
7. Remove mandrel after the welding operation.
WARNING
Improper installation may result in distortion of the weld-on nipple.
Excessive heat will distort the weld-on nipple. Weld in sections as shown
in the figure left. Allow adequate cooling between passes. To reduce the
chances of distortion to the weld-on nipple, use a mandrell.
(SERIES 2000-SAN Part.nr. 1019)
(SERIES 2000
Part.nr. 1016)
The position of the electronic housing (SERIES 2000) is fixed by the
welding position of the weld-on nipple. Before welding, locate weld-on
nipple so that the cable entry and the venting are in the right direction.
3.2 Installing Transmitter Series 2000-SAN
1. Improper installation at the packing can cause a process leak.
2. Make sure to correctly locate the packing within the weld-on nipple.
3. Position the transmitter into the weld-on nipple and begin engaging threads. The transmitter can be rotated prior to seating
enabling the user to optimize access to calibration adjustments, cable entry, and local indicator.
4. Once Lock ring (9) has been hand tightened, it must be tightened with an additional turn with adjustable pliers (± 1/8”).
3.3 Installing Transmitter Series 2000
1. After welding, clean up edges, take care of the inside nipple wall.
2. Make sure the O-rings (10) and (11) are properly located. Improper installation at the O-ring can cause a process leak.
3. Apply silicone grease to the O-ring(10), diaphragm ring and the hole inside wall of the weld-on nipple, this prevents galvanic cell
corrosion between transmitter and nipple inside.
4. Install the transmitter and fix it with the SS M8 bolt.
Series 2000 HART