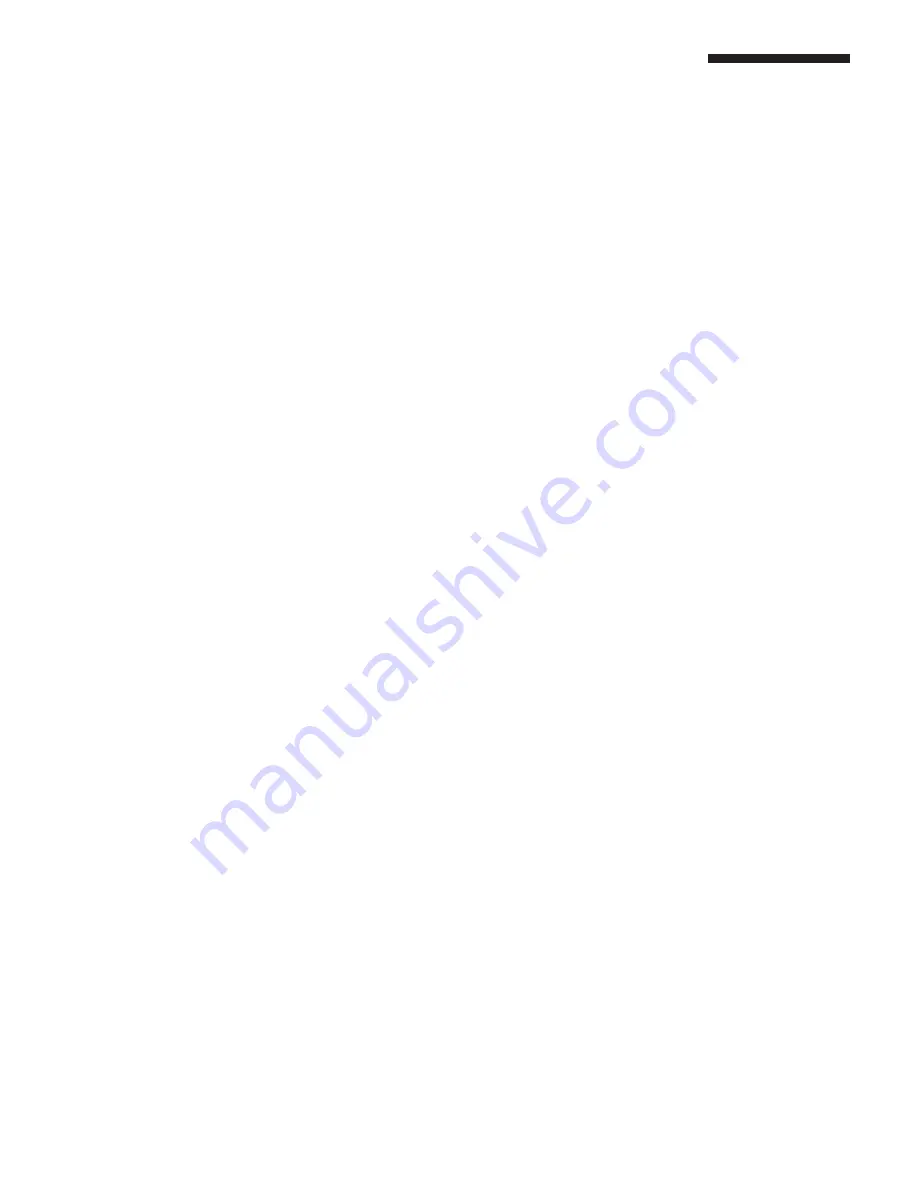
37
PART 6. START-UP PROCEDURES
3. Turn on gas shutoff valve (located
outside the cabinet on the bottom
of the appliance) so that the
handle is aligned with the gas
pipe. If the handle will not turn by
hand, don’t try to repair it; call a
qualified service technician. Force
or attempted repair may result in
a fire or explosion.
4. Do not use this appliance if
any part has been under water.
Immediately call a qualified service
technician to inspect the appliance
and to replace any part of the
control system and any gas control
which has been under water.
5. The EVO Heater shall be installed
so the gas ignition system
components are protected
from water (dripping, spraying,
rain, etc.) during appliance
operation and service (circulator
replacement, condensate trap,
control replacement, etc.).
B. LIGHTING INSTRUCTIONS (continued)
START-UP PROCEDURES
C. OPERATING INSTRUCTIONS
D. ADJUSTING THE TEMPERATURE ON THE EVO DISPLAY
1.
STOP!
Make sure you have read
the safety information above.
2. Turn off all electric power to the
appliance.
3. This appliance is equipped
with an ignition device which
automatically lights the burner. Do
not try to light the burner by hand.
4. Turn gas shutoff valve clockwise
to “off” The handle will be
horizontal; do not force it.
5. Wait five (5) minutes to clear
out any gas. If you then
smell gas, STOP! Follow the
instructions from Section B:
Lighting Instructions in the safety
information. If you don’t smell
gas, go to the next step.
6. Turn the gas shutoff valve counter
clockwise to “on” The handle will
be vertical.
7. Turn on all electric power to
appliance.
8. Set the thermostat to the desired
setting.
9. If the appliance will not operate,
follow the instructions “To Turn
Off Gas To Appliance” (Part 7,
Section F, page 46 and call your
service technician or gas supplier.
Enter the menu labeled Setpoint
in the upper right of the display
to set the desired operating water
temperature. On a boiler, this will
be based on the leaving water
temperature. On a water heater it
will be based either on a connected
external (storage tank) sensor, or,
if there is none connected, it will
operate based on the incoming
water temperature. The range is
factory-set at 50–160°F for water
heaters and 50–195°F for boilers.
Other special ranges are available
by contacting the factory.
If other
temperature settings are required,
contact Hamilton Engineering
Company, Inc.
Other special
parameters may be set by entering
a password in the display, varying
from end user, installer, advanced,
and factory levels. The display can
show either °F or °C set in the setup
menu, then display options.