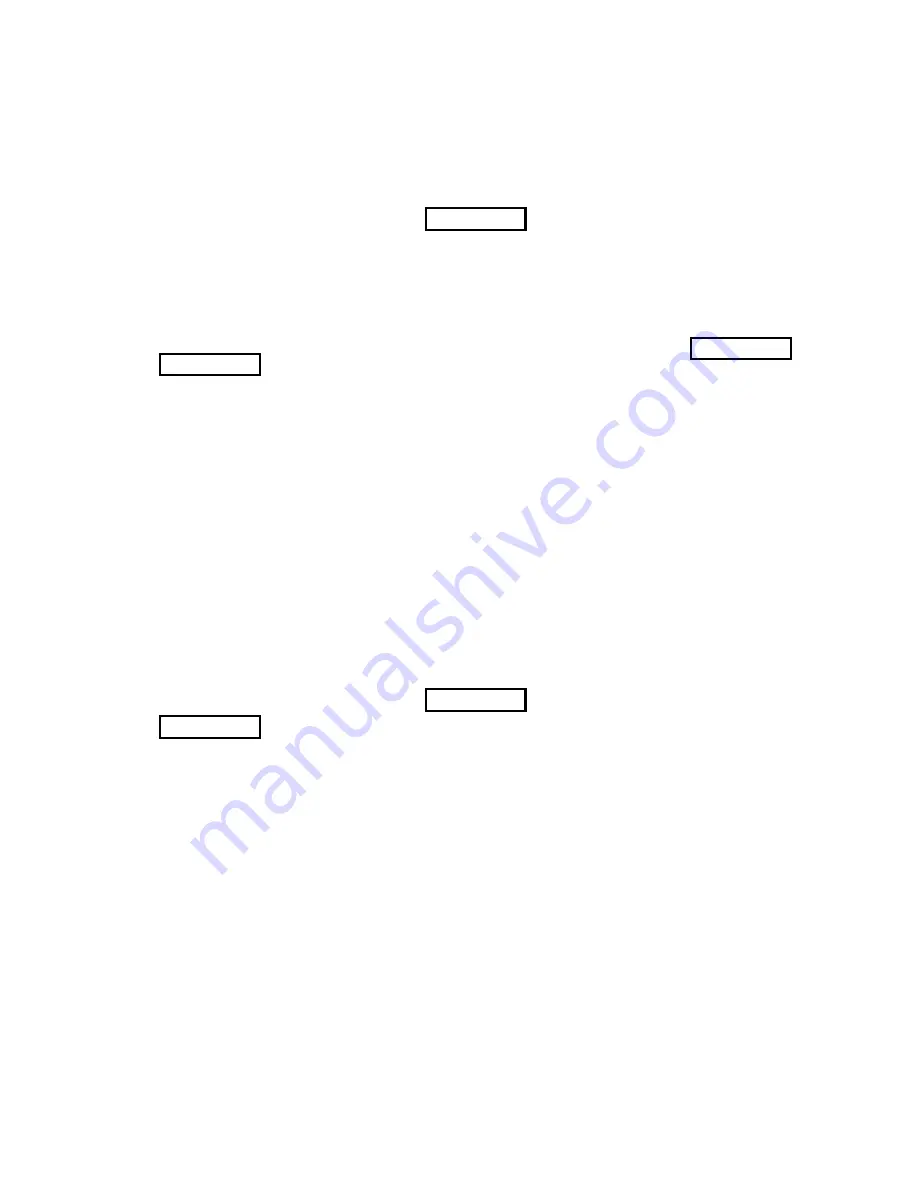
supply voltage. The transformer secondar-
ies are designated 60/75/90/105/120 Vdc.
Moving from the 105 tap to the 90 tap will
reduce the IPA supply voltage and the drive
level.
3.3.7.
IPA Tuning
Adjust A26L2 with a slotted screwdriver
for a peak in drive level as measured on the
PA modules.
