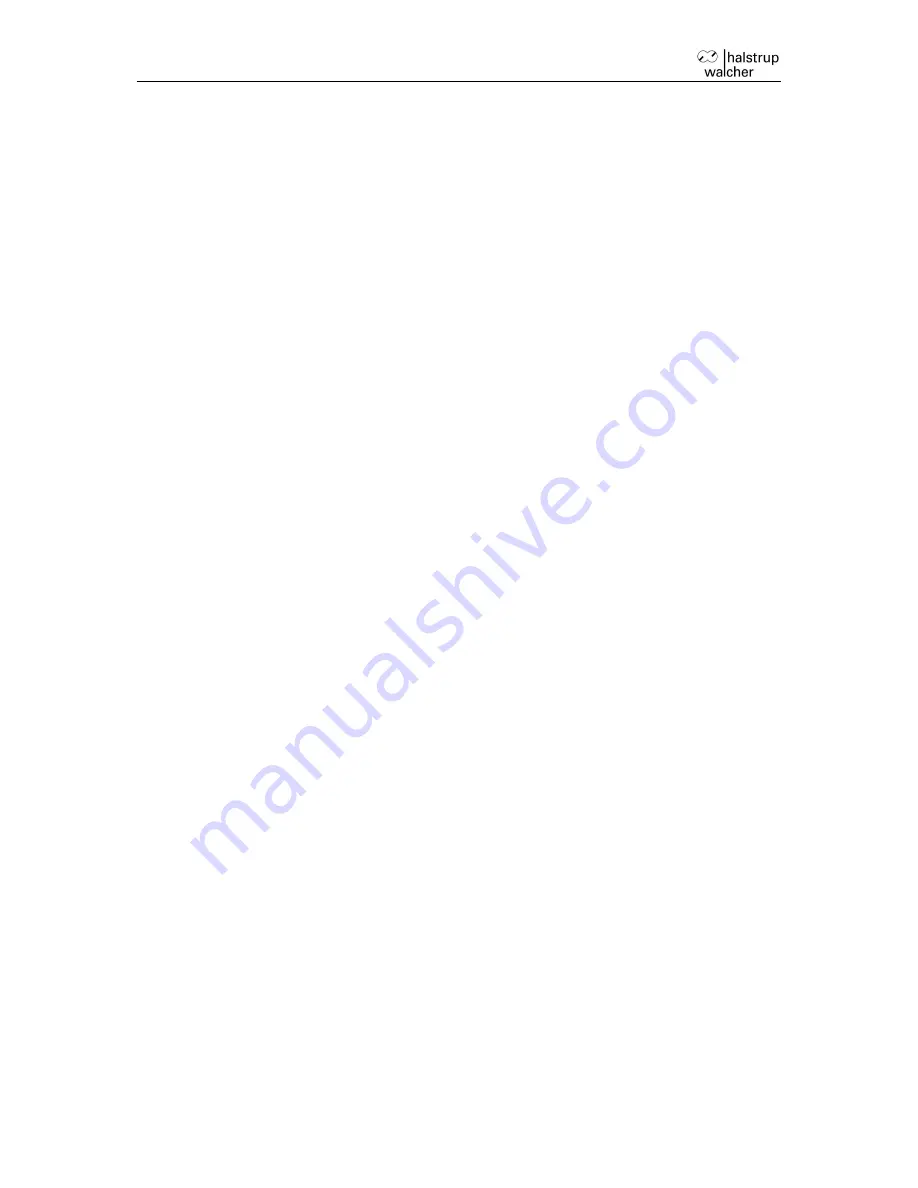
PSx3xxDN Instruction Manual
32
i) Devices with optional friction brake
The device model PSE34xxDN can be supplied with an optional friction brake. This
brake prevents the output shaft from turning when the power supply to the motor is
removed, or, if the motor holding torque is too low.
A run command is not approached immediately but only after a short idle period to
tighten the brake.
The brake releases at the end of every run.
To adjust the drive manually, it is first necessary to remove the corresponding rubber-
plug in the top cover (see drawings at the end of these instructions). The drive can
then be rotated using a hex wrench NW4. This is quite difficult as the operator has to
overcome both any torque present at the output and the force of the friction brake.
j) Reference runs
The PSx3xxDN positioning system is equipped with an absolute measuring system,
therefore there’s no need for a reference run when powering on the drive. However, if
in certain cases a reference run onto a hard block should be desired (e.g. uniquely
when installing the drive at a machine), the course of action should be the following:
1) Before commanding the reference run the following settings have to be carried
out:
-
set the maximum torque (attr. 20) and the maximum start-up torque (attr. 24)
to max. 10% of the nominal torque
-
set the maximum holding torque (attr. 43) and the maximum holding torque at
end of run (attr. 153) to 0
-
set the rpm limit for aborting run (attr. 26) to 60
-
set the time elapsed until speed falls below rpm limit for aborting run (attr. 27)
to 100
(The span of time in which the drive trys to get over the block, decreases:
With the reduced values the positioning will be aborted if the speed stays
below 60% of the target speed for longer than 100ms. By default, these
values are 30% and 200ms.)
-
set the corresponding upper and lower limit (attr. 22 or 23) in a way that the
block location lays considerable within the area between the upper and lower
limit
(Otherwise there’s the danger that the block is located within the positioning
window and consequently won’t be recognized.)
-
Where appropriate, reduce the target speed for manual run (attr. 19).
2) Now start the reference run as manual run (set bit 0 or 1 in the control word).
3) Wait for the drive moving (bit 6 in the status word is set).
4) Wait for the drive has stopped and a positioning error has appeared (bit 6 in the
status word is cleared, bit 10 is set).
5) Start a manual run in the opposite direction with the same settings (move a
certain distance away from the hard stop in order the drive can move freely).
6) Only now adjust the desired settings of the adove mentioned attributes for normal
operation.
Содержание PS*3**DN series
Страница 35: ...PSx3xxDN Instruction Manual 35 ...