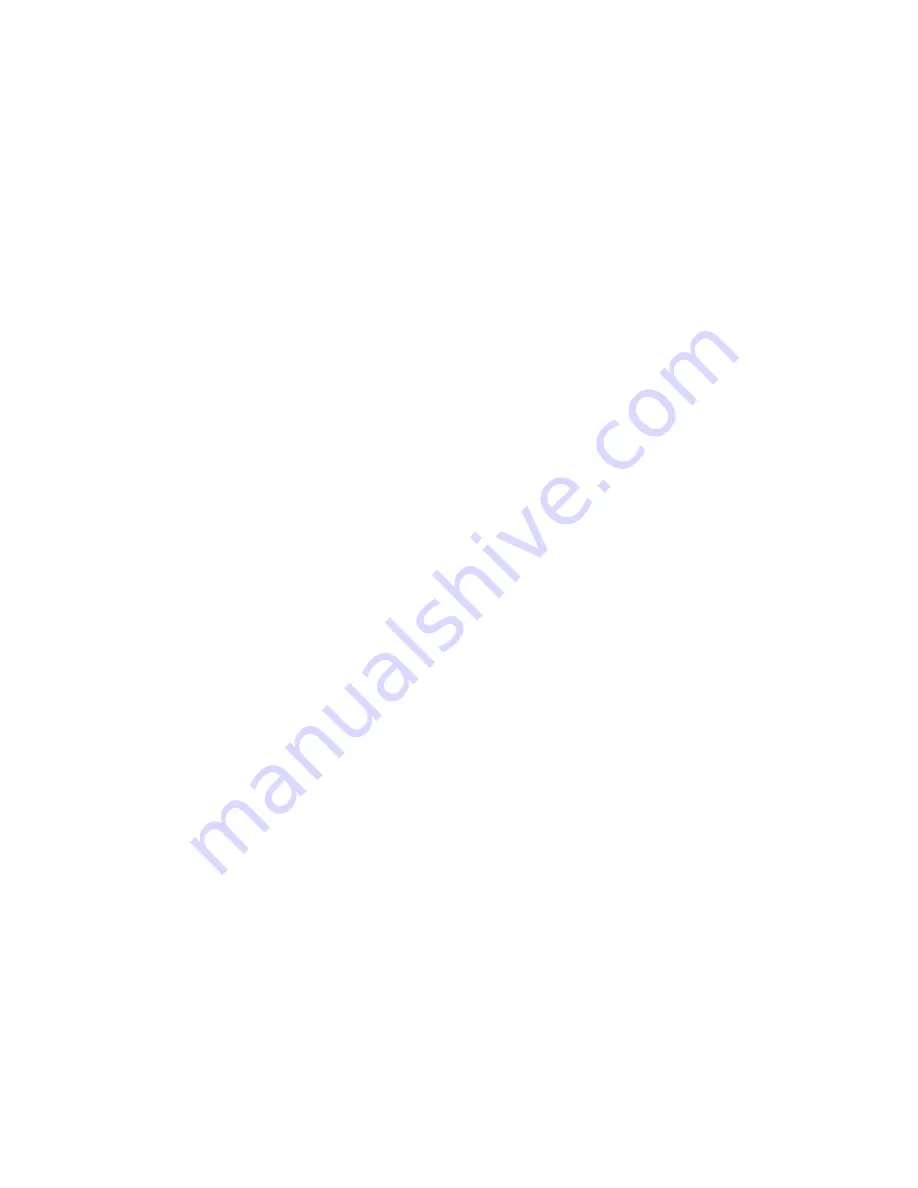
HAMWORTHY HEATING LTD
LILLIPUT HE
500001047/F
5
appliances.
Failure to install gas appliances correctly may
lead to prosecution. It is in your own interest,
and that of safety, to comply with the law.
