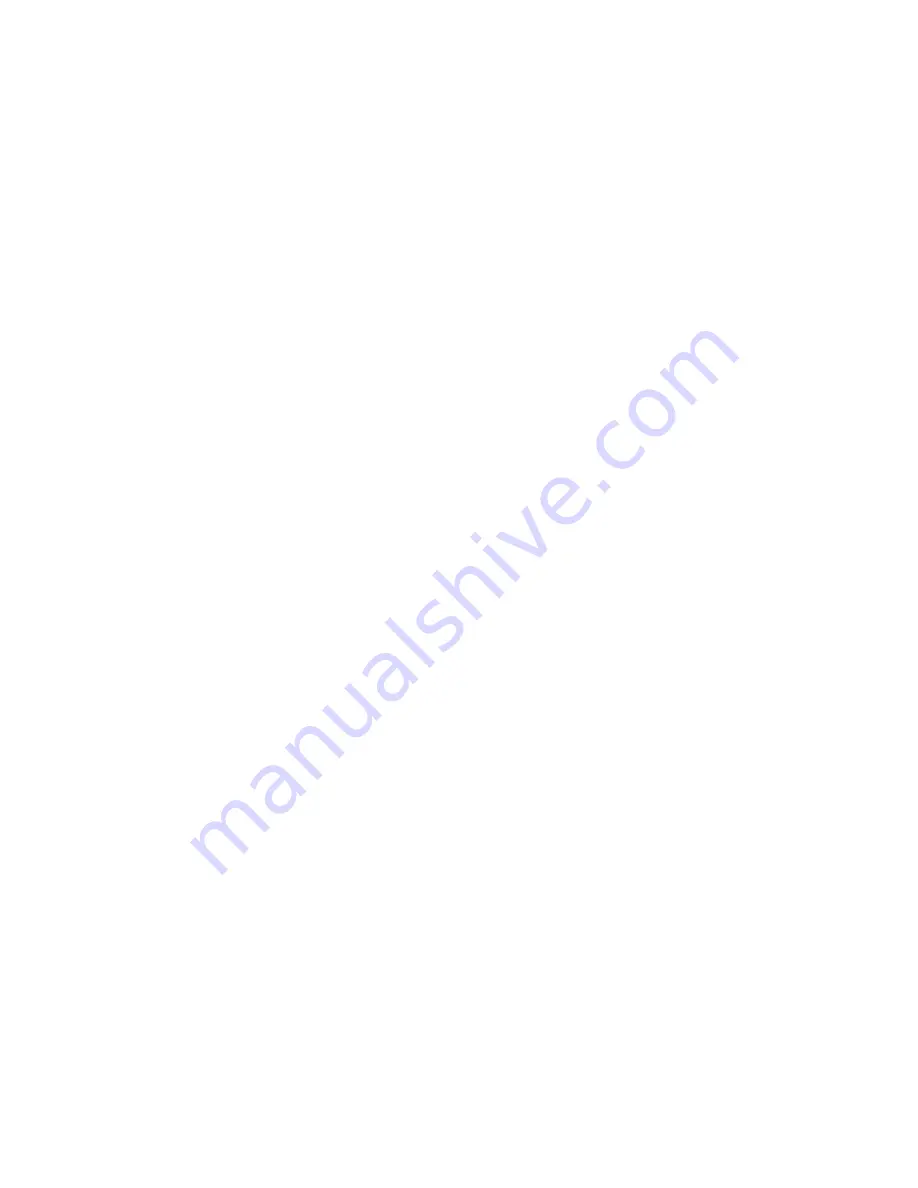
INSTALLATION
Regulators should be protected from dirt and moisture
during storage. The arrow on the body should be in
the normal direction of refrigerant flow.
These valves
will not prevent reverse flow;
use check valves where
necessary. Regulators are normally in horizontal pipe
lines with pilots and manual-opening stems on top. Do
not rotate the position of the valve adapter or the valve
will not operate.
The system should be free of dirt, weld slag, and rust
particles. Regulators can be equipped with separate,
c l o s e - c o u p l e d i n l e t s t r a i n e r s . N o s m a ll , h i d d e n ,
internal screens are used. Gauges and gauge valves
should be installed on the inlet and outlet to help in
system diagnosis. Because of the many regulator pilot
combinations, during installation of a large job, the
regulator nameplates should be checked against piping
drawings to guarantee proper function for each location.
