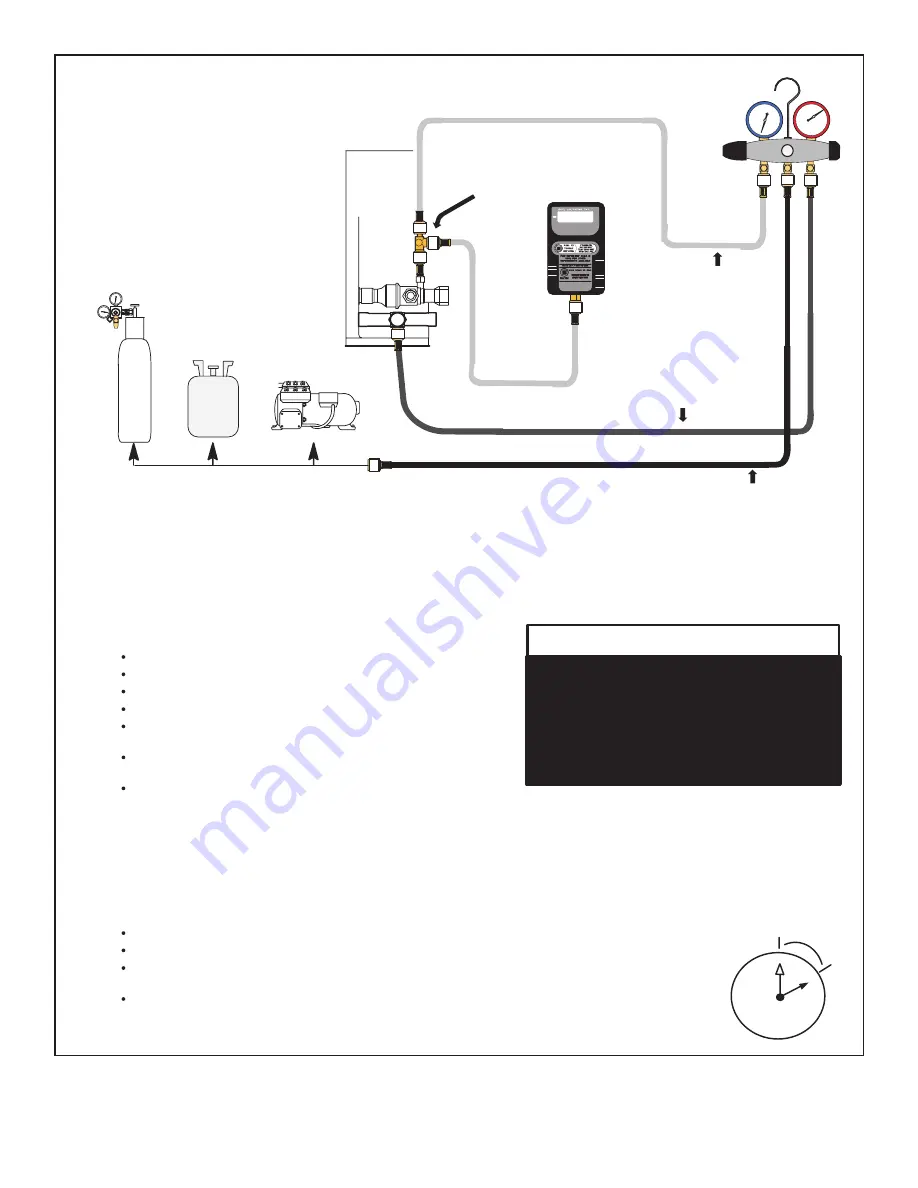
Page 17
31-5000752 Rev. 0
A -
Open both manifold valves and start the vacuum pump.
B -
NOTE - During the early stages of evacuation, it is desirable to close the manifold gauge valve at least once. A rapid rise in pressure
indicates a relatively large leak. If this occurs,
repeat the leak testing procedure.
NOTE - The term absolute pressure means the total actual pressure above absolute zero within a given volume or system. Absolute
pressure in a vacuum is equal to atmospheric pressure minus vacuum pressure.