The local gas region should be consulted at the
installation planning stage to either determine the
feasibility of providing a gas supply, or, where there
is an existing supply, to ensure that the meter
capacity is adequate for the rated input of the
proposed new boiler. An existing gas service pipe
must not be used without prior consultation with the
local gas region. A gas meter is connected to the
service pipe by the local gas region, or the local gas
region contractor.
Installation pipes should be fitted in accordance with
British Gas publication IM/16. Pipework from the
meter to the boiler must be of an adequate size to
pass the maximum required gas rate without
excessive pressure loss. Pipe of a smaller diameter
than the burner gas connection should not be used.
The complete installation must be tested as
described in IM/16.
Where it is necessary to use a gas booster, the
controls must include a low pressure cut-off switch
fitted upstream of the booster. The cut-off pressure
will be decided by the local gas region, who should
be consulted before a gas booster is installed.
A manual shut-off valve must be fitted on the
incoming gas supply pipe, in an easily accessible
position, adjacent to the boiler and clearly identified.
3.5 Oil
Supply
The oil storage and supply system should be
designed and installed in accordance with BS.5410
Part 1 or 2, as appropriate. The following notes are
given as guidance:-
Oil Storage Tank
- The oil storage tank should be
of sufficient capacity to permit economic deliveries
of oil to be taken. Reference should be made to oil
distributor for advice. The tank should be installed
such that:
a.
The oil outlet should be higher than the top of
the oil burner pump. If site conditions prevent this,
then a suction lift (or 'two-pipe') fuel supply system
must be used.
b.
The maximum head on the suction side of the
oil pump should not exceed 4 metres (14 feet).
c.
The base should be sloped away from the
outlet and towards a drain cock to allow draining of
any water or sediment from the tank.
d.
It is sited outside, if possible, and complies
fully with the requirements of the relevant British
Standards and Local Authority Regulations.
Oil Supply Lines
- The oil supply line(s) between
storage tank and burner should be run in copper,
steel or aluminium pipe. Galvanised pipes and
fittings should not be used. All pipework and fittings
must be oil-tight, with any screwed joints made good
with an oil resistant compound. The supply line
should terminate adjacent to the burner with an
isolating valve and metal bowl filter (with
replaceable filter element).
Gravity Feed Supply
- Where the delivery
connection of the storage tank is above the level of
the pump inlet on the burner a 'single pipe' gravity
feed system can be used. At no point in this system
should the supply pipework be higher than the
lowest level of fuel in the tank.
Suction Lift Supply
- where the delivery connection
of the tank is below the level of the pump inlet on
the burner a 'two-pipe' fuel supply system MUST be
used. This system uses the burner pump to provide
a circulation of oil to and from the tank.
N.B.
Burner pumps can be supplied ready for use on a
'single-pipe' system. For use on a 'two-pipe' system
it may be necessary to fit the pump with a by-pass
plug. Refer to technical information supplied with
burner.
The return line should terminate within the oil tank at
the same level as the suction line, in which case a
non-return valve is not required. If the return line
terminates above the fuel level, a non-return valve
MUST be fitted.
3.6 Flue
System
The flue system should be designed and installed in
accordance with the requirements of BS.5440 Part
1, BS.5854, BS.6644 and British Gas publication
IM/11. The following notes are given for your
guidance.
The boiler should be connected to a single flue
system in the case of a single boiler, or a common
flue header in the case of a multiple boiler
installation. Flue systems must be self supporting
and contain access for cleaning.
The size of the flue must be such as to guarantee
the efficient discharge of combustion products from
the building and should not be less than the
diameter of the flue outlet.
When designing the flue system, care must be taken
to ensure that any condensate that may form within
the system can be safely drained to a suitable waste
point, and that the flue material used is resistant to
the corrosive effects of that condensate.
The flue system should be designed such that the
flue terminates at least 1 metre above the roof
surface, or above the level of any nearby structure
which is within 2.5 metres of the flue.
The flue should not terminate adjacent to any