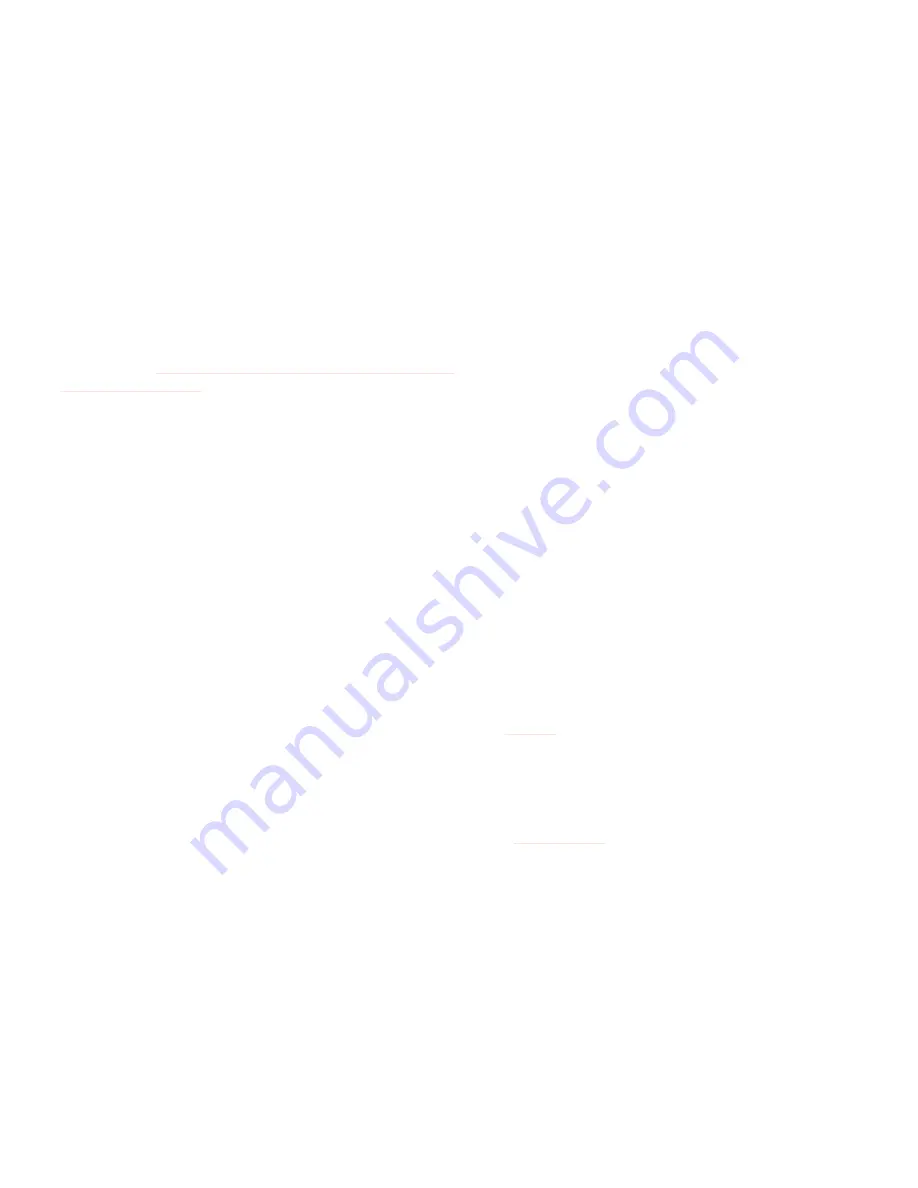
13
Control
Modbus-RTU
Modbus is an application-layer messaging protocol that formats data for communications
over serial RS-232 or RS-485. The controller/meter supports Modbus-RTU protocol, with
data transmitted through Pin 3 of the DB9 connector.
Modbus-RTU can be used to control:
•
taring
•
data collection
•
setpoint control
•
totalizer
•
batch dispensing
•
changing the gas
•
control loop adjustment.
For more information on Modbus-RTU communication commands, please see the the
Modbus FAQ at
alicat.com/using-your-alicat/faq-modbus/
and the Modbus RTU manual
at
Communicating Via Modbus-RTU
The following Modbus commands are supported:
3
Read holding register
6
Write single register
16
Write multiple registers
Use the device registers to interact with the device.
Modbus commands are written to register addresses 1001 and 1002. The command
arguments are written to 1003 and 1004. The command arguments are variables that
influence how the commands modify the device.
Analog Signals
Alternative to the digital communications described above, the device can be controlled
using analog signals transmitted through the DB9 connector (see
.
!
Warning:
Do not supply power to the device until all necessary pins have been properly
connected.
Note:
Power requirements vary based on analog configuration and valve type. Please
reference the Factory OEM Mass Flow Devices specification sheet at
alicat.com/imc
for power requirements.
The following section describes some functions that can be completed using analog signals.
Taring the Device
(METERS ONLY)
Taring gives the meter a zero reference for flow measurements, ensuring that the meter
provides the most accurate measurements. It is recommended to tare the meter:
•
After installing
•
Before every new flow measurement cycle
•
After significant changes in temperature or pressure
•
After dropping or bumping the flow controller
•
After changing the device’s orientation.