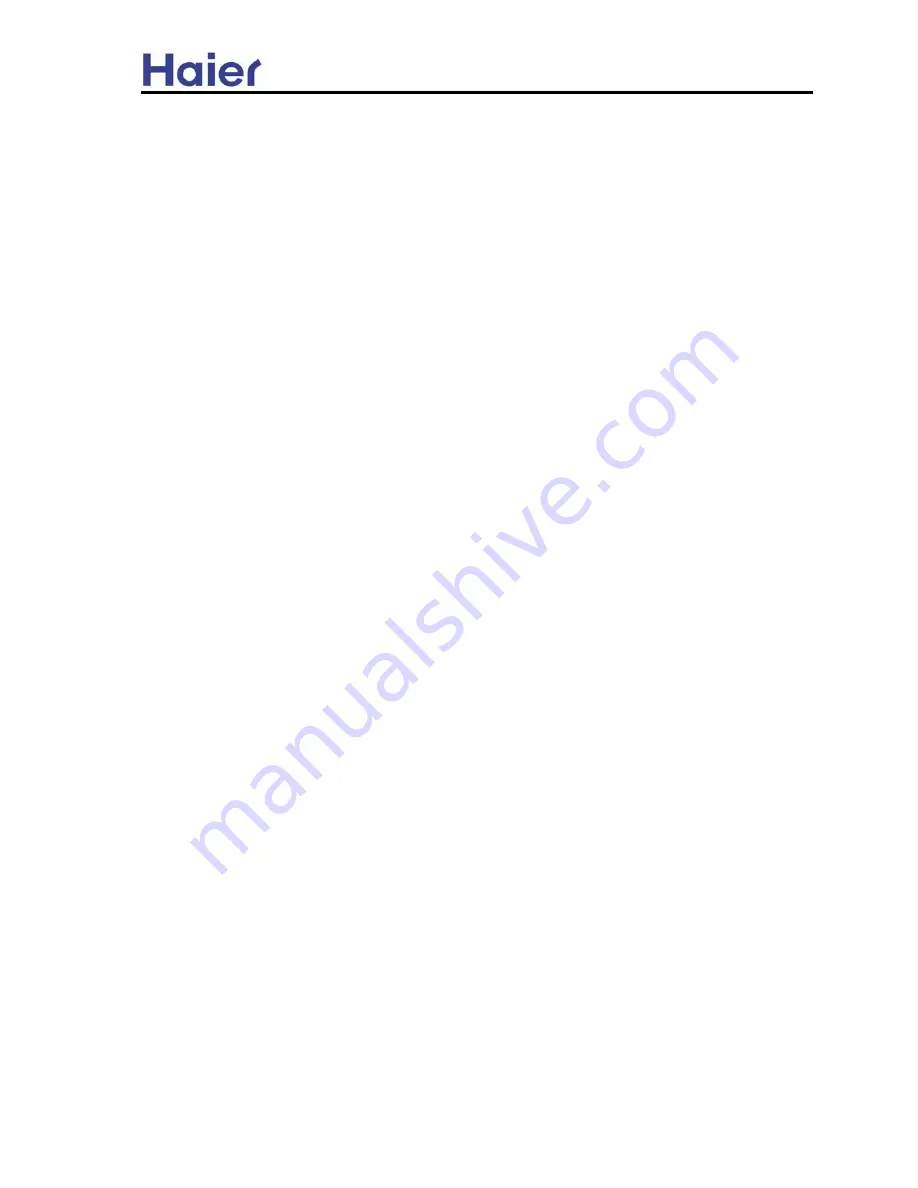
29
5.
is now the refrigerant temperature .
6.
Run the condensing fan until the leaving air temperature equals to the entering air temperature. This
Compare the observed refrigerant pressure shown on the high pressure gauge to its associated pressure
entering and leaving air temperature with accurate thermometers.
on a temperature –pressure conversion chart.
7. The refrigerant pressure should equal the chart pressure for the observed temperature.
A. The system pressure is above the chart pressure. Capital letters: Non-condensales are present
-air and/or moisture.
ACTION:
Remove and recover the refrigerant. Evacuate the system and
B. The system pressure is below the chart pressure.
C
apital letters: A mixed refrigerant is
charge with new and correct refrigerant.
and correct refrigerant.
present.
ACTION:
Remove and recover the refrigerant. Evacuate the system and charge with new
COMPRESSOR REMOVAL PROCEDURES
Use the following procedure for compressor removal ONLY after determining that the compressor has
failed.
USE THESE PROCEDURES ONLY WHEN YOU HAVE POSITIVELY DETERMINED THAT THE
COMPRSSOR HAS EXPERIENCED A MECHANICAL AND/OR ELECTRICAL FAILURE.
should wear rubber gloves and eye protection to prevent injury when testing refrigerant oil.
1. DISCONNECT THE MAIN POWER SOURCE TO THE UNIT AND LOCK THE DISCONNECT
2.
3.
Disconnect the electrical wiring at the compressor identifying each wire and its location.
SWITCH IN THE OPEN POSITION.
Remove the refrigerant charge from the entire system using proper recovery procedures.
CAUTION: After a seveer motor burn-out the products of the burn-out may be acidic. The technician
4. Remove the failed compressor.
A. Unsolder the suction and discharge lines at the compressor stubs.
B. Remove the compressor hold down bolts.
C. Place the failed compressor on a smooth surface to remove the mounting grommets and
sleeves for use with the new compressor .
D. Prevent any contamination from entering the refrigerant lines.
5. Conduct an acid test on the oil from the failed compressor .
A. Secure a generous sample of oil from the failed compressor.
B. Follow the oil test kit instructions to determine the degree of compressor burn out.
.
ƽ
As a general rule, oil with a test number less than 0.05 indicates a mild burn out.
ƽ
As a guide ,burn out classifications are as follows:
Note: Dispose of any contaminated refrigerant oil in accordance with all environmental regulations
6.
ƽ
Some oil test kits indicate severity by color change .
oil clear, no color, the compressor may have had a mechinial failure and not a burn-out.
and procedures.
oil clear, slight color, the compressor may have had a mild burn-out .
ƽ
Oil with a test number greater than 0.05 indicates a severe burn-out .
oil very dirty, strong odor test >0.05, the compressor may have had severe burn-out.
Use the following procedures with units suspected of having mild to severe burn outs.
A. After compressor removal, insert a clean, lint free swab into the system‘s suction and
discharge lines to determine the extent of contamination.
together.
D. Place the new compressor in the unit and install the mounting bolts.
C. Confirm that the new compressor has no shipping damage. The line connections must come
electrical characteristics as the original.
sealed from the factory. Verify that the replacement compressor is the same model number and
F. If any burn detected replace the liquid line filter drier with an oversized core filter drier, if the
burn was severe, and a suction line filter drier.
E. Remove the caps from the compressor stubs, clean the lines and stubs, and braze joint
B. If contamination is noted for a considerable depth, consider replacing the lines with new tubing.
Central Air Conditioner
Model: Cooling Only,
13
SEER
units