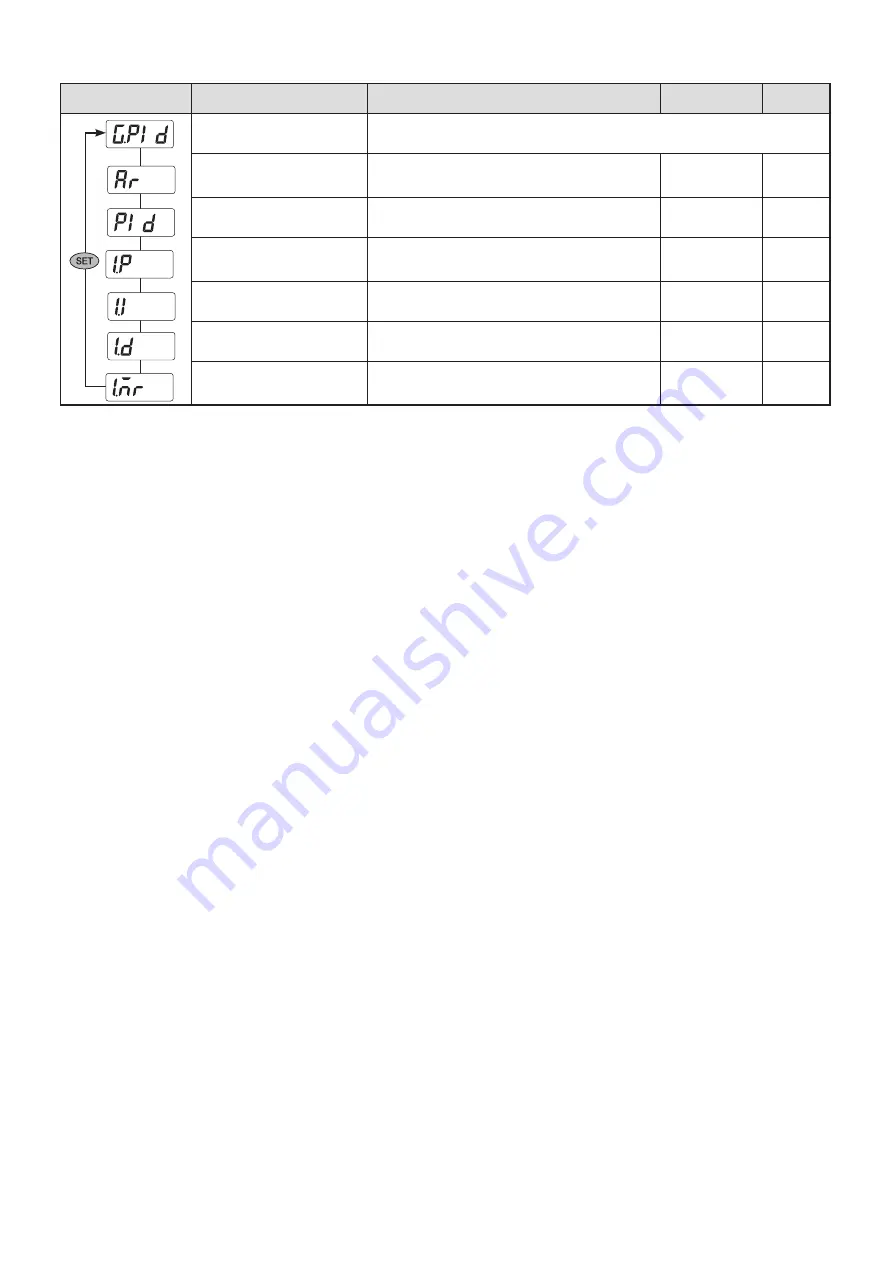
22
Signal
Item
Setup range
Display condition Initial value
PID setup group
Setup below items.
Anti Reset wind up
Auto/50.0 ~ 200.0 %
P.I.D
control
Auto
PID indication group
OFF / P1Gr ~ P4Gr
Always
0
n. Proportion
0.1 ~ 999.9 %
P.I.D
control
5.0 %
n. Integral
OFF / 1 ~ 6000 sec.
Always
240 sec.
n. Differential
OFF / 1 ~ 6000 sec.
Always
60 sec.
Manual reset
-5.0 ~ 105.0 %
Integral
time OFF
50.0 %
8-1-7. PID Setup Group
1) Anti Reset Wind Up :
Anti Reset Wind Up operation is carried out to prevent over-integral when the control output value reached
the limitation. Integral time is not “0” and integral time executes the ARW operation under the following
conditions when AUTO is selected for the auto tuning execution from the auto tuning setup group.
·DV≥0 & output value maximum restriction
·DV<0 & output value maximum restriction
2) Selection of PID Indication Group Number :
The PID control integer possesses 4 types and the operated PID integer can indicate and set up the items
when selecting manual operation. The operative integer of the PID group in agreement with the selected
number from the auto tuning selection in the auto tuning setup group is applied to each pattern segment of
4 types due to the selection of pattern segment PID group number of segment #0 in memory program
setup mode.
3) n. Proportion :
If select PID 1 group (P1GR) from the setup item of PID indication group number selection, 1 group
proportion (1.p) with n. proportion is indicated. Here, the proportional value of the operated 1 group is
indicated and can be changed and set up manually.
4) n. Integral Time :
According to the PID indication group number selection, 1~4 group integral time will be indicated in the
setup item and will be automatically remembered and manually changed/set up due to the auto tuning.
5) n. Differential Time :
According to the PID indication group number selection, 1~4 group differential time will be indicated in the
setup item and will be automatically remembered and manually changed/set up due to the auto tuning.
6) Manual Reset :
If “0” is selected as the integral time, variation occurs in control due to proportionate movement.
Such variation can be eliminated through manual reset.
(Parameter appears only when the integral time is set up “0”)
Содержание NP100
Страница 1: ...Manual NP100 Programmable Controller...