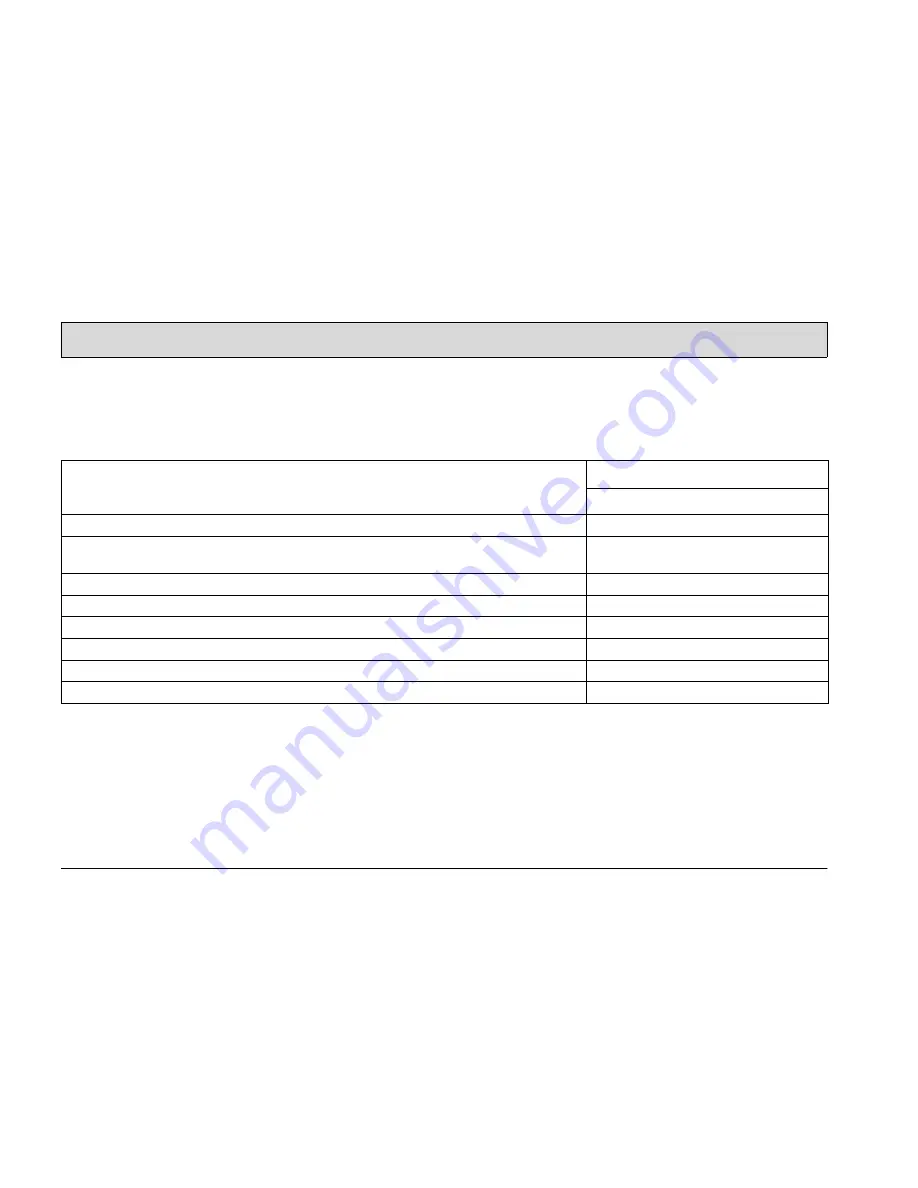
40
Maintenance and Service
Hako-System Maintenance II
The following maintenance woks are to
be performed by an authorised Hako
Service workshop.
To be performed
Interval
every 250 hours of operation
Perform maintenance works according to Hako-System Maintenance I
o
Inspect steering rollers for tread damages and bearing slackness and replace if
required
o
Check function of water pump and replace if required
o
Check drain hose of the soiled water tank and replace if required
o
Check deflector roller of the brush head and replace if required
o
Check suction hose for tight fitting and damages and replace if required
o
Check supporting wheel of the squeegee and replace if required
o
Test drive and function test
o
Содержание Hakomatic B45
Страница 1: ...Instruction Manual Hakomatic B45 7700...
Страница 58: ...58...