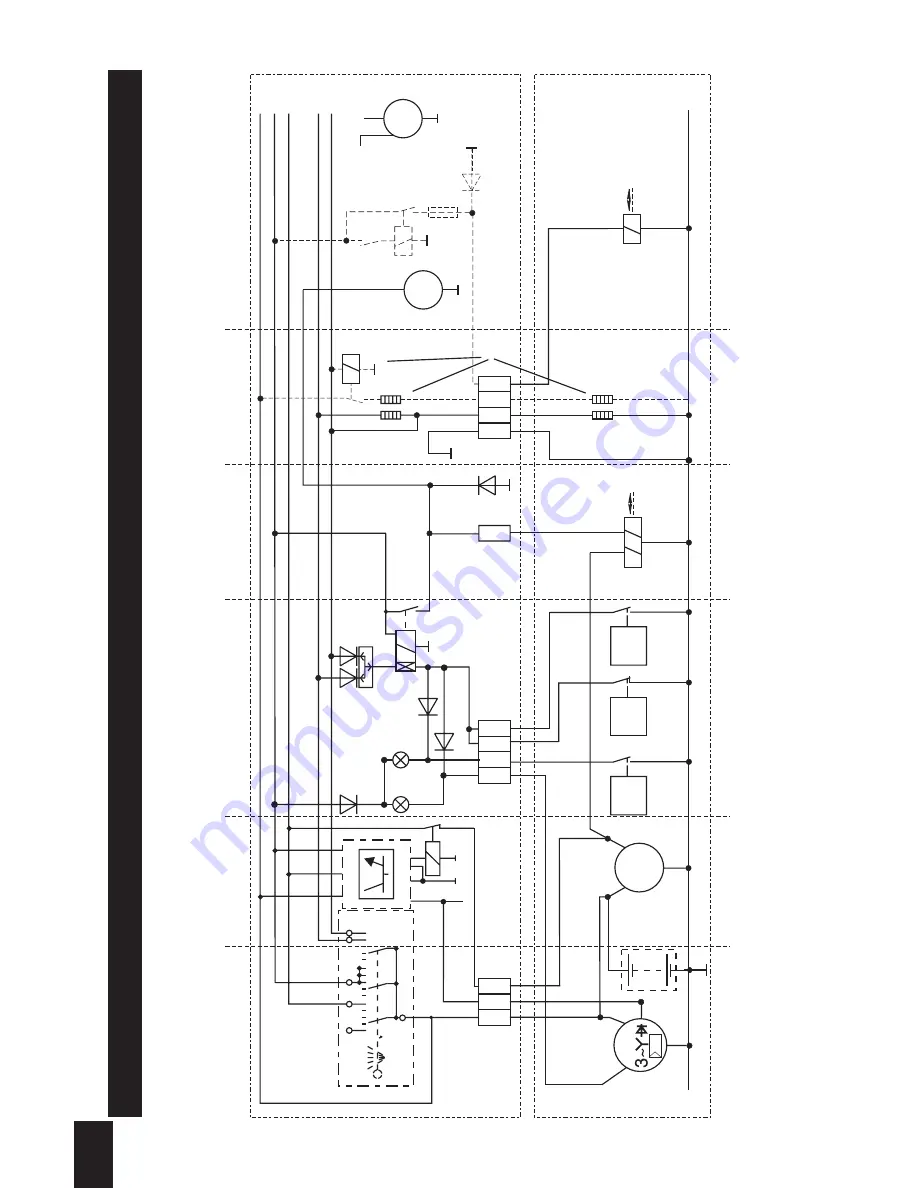
4
L / M . . / 07.96
P 0 1 2 3
58 50a 15 19 17
P
, 0, 1
30
86
30
87
85
86
30
87
85
30
50
M
G
U
D+
B+
P
u
P
t°
h
P1
n
P2
15
W - 2
0
7
Y1
0
Y3
3
AW
7
HW
S1
G1
G2
M1
31
30
15
50
19
17
22
1
3
W - 6
W
7
4
17
5
2
X1
X2
8
6
14
0
X1
X1
X1
S8
S7
S6
H1 H4
V1
V1
V1
V1
K4
V1
R1
R1
H6
V2
H6
K2
S5
K3
F1
8A
V2
U30 U50 U15
Win GND A
u
s
86 30
85 87a
K1
A4
31
87
15
50
SE
12
3
4
56
Engine
4 L / M 31,40,41 only
Instr
ument bo
x
P
o
w
e
r supply
Charging de
vice
Star
ting de
vice
Monitor
ing + displa
y
Engine shut-do
w
n
P
re-heating
Optiones
(Hour-r
un meter
, speed adjustment)
Cir
cuit dia
gram 12
V - system with automat.
shut do
wn and star
ter pr
otection module
Содержание 2-4L30
Страница 2: ......
Страница 6: ......
Страница 7: ...1 L M 10 98 1 General...
Страница 22: ......
Страница 23: ...2 L M 09 96 2 Additional equipment...
Страница 47: ...3 Basic engine 3 L M 09 96...
Страница 134: ......
Страница 135: ...4 L M 07 96 4 Tables...