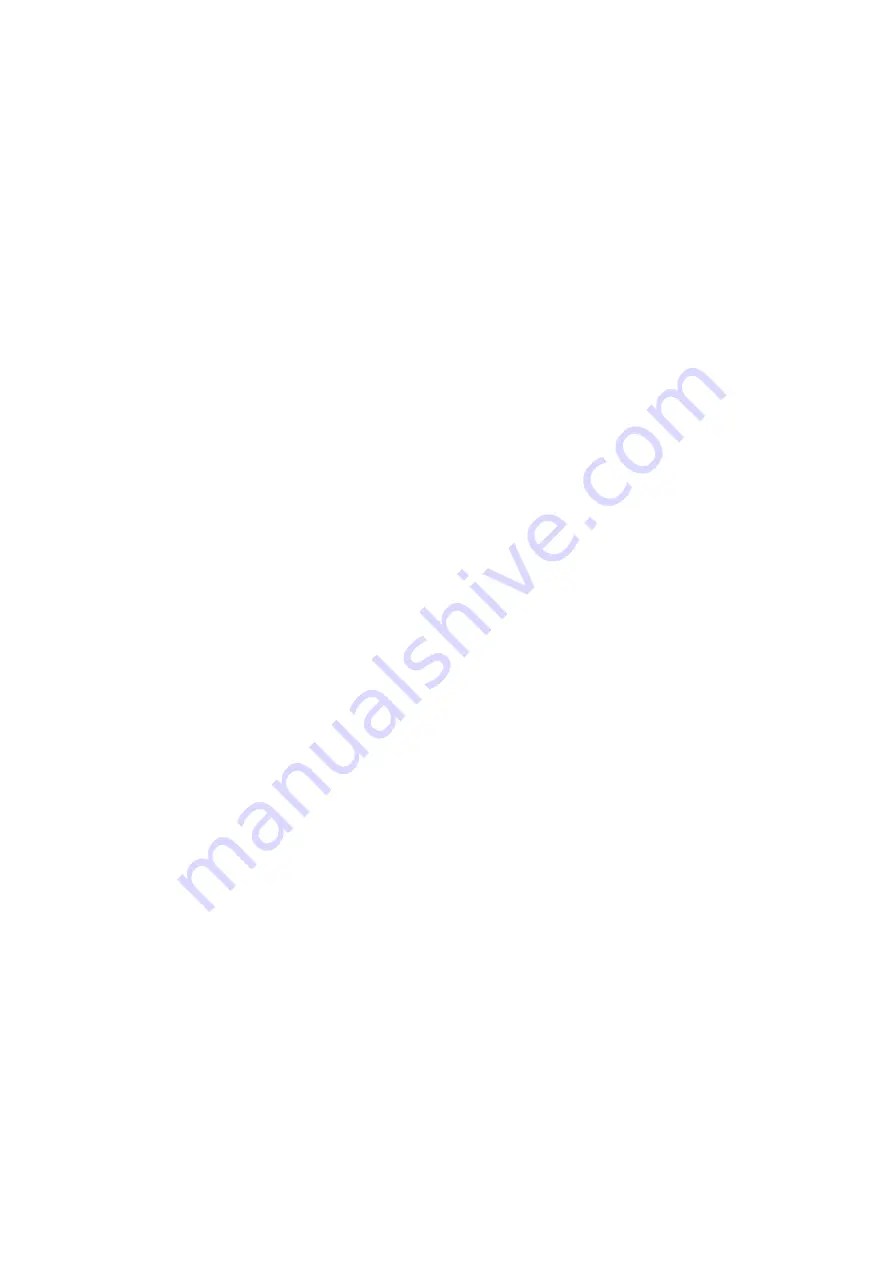
HAMWORTHY HEATING LTD
WESSEX-HE 200 BOILER
500001008/K
12
Main Burner Commissioning
Having established a satisfactory pilot flame and
reconnected the supply to the main gas solenoid
valve, the sequence described above will, after
switching the boiler on, be repeated. Instead of the
boiler going to lockout at the end of the safety time,
the main gas valves will open. After approximately 5
seconds the pilot valve will be de-energised and the
main flame should remain established under the
control of the flame monitoring system. The main
flame-proving signal should be 2.5-3.5 µA.
