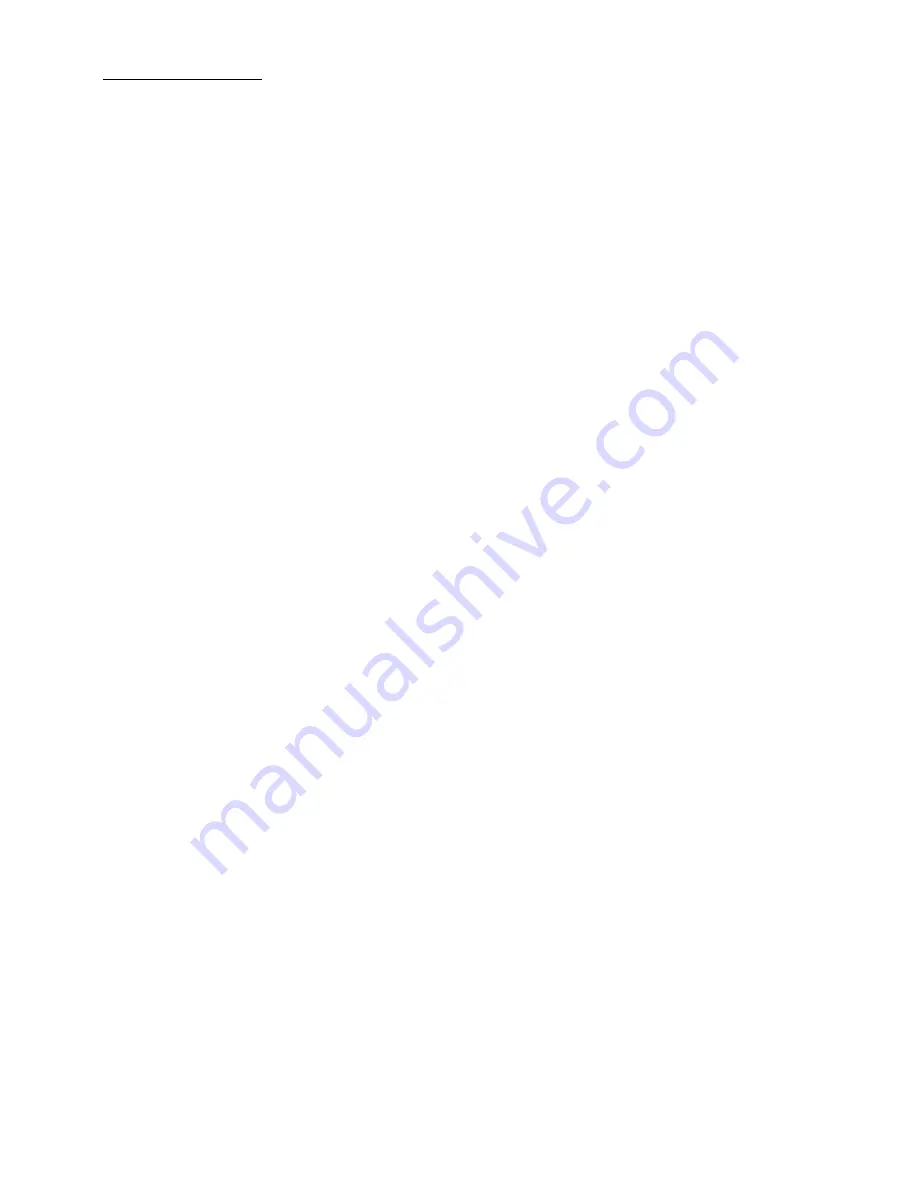
HAMWORTHY HEATING LTD
14
FLEET V series
500001213/G
5.0 BOILER ASSEMBLY
5.1 General
Boilers are despatched to site as fully assembled units. The flue manifold and pipe work set (where applicable)
are the only items that will need assembling on site.
