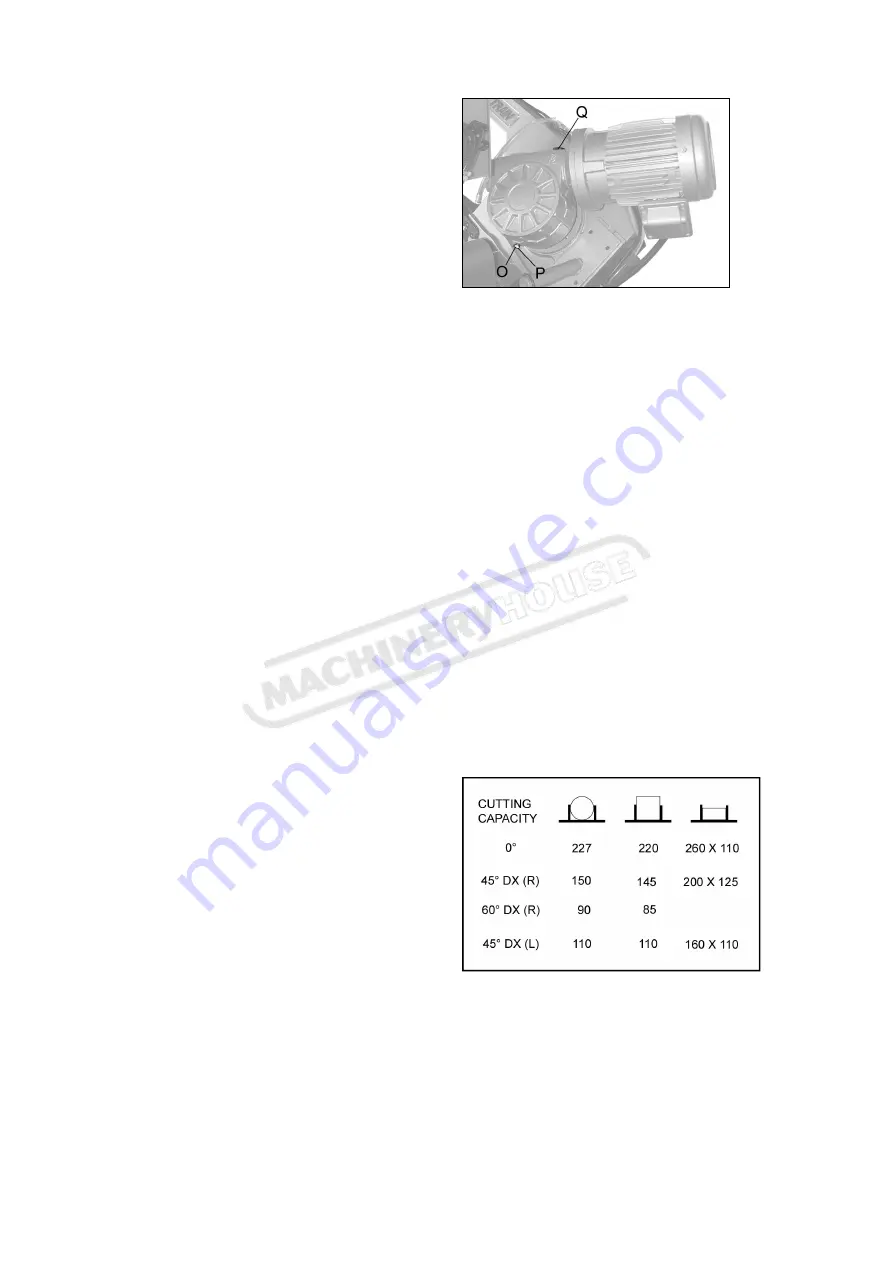
- 9 -
6.1 Daily maintenance
- General cleaning of the machine to remove
accumulated shavings.
- Clean the lubricating coolant drain hole to avoid
excess fluid.
- Top off the level of lubricating coolant.
- Check blade for wear.
- Rise of saw frame to top position and partial
slackening of the blade to avoid useless yield stress.
- Check functionality of the shields and emergency
stops.
6.2 Weekly maintenance
- Thorough cleaning of the machine to remove
shavings, especially from the lubricant fluid tank.
- Removal of pump from its housing, cleaning of the
suction filter and suction zone.
- Clean the filter of the pump suction head and the
suction area.
- Use compressed air to clean the blade guides (guide
bearings and drain hole of the lubricating cooling).
- Cleaning flywheel housings and blade sliding
surfaces on flywheels.
6.3 Monthly maintenance
- Check the tightening of the motor flywheel screws.
- Check that the blade guide bearings on the heads are
perfect running condition.
- Check the tightening of the screws
of the gear motor,
pump, and accident protection guarding.
6.4 Six-monthly maintenance
- Continuity
test
of
the
equipotential
protection
circuit.
6.5 Maintenance of other machine parts
The
worm
drive
gearbox mounted
on
the
machine
is
maintenance-free
guaranteed
by
its
manufacture.
6.6 Oils for lubricating coolant
Considering the vast range of products on the market,
the user can choose the one most suited to their own
requirements, using as reference the type SHELL
LUTEM OIL ECO. THE MINIMUM PERCENTAGE
OF OIL DILUTED IN
WATER IS 8 - 10 %.
6.7 Oil disposal
The
disposal
of
these
products
is
controlled
by
strict
regulations.
Please
see
the
Chapter
on
"Machine
dimensions Transport - Installation"
in
the
section
on
Dismantling.
6.8 The gear box
The gear box requires periodic changing of oil. The
oil must be changed by the first 6 months of a new
machine and every year thereafter.
To change the gear box oil
- Disconnect the machine from the power source.
- Raise the saw arm to vertical position.
- Release the drain hold (O) to draw off gear oil by
loosening the hex socket screw (P).
- Replace the screw (P) after oil completely flows off.
- Place the saw arm back to horizontal position.
- Fill Gear box with approximately .3 liter of gear oil
through the hole of the vent screw (Q)
For reference, use SHELL type gear oil or Mobile gear
oil #90.
6.9 Special maintenance
Special
maintenance
must
be
conducted
by
skilled
personnel.
We
advise
contacting your nearest dealer
and/or
importer.
Also
the
reset
of
protective
and
safety
equipment
and
devices (of
the
reducer), the
motor,
the
motor pump,
and
other
electrical
components
requires
special maintenance.
7
TECHNICAL CHARACTERISTICS
7.1 Table of cutting capacity and technical details
10
Instruction Manual for EB-270DSA (B066)
31/03/2016
Содержание EB-270DSA
Страница 14: ... 13 10 WIRING DIAGRAMS 14 Instruction Manual for EB 270DSA B066 31 03 2016 ...
Страница 15: ... 14 15 Instruction Manual for EB 270DSA B066 31 03 2016 ...
Страница 25: ... 24 25 Instruction Manual for EB 270DSA B066 31 03 2016 ...
Страница 26: ... 25 26 Instruction Manual for EB 270DSA B066 31 03 2016 ...
Страница 27: ... 26 27 Instruction Manual for EB 270DSA B066 31 03 2016 ...
Страница 28: ... 27 28 Instruction Manual for EB 270DSA B066 31 03 2016 ...
Страница 29: ... 28 29 Instruction Manual for EB 270DSA B066 31 03 2016 ...