C -
When the absolute pressure reaches 23,000 microns (29.01 inches of
mercury), perform the following:
Close manifold gauge valves.
Close valve on vacuum pump.
Turn off vacuum pump.
Disconnect manifold gauge center port hose from vacuum pump.
Attach manifold center port hose to a nitrogen cylinder with pressure
regulator set to 150 psig (1034 kPa) and purge the hose.
Open manifold gauge valves to break the vacuum in the line set and indoor
unit.
Close manifold gauge valves.
D -
Shut off the nitrogen cylinder and remove the manifold gauge hose from the cylinder. Open the manifold gauge valves to release the
nitrogen from the line set and indoor unit.
E -
Reconnect the manifold gauge to the vacuum pump, turn the pump on, and continue to evacuate the line set and indoor unit until the
absolute pressure does not rise above 500 microns (29.9 inches of mercury) within a 20-minute period after shutting off the vacuum pump
and closing the manifold gauge valves.
F -
When the absolute pressure requirement above has been met, disconnect the manifold hose from the vacuum pump and connect it to a
cylinder of HFC-410A positioned to deliver liquid refrigerant. Open the manifold gauge valve 1 to 2 psig in order to release the vacuum in the
line set and indoor unit.
G -
Perform the following:
Close manifold gauge valves.
Shut off HFC-410A cylinder.
Reinstall service valve cores by removing manifold hose from service valve. Quickly install cores with core
tool while maintaining a positive system pressure.
Replace stem caps and finger tighten them, then tighten an additional one-sixth (1/6) of a turn as illustrated.
OUTDOOR
UNIT
TO VAPOR
SERVICE VALVE
TO LIQUID LINE
SERVICE VALVE
MICRON
GAUGE
VACUUM PUMP
1/4 SAE TEE WITH SWIVEL
COUPLER
500
MANIFOLD
GAUGE SET
HFC-410A
RECOMMEND
MINIMUM 3/8” HOSE
A -
Connect low side of manifold gauge set with
1/4 SAE in-line tee to
vapor
line service valve
B -
Connect high side of manifold gauge set to
liquid
line service valve
C -
Connect available micron gauge connector
on the 1/4 SAE in-line tee.
D -
Connect the vacuum pump (with vacuum
gauge) to the center port of the manifold
gauge set. The center port line will be used
later for both the HFC-410A and nitrogen
containers.
HIGH
LOW
1
2
3
4
5
6
7
8
9
10
11 12
1/6 TURN
NITROGEN
3
CONNECT GAUGE SET
A
B
C
D
4
EVACUATE THE SYSTEM
NOTE - Remove cores from service valves (if not already done).
Possible equipment damage.
Avoid deep vacuum operation. Do not use
compressors to evacuate a system.
Extremely low vacuum can cause internal
arcing and compressor failure. Damage
caused by deep vacuum operation will
void warranty.
WARNING !
EVACUATION
H -
Open suction service valve first before liquid valve to release the unit charge into the system. Replace valve
caps and tighten (8 ft. lb.). Caps are the primary seal.
Evacuate the line set and indoor unit until a slight vacuum is indicated on the micron gauge (approximately 23,000 microns or
29.01 inches of mercury).
NOTE - Position
canister to deliver
liquid refrigerant.
Содержание GE APPLIANCES NS17HS
Страница 7: ...Page 7 31 5000752 Rev 0 Figure 1 Typical Parts Arranegment Figure 2 Typical Parts Arranegment...
Страница 29: ...Page 29 31 5000752 Rev 0 Figure 11 Typical Factory Wiring 018 through 036 models...
Страница 30: ...Page 30 31 5000752 Rev 0 Figure 12 Typical Factory Wiring 042 through 060 models...
Страница 31: ...Page 31 31 5000752 Rev 0 Figure 13 Wiring Diagram 018 036 Models...
Страница 32: ...Page 32 31 5000752 Rev 0 Figure 14 Wiring Diagram 042 060 Models...
Страница 43: ...Page 43 31 5000752 Rev 0 Notes...