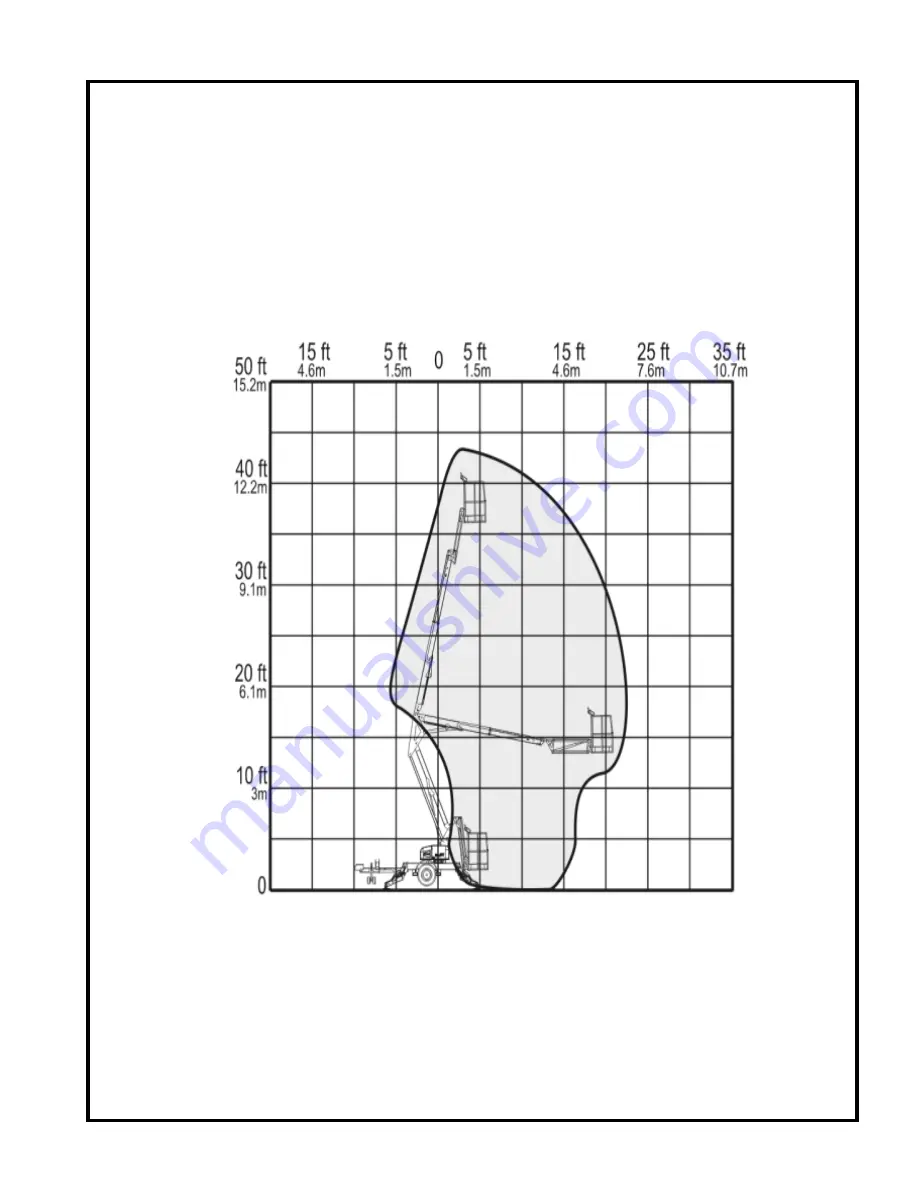
HAULOTTE GROUP
2 SPECIFICATIONS
15
2 SPECIFICATIONS
The following information is based on ideal working conditions. Machine performance may vary
based on work environment and on machine options.
Only one boom function is permitted at a time, this function is only operable as long as the boom is
within the safe operating zone. Once a boom motion exceeds its safe operating limit, that function
ceases, another boom function within the safe operating zone must be selected.
