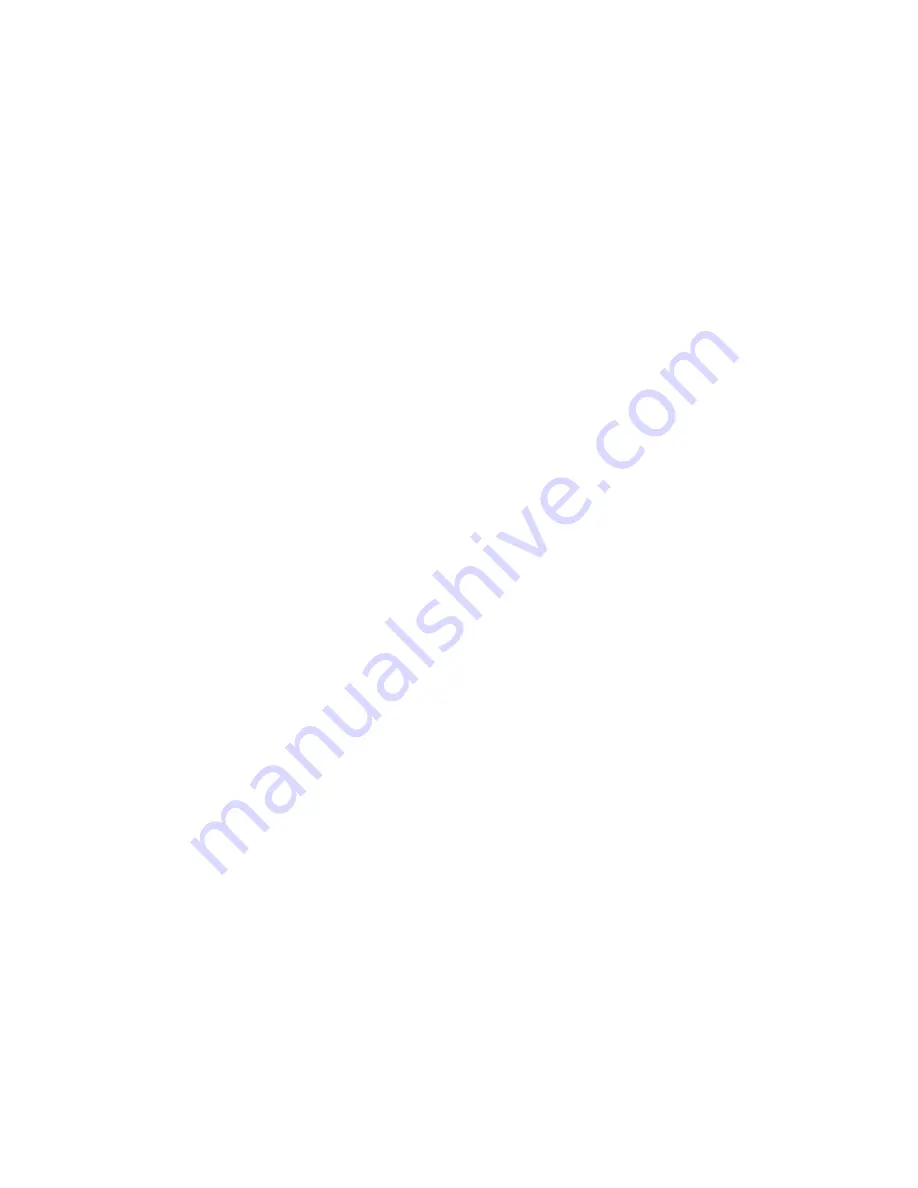
SECTION G
PDM AMPLIFIER/PULL-UP (A6-A9)
G.1.
Principles of Operation
G.1.1.
PDM Amplifier
The purpose of the PDM amplifier is to
switch the PDM filter inputs to ground at a
60 kHz rate, determined by the pulses from
the PDM generator.
The signal from the PDM generator is
about 13 volts peak-to-peak, and comes in
on J2-3 and J2-1 of the PDM Amplifiers.
