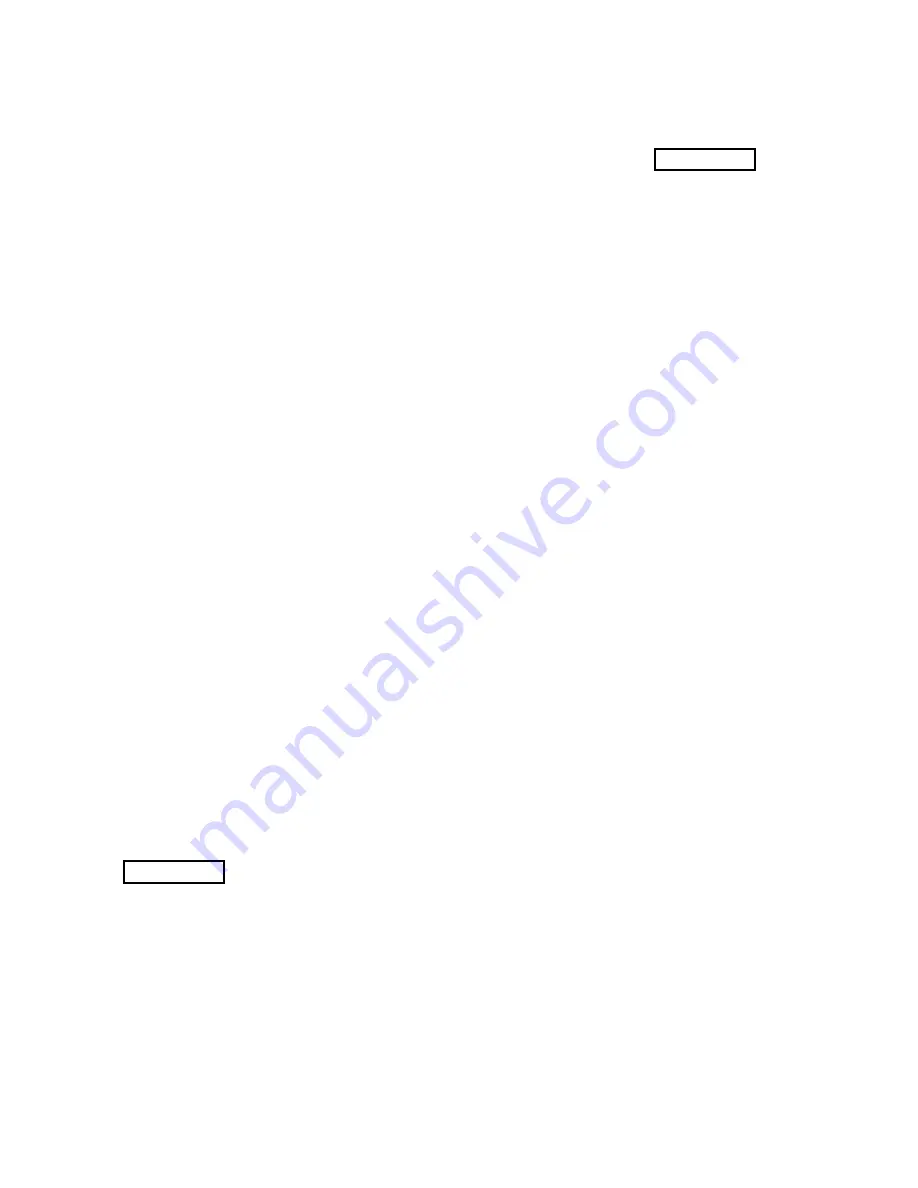
Generator, A15 at the fuses. Measure
each voltage with respect to ground. If
the voltages are under 19 Vdc, discon-
nect AC power and re-tap A20T1 to the
next lower primary voltage (taps 240, 0).
It is desired that the low voltage supply be
between 19 and 23 Vdc both plus and mi-
nus. Use a procedure of removing AC
power, grounding transformer taps, moving
the primary wiring to the next lower incre-
ment, then mea/-20 volt supplies,
to achieve the desired supply voltages.
