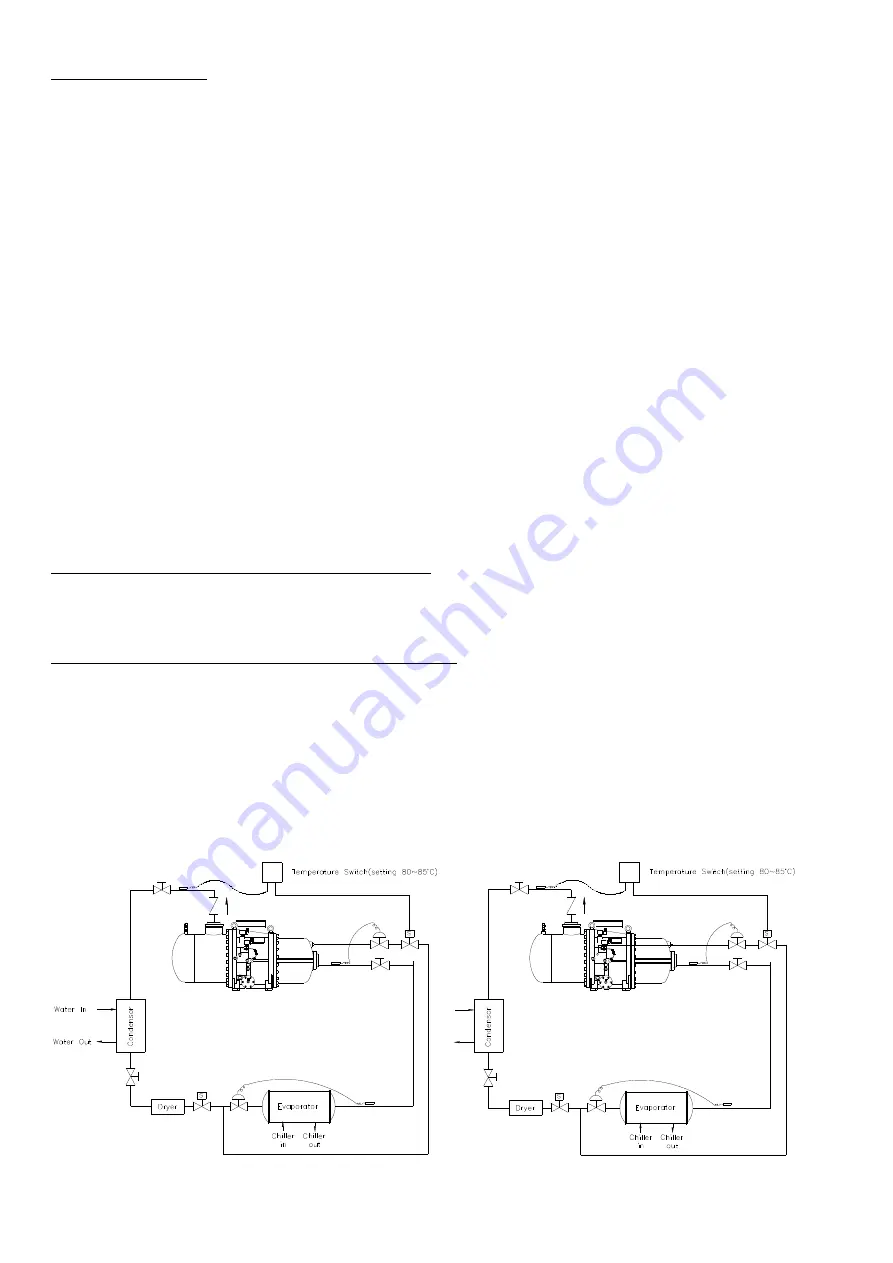
55
7. Applications
7.1 Additional cooling
When compressors operate at following application conditions, installation of an additional cooling apparatus is
recommended to control discharge temperature, maintain proper temperature of lubricant and ensure safety of the
motor.
Air-cooled system
High compression ratio system such as heat pump, low temperature and refrigeration systems
High discharge temperature system such as heat recovery system
Any other heavy duty application
There are two type of additional cooling methods:
a. Liquid injection applications
In areas with high condensing temperature and/or low evaporating temperature as in the limitation diagram, additional
cooling is required in order for the compressor to work properly. A relatively simple method of additional cooling is
direct refrigerant injection into the compressor, to motor or compression chamber or to both places at the same time
once needed.
The purpose of liquid injection systems is to prevent the compressor from overheated. The system is with a liquid
injection expansion valve between the liquid line and compressor for cooling down the compression chamber and
motor to ensure the continuous and safe running of the compressor. The suction superheat should be controlled
between 5K~10K for air-cooled and heat pump chillers by means of expansion valve devices. These devices can be
adjusted by the stem of the expansion valve to control suction superheat by means of refrigerant flow rate. During the
initial startup, the loading of the chiller is heavy due to high temperature chilled water, so the liquid injection devices
capacity should be selected or calculated enough to reduce the overheat of the compressor.
Calculating the cooling capacity of liquid injection devices:
Liquid injection devices can be calculated with the HANBELL selection software or manually. For manual calculation,
consider the most extreme conditions to be expected during actual operations i.e. minimum evaporating temperature,
maximum suction gas super heat and condensing temperature.
Liquid injection applied with low temperature expansion valve:
When the compressor applied in the low temperature system (E.T.
≦
-10°C) the compression ratio is high at this
condition, also the discharge temperature will be very high. The design of the liquid injection system for low
temperature application is similar to the illustration shown in figure below. There are two connectors for the liquid
injection in the compressor, one is in the motor side to cool down the motor temperature and reduce the discharge
temperature. The other is in the compression chamber side and its function is to reduce the discharge temperature and
increase the compression efficiency. However, when additional cooling in compression chamber like economizer
operation, oil cooler application is used or when condensing temperature is low, discharge temperature be kept low
and liquid injection may not be turned on, although motor load is severe and motor coil temperature is high. This may
lead to motor failure. Therefore, in application mentioned above Pt100 or Pt1000 for liquid injection to motor is
recommended instead.
Figure 41 Liquid injection connected to motor
Figure 42 Liquid injection connected to compression chamber
Содержание RC2-1020AV
Страница 15: ...4 3 RC2 AV series compressor outline drawings ...
Страница 16: ...15 ...
Страница 17: ...16 UNIT SI mm Imperial in ...
Страница 18: ...17 ...
Страница 19: ...18 ...
Страница 20: ...19 ...
Страница 21: ...20 ...
Страница 22: ...21 ...
Страница 23: ...22 ...
Страница 24: ...23 ...
Страница 25: ...24 ...
Страница 26: ...25 ...
Страница 27: ...26 ...
Страница 28: ...27 ...
Страница 29: ...28 ...
Страница 30: ...29 ...
Страница 31: ...30 ...
Страница 32: ...31 ...
Страница 33: ...32 ...
Страница 34: ...33 SI mm Imperial in UNIT ...
Страница 35: ...34 ...
Страница 36: ...35 ...
Страница 37: ...36 ...