Coarse IPA Tuning coil A26L1 has multi-
ple taps so that A26L2 can be kept within
its adjustment range. If the drive does not
peak within the range of L2, the tap setting
of A26L1 will have to be changed by select-
ing another tap position.
WARNING
THE IPA CIRCUITRY UTILIZES FAIRLY
HIGH VOLTAGES WHICH CAN CAUSE
ELECTRICAL SHOCK AND RF BURNS.
BE SURE TO DISCONNECT THE PRI-
MARY POWER AND DISCHARGE ANY
RESIDUAL VOLTAGES BEFORE MAKING
ANY TAP CHANGES ON A26L1. BE SURE
THAT THE SAFETY COVERS ARE IN
PLACE ON THE IPA SECTION BEFORE
REAPPLYING POWER.
Some of the components in the A26C1
position may not be used. Refer to the Fac-
tory Test Data Sheets for the proper amount
of capacitance.
If the RF Drive when peaked is lower than
25 volts peak to peak, make sure the IPA is
fully working, and that it is not being loaded
down by PA failures. Refer to the trou-
bleshooting procedures, as well as the
checks of the PA modules.
WARNING
ENSURE ALL VOLTAGE IS REMOVED
FROM TRANSMITTER AND ALL POINTS
WHERE VOLTAGE HAS BEEN APPLIED
ARE GROUNDED BEFORE CHANGING
ANY TAPS IN THE FOLLOWING STEP.
If the drive is not low because of a com-
ponent failure, then the IPA power supply
secondary will have to be tapped for a
higher voltage output. For example, moving
a tap from the 105 volt connection to the
120 volt connection will increase the IPA
supply voltage and the RF drive level.
3.3.8.
PA Voltage Electrical Zero
Unplug P2 from the PDM Generator so
that there will be no PA voltage when the
high voltage is energized.
Energize the high voltage by depressing
one of the power level buttons. The contac-
tors should energize, and Supply Voltage
should appear on the Multimeter.
Adjust R31 on the Controller board to
make the PA Voltmeter read zero.
3.3.9.
PA Volt Meter Calibration
The PA volt meter can be calibrated
against an external meter of known accu-
racy, using the following procedure.
WARNING
TURN OFF TRANSMITTER AND DIS-
CHARGE HIGH VOLTAGE BEFORE PRO-
CEEDING.
Route some long voltmeter leads to the PA
modules through one of the bottom side
holes made for a cable entrance.
Connect the positive lead of the volt meter
to the 260 volt line of a PA module (L11 or
the fuse, for example). Connect the negative
lead to the cathode of CR13 on the PA
board. This is the same electrical point as
the small banana jacks.
Turn the transmitter on at high power.
Adjust R76 on the Controller board to make
the front panel PA voltmeter agree with the
external voltmeter.
Turn off high voltage. Allow discharge of
power to zero. Remove voltmeter leads.
3.3.10.
PA Current Calibration
The PA AMPS meter can be calibrated
against an external meter using the follow-
ing procedure. The external meter and its
leads must be capable of accurately reading
at least 12 amps for a GATES ONE, at least
30 amps for a GATES TWO, and at least 60
amps for a GATES FIVE.
WARNING
ENSURE ALL POWER IS REMOVED
FROM THE TRANSMITTER BEFORE AT-
TEMPTING TO ROUTE THE LEADS IN THE
FOLLOWING STEPS.
Locate the DC Ammeter where it can be
seen from front of transmitter and route its
leads through one of the bottom side access
holes and up through one of the wiring
grommets.
Interrupt the connection between the
white, PA supply wires and PA metering
shunt (A19R6) on the floor of the transmit-
ter below the IPA. Insert leads from external
DC ammeter in series with PA metering
shunt and PA supply wires observing proper
polarity (positive goes toward the PA
shunt).
Be sure the external DC ammeter leads are
positioned so they will not short to ground.