Should access be an issue, the boiler modules can be dismantled to assist delivery into the plant room. To carry
out this process, carefully remove the top panel, the front cover and side panels from each module. This will give
access to 4 M10 nuts per module, securing the upper module to the lower module or base frame. Great care
MUST
be taken in separating and re-assembling the modules when in the required location, recognising the
weight - refer to section 2. It is recommended that M10 lifting eyes are fitted to the boiler chassis in the four
locations provided in the upright frame.
During assembly it is important to take care to prevent damage to the boiler casing.
Boiler positioning must allow the minimum clearances detailed in Section 3.0 to facilitate access for flue and pipe
work connections as well as maintenance. The boiler must be installed on a solid floor. In locating the boiler a
pallet truck is recommended so as to avoid damage to the casing parts
Health and safety.
Due to the weight of the boiler, care must be taken when manoeuvring the boiler. HHL
suggest the use of a pallet truck
5.2 Water Connections
The connections provided on the boiler (refer to Appendix E and figure 4.4) are suitable for direct connection to
the system pipe work. However HHL recommend the use of individual isolating valves, which should be fitted to
each module to enable isolation from the system. However, the arrangement must comply with the requirements of
BS 6644.
When installing water system pipe work, it must be self supporting and care must be taken to ensure that undue
stress is avoided on the boiler flow and return connections. It is recommended that unions are fitted local to the
boiler and outside of the casing, to permit future servicing requirements.
Each module is fitted with safety valve rated at 6bar. The valve discharge pipe is routed to the rear of the boiler,
where it must be piped to discharge via a tundish (not HHL supply) suitably located for ease of visibility.
The Fleet is designed to operate at 20°C
∆
T across the flow and return. Should the flow rate drop, the boiler
controls will modulate the burner to maintain 20°C
∆
T. The boiler module is fitted with a single speed circulating
pump and flow is controlled through a balancing valve, which must be checked and set during commissioning. As
a safety precaution, a flow switch is fitted to the boiler heat exchanger to shut the system down in the event of
sudden adverse flow conditions.
Where using Hamworthy Heating Ltd pipe work kits, assembly of these is detailed in Instruction Manual
500005134 supplied with kit.
5.3 Flue Connection
5.3.1
The Hamworthy Fleet V series boiler is designed for use with open flue systems type B23 - Intake from ventilated plant room
and discharge via horizontal/vertical flue.
For all B23 installations the Hamworthy supplied air inlet filter (Pt. No. 532812 008)
MUST
be used
1. With the boiler in its desired location, loosely engage the flue collector ducts into each other and position such
that the spigots will fit into the respective flue sockets at the rear of the boiler.
In assembling the flue ducts, it is advisable to lubricate the seal located in the socket fittings using the gel
provided, to enable easy movement and adjustment.
2.
Fit and secure the bottom closing plate to the base of the duct assembly.
Do not fit the flue manifold
at this stage as it may restrict access to the other connections.
Note:
Should modules be arranged in banks of 2 or 3 high, adjacent to each other, it is advisable to fit the water
and flue connections to each individual bank prior to fitting the connections to the adjacent bank(s).
Flue systems should be designed with reference to
BS 5440
part 1
,
IGE/UP/10
and
Third Edition of the 1956 Clean Air
Act Memorandum.
To comply with the requirements of the Clean Air Act 1956 a maximum of 150 kW may be terminated with
horizontal flue discharges.
Equivalent lengths for 90° bends and 45° bends are given in Appendix C.
Содержание F40V
Страница 2: ......
Страница 31: ...HAMWORTHY HEATING LTD 25 FLEET V series 500001213 G Figure 8 2 1 3 Operation and display philosophy...
Страница 40: ...HAMWORTHY HEATING LTD 34 FLEET V series 500001213 G Figure 8 3 11 Operating phases...
Страница 63: ...HAMWORTHY HEATING LTD 57 FLEET V series 500001213 G NOTES...
Страница 65: ...Please complete the information on the Registration Card cut out and return to Hamworthy Heating Ltd...
Страница 66: ......
Страница 67: ......