Refer to Figure 2-1.
RANGE OF MOTION
Figure 2-1. Range of Motion
Содержание 3522A
Страница 1: ...OPERATOR S MAINTENANCE MANUAL B33 01 0093 Rev 4 May 2013...
Страница 76: ...HAULOTTE GROUP 6 DECAL REPLACEMENT 76 DECAL KIT ANSI...
Страница 78: ...HAULOTTE GROUP 6 DECAL REPLACEMENT 78 IDENTIFICATION PLATES OPTIONAL EQUIPMENT ANSI...
Страница 81: ...HAULOTTE GROUP 6 DECAL REPLACEMENT 81 DECALS ANSI CONTINUED B06 00 0533 B06 00 0505 B06 00 0534 B06 00 0404...
Страница 84: ...HAULOTTE GROUP 6 DECAL REPLACEMENT 84 DECAL KIT CE...
Страница 86: ...HAULOTTE GROUP 6 DECAL REPLACEMENT 86 IDENTIFICATION PLATES OPTIONAL EQUIPMENT CE...
Страница 88: ...HAULOTTE GROUP 6 DECAL REPLACEMENT 88 DECAL KIT AU...
Страница 90: ...HAULOTTE GROUP 6 DECAL REPLACEMENT 90 IDENTIFICATION PLATES OPTIONAL EQUIPMENT AU...
Страница 92: ...HAULOTTE GROUP 6 DECAL REPLACEMENT 92...
Страница 102: ...HAULOTTE GROUP 8 MATERIAL SAFETY 102 MATERIAL SAFETY DATA SHEET LEAD ACID BATTERIES WET FILLED WITH ACID UN 2794 CONT...
Страница 103: ...HAULOTTE GROUP 8 MATERIAL SAFETY 103 MATERIAL SAFETY DATA SHEET LEAD ACID BATTERIES WET FILLED WITH ACID UN 2794 CONT...
Страница 104: ...HAULOTTE GROUP 8 MATERIAL SAFETY 104 MATERIAL SAFETY DATA SHEET LEAD ACID BATTERIES WET FILLED WITH ACID UN 2794 CONT...
Страница 105: ...HAULOTTE GROUP 8 MATERIAL SAFETY 105 MATERIAL SAFETY DATA SHEET LEAD ACID BATTERIES WET FILLED WITH ACID UN 2794 CONT...
Страница 106: ...HAULOTTE GROUP 8 MATERIAL SAFETY 106 MATERIAL SAFETY DATA SHEET POWERFLOW AW HVI HYDRAULIC OIL...
Страница 107: ...HAULOTTE GROUP 8 MATERIAL SAFETY 107 MATERIAL SAFETY DATA SHEET POWERFLOW AW HVI HYDRAULIC OIL CONTINUED...
Страница 108: ...HAULOTTE GROUP 8 MATERIAL SAFETY 108 MATERIAL SAFETY DATA SHEET POWERFLOW AW HVI HYDRAULIC OIL CONTINUED...
Страница 109: ...HAULOTTE GROUP 8 MATERIAL SAFETY 109 MATERIAL SAFETY DATA SHEET POWERFLOW AW HVI HYDRAULIC OIL CONTINUED...
Страница 110: ...HAULOTTE GROUP 8 MATERIAL SAFETY 110 MATERIAL SAFETY DATA SHEET POWERFLOW AW HVI HYDRAULIC OIL CONTINUED...
Страница 111: ...HAULOTTE GROUP 8 MATERIAL SAFETY 111 MATERIAL SAFETY DATA SHEET POWERFLOW AW HVI HYDRAULIC OIL CONTINUED...
Страница 112: ...HAULOTTE GROUP 8 MATERIAL SAFETY 112 MATERIAL SAFETY DATA SHEET POWERFLOW AW HVI HYDRAULIC OIL CONTINUED...
Страница 137: ...HAULOTTE GROUP 9 AXLE AND RELATED COMPONENTS 137 Figure 9 1 Standard Brake Adjustment Procedure...