Plug P4 is positioned in 1 to 3 for a 5kW
transmitter, and is positioned in 1 to 2 for a
1kW or 2kW transmitter. In the 1 to 3 posi-
tion, it allows one PDM signal to drive all
four transistors on the PDM amplifier. In the
other case, this allows two phases of the
PDM signal to drive two separate pairs of
PDM amplifier transistors.
The PDM input signal passes through iso-
lation resistors R11 and R31 and into cur-
rent amplifiers U11 and U31. These IC’s act
as voltage followers and pass the PDM sig-
nal to the class B drivers (transistors Q13,
Q14, Q15, Q16, Q35, Q36 and Q33 and
Q34). Only one half of the PDM amplifier
drive circuitry will be discussed; the other
half has exactly the same operation.
The push-pull driver transistors Q13 and
Q14 are voltage followers. The outputs
from U11-3 and -5 are identical. Therefore
when the voltage is high, coming out of
U11, Q13 will be on; when the signal com-
ing out of U11 is low, Q14 will be on.
Capacitor C14 in the base of transistor
Q14 quickly discharges the base of Q14
when turning it off. CR14 clamps the gate
voltage of transistor Q19 to approximately
15 volts and acts as a transient suppressor
to absorb any voltage transients on the gate
of transistor Q19.
Diodes CR12 and CR13 have two pur-
poses. Their first purpose is to provide two
diode drops for any offset voltages from
transistor Q14 and U11 when the PDM
signal is low. Their other purpose is to stand
off the high voltage on the gate of Q19 if
transistor Q19 should fail drain to gate.
Capacitors C17, C18 and C19 also have
two purposes. The first is to pass the 60 kHz
signal to turn off Q19; the second is again
to prevent the chances of failing driver cir-
cuitry beyond CR14 if Q19 should fail,
drain to gate. These capacitors then will
charge up to the high voltage power supply
and CR14 will clamp the voltage on the
other side of the capacitors to approxi-
mately 15 volts. R21 acts as a pull down and
load resistor to help prevent any accidental
turn on of Q19.
Transistors Q19 and Q20 are in parallel
and will share the current from the PDM
filter. When the incoming PDM signal is
high, Q19 and Q20 will be on and will short
the PDM filter to ground. When the incom-
ing PDM signal is low, transistors Q19 and
Q20 will be off and the PDM filter will be
un-terminated and its voltage will rise to the
power supply voltage.
C23, C46, C47 and R23 form a snubber
circuit. This circuit reduces the high voltage
overshoot transient when Q19 turns off.
R25, R26, CR19, R27 and C25 form a
PDM status indicator for the Controller and
the front display panel. This detector is what
provides the sample for the PDM Fault
LED’s.
PDM Pull-Up board fuse A6A1F1/F2 will
open in the event of damper diode or PDM
Amplifier MOSFET short circuit failures. If
a PDM phase line is short circuited on the
output side of A6A1F1, there will be 0
voltage sent to the Controller through this
circuit on J1 pin 7. If PDM Amplifier MOS-
FET (Q19 or Q20) or the associated damper
diode is short circuited, a higher voltage
than normal will be sent to the Controller
on J1 pin 7 because A6A1F1/F2 will have
opened. The PDM filter makes connection
to the PDM amplifiers at jacks J5 and J6.
Damper diode CR1 prevents the voltage
at the input side of the PDM filter from
rising above the high voltage power supply
when the PDM amplifier transistors turn
off. The damper diodes make connection to
the power supply through the PDM pull up
board.
G.1.2.
PDM Pull-Up Board
The purpose of the PDM pull-up board is
to provide the connection for the damper
diode circuit and to reduce distortion at low
power levels. Point E2 is connected to the
high voltage power supply. It is also by-
passed with a large electrolytic capacitor.
C1 and C3 also provide additional switch-
ing rate bypassing for the damper diode on
the PDM amplifier.
As a function separate from PDM pull-up
action, fuse A6A1F1/F2 provides over cur-
rent protection if either the associated PDM
Amplifier MOSFET’s (Q19 or Q20) or
damper diode on the PDM Amplifier mod-
ule short.