Turn the boiler switch and mains electrical isolator
‘OFF’, remove the Multi-Meter, and reconnect link
between terminals C1 & C2.
11.5 Gas Pressure Adjustment and Combustion
Checks
11.5.1 Gas Pressure Adjustment (Natural Gas
Only)
NOTE: - For adjustment relating to Propane firing,
refer to Appendix ‘A’.
After approximately 30 minutes of normal firing,
connecting a differential manometer to test points A &
B (either side of orifice) should check the gas
pressure differential across the gas orifice (reference
Figure No. 8). The pressure drop for Group H Natural
Gas should be 2.6mbar and minor adjustments to the
appliance governor may be necessary to correct for
site gas pressure conditions. Two double solenoid
valves arranged in parallel control the main gas. The
left hand valve (when viewed from the front) acts
when energised as a bypass without a governor (the
governor is rendered inactive by the addition of a
bypass screw, which must always remain in position
and fully inserted). The right hand valve contains the
appliance governor situated between the solenoids.
Remove the metal screw cap to reveal the adjuster
beneath.
NOTE!
The above is a first order check, Final Setting
must be made using a gas meter.
11.5.2 Combustion Checks
Details of the flue gas composition relating to Propane
firing can be found in Appendix ‘A’.
A flue gas sampling point is provided in the front
boiler casing (see Figure No. 6). To check
combustion take a flue gas sample from each module
test point and for reference CO
2
measurements
should be between 9 and 10% or 3.5 to 5.0% O
2
.
Normal CO levels should not exceed 200 ppm.
NOTE!
All the above measurements refer to
dry flue
gas
samples.
11.6 Temperature Limiter & Control Thermostats
11.6.1 Temperature Limiter
The temperature limiter is supplied factory set to 100°
C, a temperature that is normally satisfactory for low-
pressure hot water heating systems.
NOTE!
For high temperature applications, it is
essential that the water system static head or in the
case of pressurised systems, the system pressure, is
suitable for operation at elevated temperature, and
attention is drawn to the specific requirements of
BS
6644
and the HSE Guidance Note: PM5
(Automatically controlled steam and hot water
boilers). Refer also to section 8.11.
11.6.2 Control Thermostat Adjustment
Control thermostats are factory set to limit their
adjustment to 90°C however, the thermostat may,
under certain circumstances, be adjusted to operate
in excess of this temperature.
The minimum difference between the control
thermostat and temperature limiter
must not
be less
than 10°C.
When all settings and readings are satisfactorily
completed, tighten all test points and refit burner
cover.
7 External
Controls
The external controls used in typical boiler
installations, for both vented and unvented systems,
are shown in Figure No. 2. If different systems or
controls are to be used and there are any doubts as
to their suitability contact the manufacturer for advice.
8 Installation
Noise
In order to avoid the possibility of noise from the
installation, care should be taken to follow the
manufacturer’s instructions. Particular attention
should be paid to minimum water flow rates. If
acoustic insulation is added to the boiler, care must
be taken not to impede combustion or ventilation
airflow. If in doubt contact the manufacturer.
11.9 User’s Instructions
Upon satisfactory completion of commissioning and
testing, the commissioning engineer should hand the
User’s Instructions to the user or purchaser and
explain the method of economic and efficient
operation of the system. Ensure that the user or
purchaser is fully conversant with lighting, shutdown
and general operational and emergency procedures.
Содержание WESSEX-HE 200
Страница 6: ...HAMWORTHY HEATING LTD WESSEX HE 200 BOILER 500001008 K iv...
Страница 28: ...HAMWORTHY HEATING LTD WESSEX HE 200 BOILER 500001008 K 22 Figure No 2 Typical Boiler Installation...
Страница 41: ...HAMWORTHY HEATING LTD WESSEX HE 200 BOILER 500001008 K 35 NOTES...
Страница 42: ...HAMWORTHY HEATING LTD WESSEX HE 200 BOILER 500001008 K 36 NOTES...
Страница 43: ...Notes...