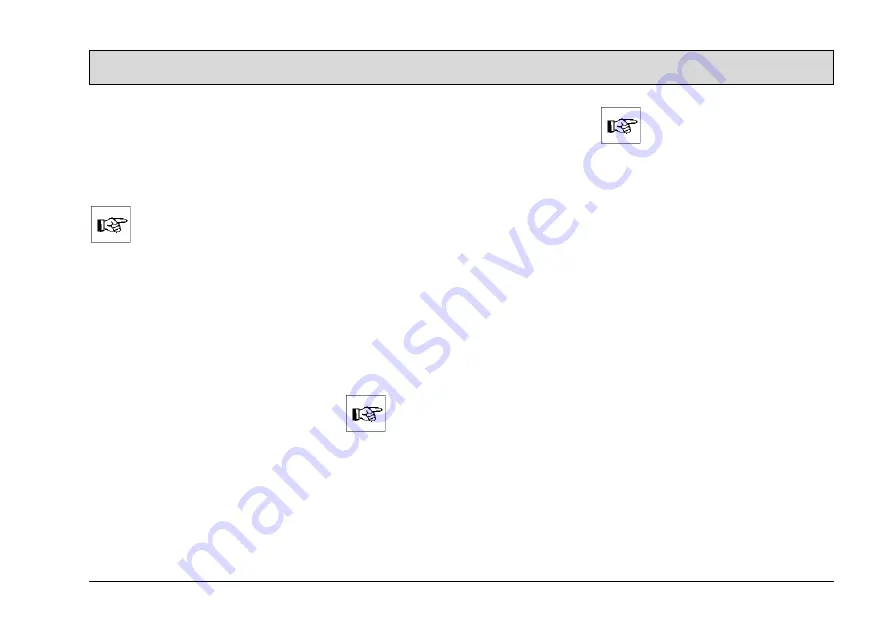
51
Safety Information
5.8.1 Cleaning the brush space
The brush space with the rotary brush
(Fig. 20/1) and seals for the dirt
hoppers (Fig. 20/7) must be checked
daily for signs of dirt and cleaned as
necessary.
Only Sweepmaster B800:
Tapes winding around the
rotary brush leads shutdown
due to overloading!
1. Remove the dirt hoppers, refer to
Section 5.9.1.
2. Check the brush space - the area
between the rotary brush, panel air
filter and dirt hoppers - for residual
waste and damage.
3. Remove any foreign bodies.
4. Clean the brush space, firstly with a
hand brush and then with water. Dry
the brush space.
5. Change defective dirt hopper seals,
refer to Section 5.9.4.
5.8.2 Changing the rotary brush
The rotary brush (Fig. 20/1) must be
checked weekly and changed in the
case of wear. A new rotary brush has a
diameter of 25 cm. When a rotary brush
has a diameter of only 20 cm, it must be
replaced with a new one.
The rotary brush (Fig. 20/1) is
comprised of four individual rotary
brush segments (Fig. 20/2) which are
fixed to the rotary brush shaft
(Fig. 20/5) by the screws (Fig. 20/4).
Pay attention that the bristle pattern on
the rotary brush (Fig. 20/1) is always
arranged in a V-shape in the direction of
driving so that the dirt is guided to the
center of the rotary brush.
1. Tip the machine to the rear.
Before tipping the
Sweepmaster B800, the
batteries must be removed,
refer to Section 5.5.4!
Before the Sweepmaster can
be tipped back, the handlebar
must be adjusted to a vertical
position.
2. First of all, disassemble the two
adjacent rotary brush segments
(Fig. 20/2): Loosen the screws
(Fig. 20/4) and remove the rotary
brush segments (Fig. 20/2).
3. Then turn the rotary brush shaft
(Fig. 20/5) 180º by hand and
disassemble the two remaining
rotary brush segments (Fig. 20/2).
4. Assemble four new rotary brush
segments (Fig. 20/2) in the reverse
sequence. When doing so, pay
attention that the rotary brush
segments (Fig. 20/2) are installed on
the guide pins (Fig. 20/6) of the
rotary brush shaft (Fig. 20/5) and
screw to facing rotary brush
segments
(Fig. 20/2) firmly to each other.
5. Tip the machine back up again.