If a Clamp On DC Ammeter is used, insure
that it is not RFI or EMI sensitive.
Turn transmitter on at HIGH power and
adjust the power level to set the reading on
the external ammeter on a convenient cali-
bration level.
Adjust A19 R10 (on the floor of the trans-
mitter below the Interface board) to make
the PA AMPS meter read the same as the
external meter.
3.3.11.
Power Supply Current Calibration
The Power Supply current can be cali-
brated against an external meter using the
following procedure. The external meter
and its leads must be capable of reading at
least 6 amps for a GATES ONE, at least 20
amps for a GATES TWO, and at least 30
amps for a GATES FIVE.
WARNING
ENSURE ALL POWER IS REMOVED
FROM THE TRANSMITTER BEFORE AT-
TEMPTING TO ROUTE THE LEADS IN THE
FOLLOWING STEPS.
Locate the DC Ammeter where it can be
seen from front of transmitter and route its
leads through one of the bottom side access
holes and up through one of the wiring
grommets, to near the high voltage rectifi-
ers.
Connect the DC Ammeter in series with
the supply current shunt resistor A19R7.
This is located above the PDM Filter
boards. Connect the positive side of the DC
Ammeter to the shunt (leave the white
wire in place on the shunt).
The negative side of the meter should
connect to the black welding cable removed
from the shunt.
Turn the transmitter on at HIGH POWER,
and adjust the power level to some conven-
ient calibration level.
Note the reading on the external meter,
and adjust R25 on the Controller board to
make the Supply Current reading on the
Multimeter agree with the external meter
reading.
3.3.12.
Power Output Calibration
Connect the transmitter into a load with
the capability of accurately measuring the
power output. This is best done with a cal-
orimetric dummy load, where the water
temperature rise is measured against a
known flow rate. A second choice is a
dummy load and an RF ammeter of known
accuracy.
Operate the transmitter at a convenient
power level within the capabilities of the
test setup.
Calibrate the Power Output meter to the
same reading as measured externally using
R85 on the Controller board.
Rev. AD
888-2314-001
3-5
WARNING: Disconnect primary power prior to servicing.
Содержание Gates One 994 9202 002
Страница 4: ......
Страница 6: ...iv 888 2314 001 Rev X WARNING Disconnect primary power prior to servicing...
Страница 8: ...vi 888 2314 001 Rev X WARNING Disconnect primary power prior to servicing...
Страница 28: ...2 12 888 2314 001 Rev AC 2 29 00 WARNING Disconnect primary power prior to servicing...
Страница 40: ...Figure 5 1 PDM Flow Diagram 5 2 888 2314 001 Rev T Jan 1996 WARNING Disconnect primary power prior to servicing...
Страница 42: ...Figure 5 2 PDM Loop 5 4 888 2314 001 Rev T Jan 1996 WARNING Disconnect primary power prior to servicing...
Страница 43: ...Figure 5 3 RF Flow Rev T Jan 1996 888 2314 001 5 5 WARNING Disconnect primary power prior to servicing...
Страница 76: ...C 6 888 2314 001 Rev AE 03 05 2002 WARNING Disconnect primary power prior to servicing...
Страница 82: ...E 4 888 2314 001 Rev AE 03 05 2002 WARNING Disconnect primary power prior to servicing...
Страница 88: ...F 6 888 2314 001 Rev AE 03 05 2002 WARNING Disconnect primary power prior to servicing...
Страница 96: ...H 2 888 2314 001 Rev AA 8 18 1999 WARNING Disconnect primary power prior to servicing...
Страница 104: ...K 2 888 2314 001 Rev AE 03 05 2002 WARNING Disconnect primary power prior to servicing...
Страница 105: ...Figure K 1 Interface Board Rev AE 03 05 2002 888 2314 001 K 3 WARNING Disconnect primary power prior to servicing...
Страница 108: ...L 2 888 2314 001 WARNING Disconnect primary power prior to servicing...