Where pilot solenoid control modules are used, the
nameplate coil voltage should be checked before wiring.
Pipe sizing, anchoring, valve rating, system design,
and other precautionary factors should be taken into
consideration to ensure “liquid hammer” will not occur
when the valve opens or closes.
The 5" and 6" valves are type HA4W with integral butt
weld end only. These steel-bodied regulators are directly
welded into the pipe line. During welding, the manual-
opening stem should be opened downward several turns
to protect the Teflon seat from weld heat.
Welds should be annealed as necessary in accordance
with good practice. Painting of valves and welds is
recommended for corrosion protection. Pipe covering,
where applied, should have proper moisture barrier.
Before putting valves into service, all pipe connections,
valve seats, cover seals, and stem seals should be tested
for leaks at pressure levels called for in appropriate
codes.
ELECTRICAL
When the electric shut-off, wide-opening, or dual feature
is supplied, a Hansen low-wattage, molded electrical coil
is included. Standard coil voltages are 115V, 208/230V,
or 24V at 50/60Hz. Other voltages available. The coil
properly operates between 85% and 110% of the rated
voltage. Coils should only be energized while on the pilot
solenoid tube. Unless otherwise specified, the standard
coil with a ½" fitting for conduit is supplied with valves.
A
watertight solenoid coil
with 18" (450 mm) long
wire pigtail leads and a steel frame housing with a ½"
conduit fitting is
standard
.
Optional
D I N Plu g C o il s
are for grounded cord
connections and include the necessary DIN plug socket
with gasket.
Hansen long life Beacon Pilot Lights are available. They
incorporate a totally encapsulated, unique secondary
wound coil and LED light in a compact disc. These pilot
lights require no additional wiring.
Note: Beacon Pilot Lights are for AC voltage coils only.
MATERIAL SPECIFICATIONS
Body:
¾" through 4": Ductile iron, ASTM A536
5" & 6": Cast steel, ASTM A352 LCB
Adapter: Ductile iron, ASTM A536
Piston: Steel, disc type, Teflon piston seal
V-Port/Seat: ductile iron, with Teflon seat
Main Seat: ¾" through 1¼": integral ductile iron
1½" through 6": stainless steel, removable
Gaskets: Nonasbestos, graphite composite
Manual Opening Stem: Steel, plated
Pilots: Stainless steel trim
Pilot Orifice: Stainless steel
Flanges: Forged steel, ASTM A105
Safe Working Pressure: 400 psig (28 bar g), 600 PSIG
(41 bar g) available contact factory
Operating Temperature: – 60°F to +240°F (– 50°C to
+115°C)
ADVANTAGES
These valves combine modern design and new age
materials with advanced manufacturing techniques
and
intense
quality control to offer a significantly
superior and reliable product. Their ductile iron bodies
are stronger and more rugged than common cast iron,
or so called semi-steel (class B iron), valves. They are
more dirt resistant than full skirted-piston-design valves.
All regulators use energized Teflon dirt-wiping piston
seals which operate reliably, even under dry, oil-free
conditions. The screw-on control modules (pilots) are
easy to change and can be used on all valve sizes. All
valves incorporate Teflon seating and stainless steel
spring closing. Manual-opening stems are located on
top of valves, up and away from dirt and rust particles
to avoid thread jamming. Nonasbestos gaskets are
standard. These standard regulator valves use the same
flanges and spacing as R/S model A4A, except 1¼"
(32mm). Special Hansen 1¼" 4-bolt regulators are
available from stock to exactly replace R/S 1¼" A4A only.
SIZING
Proper regulator valve sizing is important for smooth
operation and long, trouble-free life of the valve.
Therefore, capacity of the regulator at both the maximum
and minimum flow and
pressure drop
should be
analyzed. Pressure regulators will operate satisfactorily
to approximately 15% of the maximum capacity of valve
based on the corresponding pressure drop. In extreme
cases, downsizing or two smaller regulators in parallel
are necessary. For pressure drops exceeding 45 psi
(3.1 bar g), special construction may be required. Contact
the factory.
2
R429d
AUG 2015