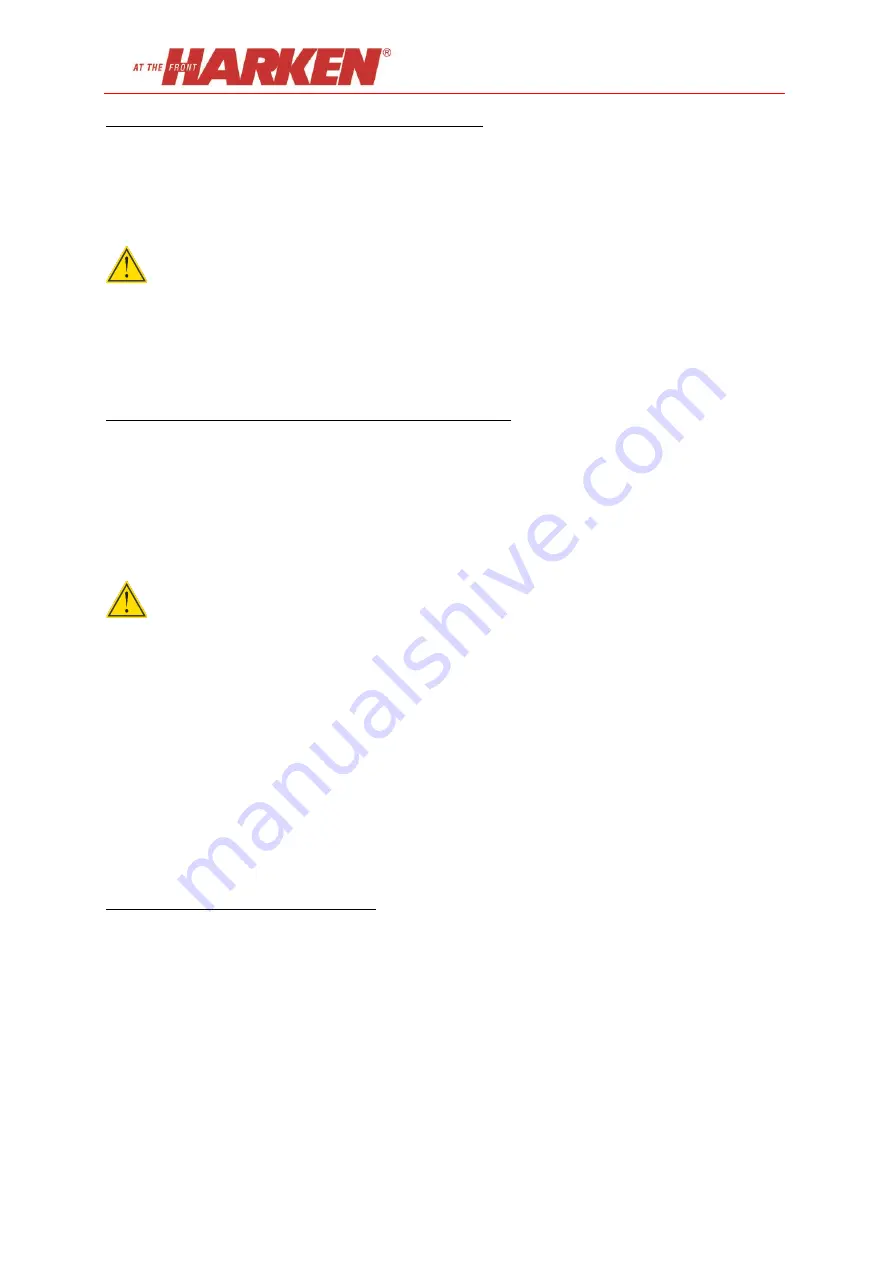
Rev.0
–
19/03/2021
17
9.1.3 Hydraulic motor installation procedure
The pressure lines must be connected to the motor using the approved size and type
hydraulic hose.
WARNING! - Do not remove the plugs on the Tensioner motor connections until
absolutely necessary to prevent contamination.
Each 90° hose bend causes pressure loss and decreases performance - avoid where
possible. If a 90° bend is needed, use a 90° swept hose fitting not a 90°elbow. Do not exceed
the minimum bend radius specified by the hose manufacturer.
9.1.3 Tensioner manifold installation procedure
Manifold can be mounted near the Tensioner or in a remote location.
The various functions must be connected to the manifold using approved size and type
hydraulic hose.
Before connecting make sure insides of hoses tubes are clean and free of debris that can
damage valves.
WARNING! - Do not remove the plugs on the manifold hydraulic connections
until absolutely necessary to prevent contamination.
Each 90° bend causes pressure loss and decreases performance - avoid where possible. If a
90° bend is needed, use a 90° swept hose fitting not a 90°elbow. Do not exceed the
minimum bend radius specified by the hose manufacturer.
Manifolds drilled through for 2xM8 mounting fasteners.
The max pressure is set on the valve PR1 on the Tensioner manifold, during the
commissioning of the system, it should be verified that during the pay-out the sheave does
not slip on the rope: in this case, reduce the pressure.
The drag of the Tensioner during the pay-in is set by the valve RV1 on the manifold, to
increase the drag screw the valve (to reduce unscrew), also in this case verify that in all
conditions the sheave does not slip on the rope.
9.1.4 PLC Control requirements
•
The Hydraulic Tensioner manifold needs to be connected to the PLC for the solenoid
valve control. In the pay-in direction the Tensioner motor is not powered, the
Tensioner is freewheeled by the pull of the Captive.
On the pay-out, the solenoid valve should be activated.
•
Tensioner should be operated for a slightly longer period than the winch. It should be
switched on 0.5 seconds before releasing the winch brake and deactivated 0.5
second after the brake is engaged again.
Содержание Tensioner CT0
Страница 1: ...Rev 0 19 03 2021 1 Tensioner CT0 USER AND MAINTENANCE MANUAL ...
Страница 12: ...Rev 0 19 03 2021 12 8 2 Hydraulic Tensioner Outline ...
Страница 18: ...Rev 0 19 03 2021 18 9 1 5 Tensioner Manifold structure ...
Страница 19: ...Rev 0 19 03 2021 19 9 1 6 Hydraulic Motor connections ...
Страница 29: ...Rev 0 19 03 2021 29 10 2 3 Disassemble procedure Step 1 Step 2 Step 3 ...
Страница 30: ...Rev 0 19 03 2021 30 Step 4 Step 5 Step 6 ...
Страница 31: ...Rev 0 19 03 2021 31 Step 7 Step 8 Step 9 ...
Страница 32: ...Rev 0 19 03 2021 32 Step 10 Step 11 Step 12 ...