Note: The transformer tap connections
are provided on TB3, terminals 15 through
19. Refer to Figure 2-3 for instructions on
using the Wago block terminals. Move the
AC connection as deemed appropriate to
achieve the desired output voltage.
i. Verify that all overload and fault indica-
tors can be extinguished by pressing the
Reset button.
j. Check the RF Drive reading on the Mul-
timeter. It should be close to the values
recorded on the factory test data sheet. If
it is not, re-check the low voltage trans-
former tapping. If needed, check the ac-
tual RF Drive on the PA module(s) per
the procedure in Section C.
k. Confirm that when any of the power ON
pushbuttons are depressed they illuminate.
The AC contactors in the pull out drawer
should not be heard energizing at this time
since F1 is not in the Interface board. Also,
the PDM KILL and PDM FAULT LED’s
will light in this condition.
l. Verify that depressing the OFF pushbut-
ton clears all power ON pushbuttons.
m. Disconnect all primary power, and in-
stall F1 in place on the Interface board.
n. Reapply primary power.
o. Rotate the multimeter switch to the Sup-
ply Voltage position. Depress the LOW
power pushbutton. The contactors
should close and apply main AC voltage
to the high voltage supply. The multime-
ter should show a voltage in the range of
220 to 270 on the 300 scale.
WARNING
IF CONTACTORS DO NOT CLOSE IN THE
P R E C E D I N G S T E P, R E M OV E A L L
POWER FROM TRANSMITTER AND EN-
SURE FAILSAFE INTERLOCK CON-
TACTS ARE JUMPERED OR EXTERNAL
FAILSAFE HIGH VOLTAGE INTERLOCK
CIRCUIT IS PROPERLY CONNECTED.
ALSO BE SURE THE REAR PANEL IS
SECURELY FASTENED.
p. Switch the multimeter to read Detector
Null and verify that the reading is zero.
q. Rotate the Low Power control pot clock-
wise and observe the PA Voltage, PA
Amps, and FWD Power meters, and
raise the power until the power level is
as stated on the factory Final Test Data
Sheets for the Low Power setting.
r. If the Detector Null reading increases
from zero, adjust the TUNING and
LOADING controls to minimize the
reading. This will match the PA to the
load impedance you are using.
During the initial tune-up, the null should be
found to be well within the range of the TUN-
ING and LOADING controls. If these con-
trols require considerable adjustment, the load
impedance on the transmitter is probably not
very close to 50 ohms. If considerable adjust-
ment is required, the impedance presented to
the transmitter output terminal should be
measured and corrected as necessary.
Although the transmitter is designed to
match up to a 1.5:1 VSWR, the optimum
condition is to terminate it into 50 ohms.
s. Depress Power Level number 2. The
power level should increase to near the
factory setting for this power level. It
probably will not be exactly the same
since the Fine Power adjustment has not
been made.
t. Adjust the Tuning and Loading controls
as necessary to null the Detector Null
reading to zero.
u. Compare the present readings against
the factory data for any major discrepan-
cies. If any exist, it should be investi-
gated at this time.
v. Progressively step the power level up-
ward by selecting each higher level,
check the readings against the Final Test
Data Sheets. Adjust the TUNING and
LOADING controls to minimize the De-
tector Null reading to zero.
w. Compare all readings against the Test
Data. Since the High Voltage trans-
former is tapped at 240 +11 from the
factory, it will probably be necessary to
change the transformer taps accordingly.
The need to do this or not is determined
by the Supply Voltage reading on the
Multimeter. It should be 250 to 265 volts
at full power.
A change from one transformer tap setting
to the next will produce about a 5% change in
DC Supply voltage. For example, moving
from 240, +11 to a setting of 240, 0 would
result in a DC Supply increase of about 5%.
NOTE
The smaller gauge wiring on the trans-
former primary is for the fans. These
smaller wires should always be left on
240, -11.
