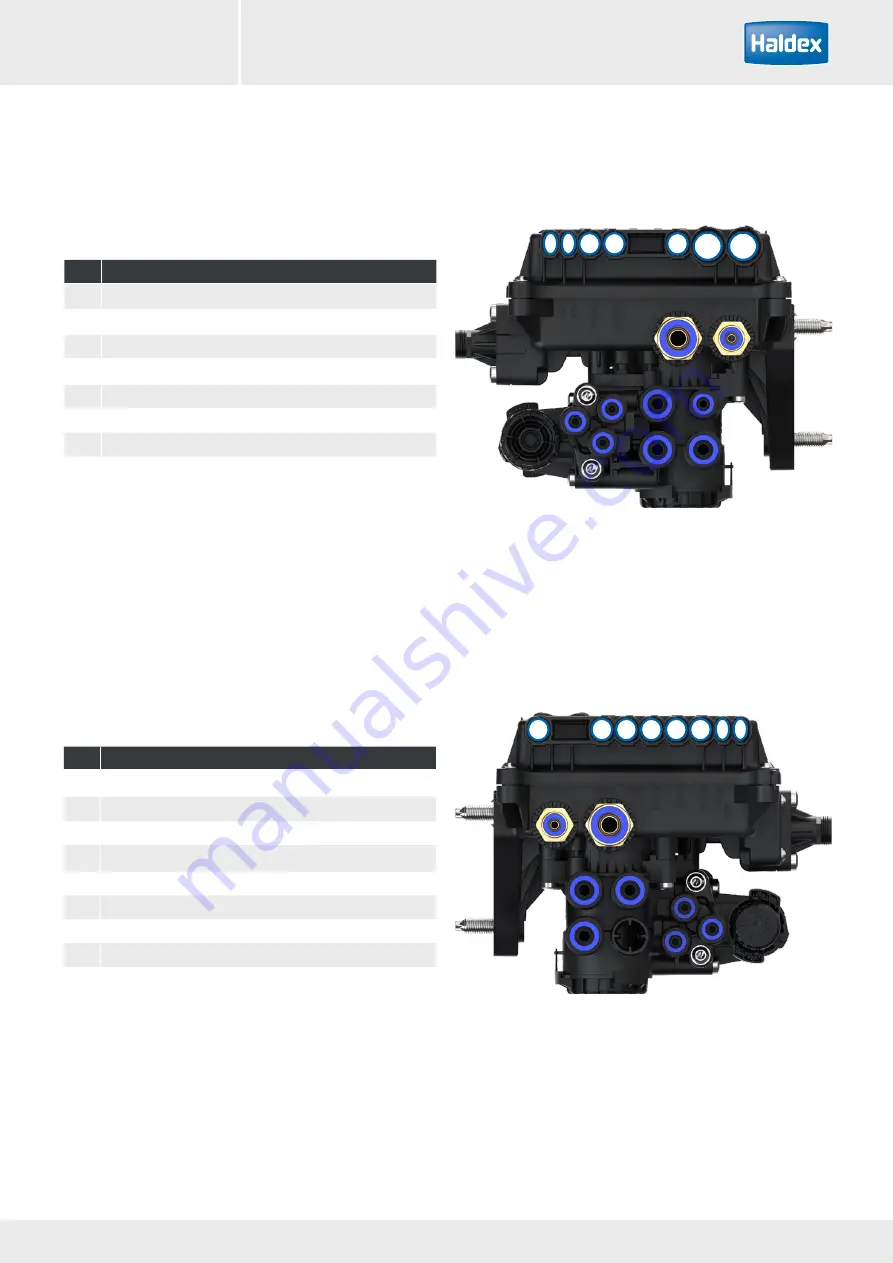
17
2022
Innovative Vehicle Solutions
DIAG++
Operator‘s Guide
DIAG++
3
12
13
11
10
9
8
2
1
4
5
6
7
14
No. Description
1
ISO 7638 PWR-A
2
ISO 12098 / PWR-B
3
S-CAN
4
H-CAN
5
T-CAN
6
Sensor S2A
7
Sensor S1A
No. Description
8
AUX 5
9
AUX 4
10
AUX 3
11
AUX 2
12
AUX 1
13
AUX 0
14
Sensor S2B
15
Sensor S1B
15
Premium 2M EBS connections
Содержание DIAG++
Страница 1: ...Innovative Vehicle Solutions OPERATOR S GUIDE ...
Страница 4: ...4 Innovative Vehicle Solutions 2016 4 Innovative Vehicle Solutions 2022 Operator s Guide DIAG ...
Страница 14: ...14 Innovative Vehicle Solutions 2016 14 Innovative Vehicle Solutions 2022 Operator s Guide DIAG ...
Страница 97: ...97 2022 Innovative Vehicle Solutions DIAG Operator s Guide DIAG Notes ...