The PDM pull-up signal comes in on J1
from a heavily averaged current source
which is formed by A19L1, a two henry
choke and A19R20, a 500 ohm resistor. This
circuit compensates for stray capacitance in
the PDM Amplifier and reduces low power
distortion.
G.2.
Maintenance
G.2.1.
PDM Amplifiers
NOTE
If a PDM AMPLIFIER fails shorted
when operating at a reduced power,
there will be an increase in the carrier
power. The fuses will not necessarily
blow because of the relatively low total
transmitter power. In this case, it may be
impossible to lower the output power to
an acceptable level, and the transmitter
will have distorted audio. If this condi-
tion occurs, the transmitter should be re-
moved from service and maintenance
personnel alerted to the problem as
quickly as possible. The failed amplifier
may be isolated by removing the correct
fuses from the PDM Pull Up board.
G.2.2.
Gate Drive Checks
NOTE
Ensure that the REMOTE/LOCAL switch
located on the Controller board is in the
LOCAL position before performing the
checks outlined below. When the switch
is in the REMOTE position, RF Drive
and PDM are disabled.
After performing these checks, set the
switch back in the REMOTE position.
Check jumper plug P4 next to the molex
connector J2 to ensure it is between the
correct terminals for your transmitter.
With only the low voltage on, check the
PDM drive to the output transistors of the
PDM Amplifiers. Connect an oscilloscope
across R21, R22, R41 and R42 on the PDM
Amplifiers with the ground side is away
from the output transistors.
A 13 volts peak-to-peak 60 kHz pulse
should be found at all eight resistors. The
resistors are 47,000 ohms, 2 watts each.
When replacing the PDM Amplifier mod-
ule, be sure an even coating of thermal
compound is applied to the mating heat sink
surfaces. Be certain to tighten down the
captive fasteners which mount the PDM
Amplifier module to the heat sink. Be espe-
cially sure to tighten the captive fastener
which attaches the PDM Pull Up board to
the large capacitor.
Rev. AE: 03-05-2002
888-2314-001
G-1
WARNING: Disconnect primary power prior to servicing.
Содержание Gates One 994 9202 002
Страница 4: ......
Страница 6: ...iv 888 2314 001 Rev X WARNING Disconnect primary power prior to servicing...
Страница 8: ...vi 888 2314 001 Rev X WARNING Disconnect primary power prior to servicing...
Страница 28: ...2 12 888 2314 001 Rev AC 2 29 00 WARNING Disconnect primary power prior to servicing...
Страница 40: ...Figure 5 1 PDM Flow Diagram 5 2 888 2314 001 Rev T Jan 1996 WARNING Disconnect primary power prior to servicing...
Страница 42: ...Figure 5 2 PDM Loop 5 4 888 2314 001 Rev T Jan 1996 WARNING Disconnect primary power prior to servicing...
Страница 43: ...Figure 5 3 RF Flow Rev T Jan 1996 888 2314 001 5 5 WARNING Disconnect primary power prior to servicing...
Страница 76: ...C 6 888 2314 001 Rev AE 03 05 2002 WARNING Disconnect primary power prior to servicing...
Страница 82: ...E 4 888 2314 001 Rev AE 03 05 2002 WARNING Disconnect primary power prior to servicing...
Страница 88: ...F 6 888 2314 001 Rev AE 03 05 2002 WARNING Disconnect primary power prior to servicing...
Страница 96: ...H 2 888 2314 001 Rev AA 8 18 1999 WARNING Disconnect primary power prior to servicing...
Страница 104: ...K 2 888 2314 001 Rev AE 03 05 2002 WARNING Disconnect primary power prior to servicing...
Страница 105: ...Figure K 1 Interface Board Rev AE 03 05 2002 888 2314 001 K 3 WARNING Disconnect primary power prior to servicing...
Страница 108: ...L 2 888 2314 001 WARNING Disconnect primary power prior to servicing...