If you will be operating the transmitter
well below its rated power, then you may
leave the High Voltage transformer at it
highest primary setting. This will yield the
best overall performance if it is to be oper-
ating at a reduced power level.
WARNING
ENSURE ALL VOLTAGE IS REMOVED
FROM TRANSMITTER AND ALL POINTS
WHERE VOLTAGE HAS BEEN APPLIED
ARE GROUNDED BEFORE CHANGING
ANY TAPS ON THE TRANSFORMER.
x. Look at the range of the Fine Power
adjustment using the Raise/Lower
switches. It is desirable to set each of the
coarse power level pots (LOW through
HIGH) with the Fine adjustment in the
middle portion of its range.
The PDM Power Level reading on the
Multimeter is essentially the power control
settings. This reading may serve as a handy
reference for each desired power level.
These readings should be recorded when
the transmitter is initially set up, and used
later if you need to troubleshoot a power
level change.
y. Check or set each power level according
to your needs and compare all readings
with the factory test data. Report any
major discrepancies to the HARRIS
Service Department.
The GATES Series™ incorporates a pro-
tective action named Automatic Cutback in
which the transmitter will step to each suc-
cessively lower power in an effort to stay at
the highest tolerable power level when there
is an overload condition. This is similar to
the automatic foldback feature in some
transmitters, but is different in that the
power level steps down rather than going
through a gradual reduction.
Because of the Automatic Cutback fea-
ture, it is useful to set all 6 power levels. This
way, the transmitter output will remain at a
reasonable level should an Automatic Cut-
back occur. These power levels that you
would not ordinarily use may be intermedi-
ate power levels, or lower than your normal
operating powers.
2.7.2.
Modulation Monitor Carrier Level
After each power level has been adjusted,
you should set the RF sample level for your
Modulation Monitor. If you are not using a
modulation monitor at the transmitter, you
should leave all of the monitor level controls
set fully counter clockwise (minimum output).
The output levels of the monitor circuit are
independent of one another, so they may be set
in any order. While operating at a particular
power level, rotate each corresponding control
clockwise to achieve adequate carrier level.
Switching the REMOTE/LOCAL switch
(near the battery on the Controller board) to
2-6
888-2314-001
Rev. AC: 2/29/00
WARNING: Disconnect primary power prior to servicing.
Содержание Gates One 994 9202 002
Страница 4: ......
Страница 6: ...iv 888 2314 001 Rev X WARNING Disconnect primary power prior to servicing...
Страница 8: ...vi 888 2314 001 Rev X WARNING Disconnect primary power prior to servicing...
Страница 28: ...2 12 888 2314 001 Rev AC 2 29 00 WARNING Disconnect primary power prior to servicing...
Страница 40: ...Figure 5 1 PDM Flow Diagram 5 2 888 2314 001 Rev T Jan 1996 WARNING Disconnect primary power prior to servicing...
Страница 42: ...Figure 5 2 PDM Loop 5 4 888 2314 001 Rev T Jan 1996 WARNING Disconnect primary power prior to servicing...
Страница 43: ...Figure 5 3 RF Flow Rev T Jan 1996 888 2314 001 5 5 WARNING Disconnect primary power prior to servicing...
Страница 76: ...C 6 888 2314 001 Rev AE 03 05 2002 WARNING Disconnect primary power prior to servicing...
Страница 82: ...E 4 888 2314 001 Rev AE 03 05 2002 WARNING Disconnect primary power prior to servicing...
Страница 88: ...F 6 888 2314 001 Rev AE 03 05 2002 WARNING Disconnect primary power prior to servicing...
Страница 96: ...H 2 888 2314 001 Rev AA 8 18 1999 WARNING Disconnect primary power prior to servicing...
Страница 104: ...K 2 888 2314 001 Rev AE 03 05 2002 WARNING Disconnect primary power prior to servicing...
Страница 105: ...Figure K 1 Interface Board Rev AE 03 05 2002 888 2314 001 K 3 WARNING Disconnect primary power prior to servicing...
Страница 108: ...L 2 888 2314 001 WARNING Disconnect primary power prior to servicing...