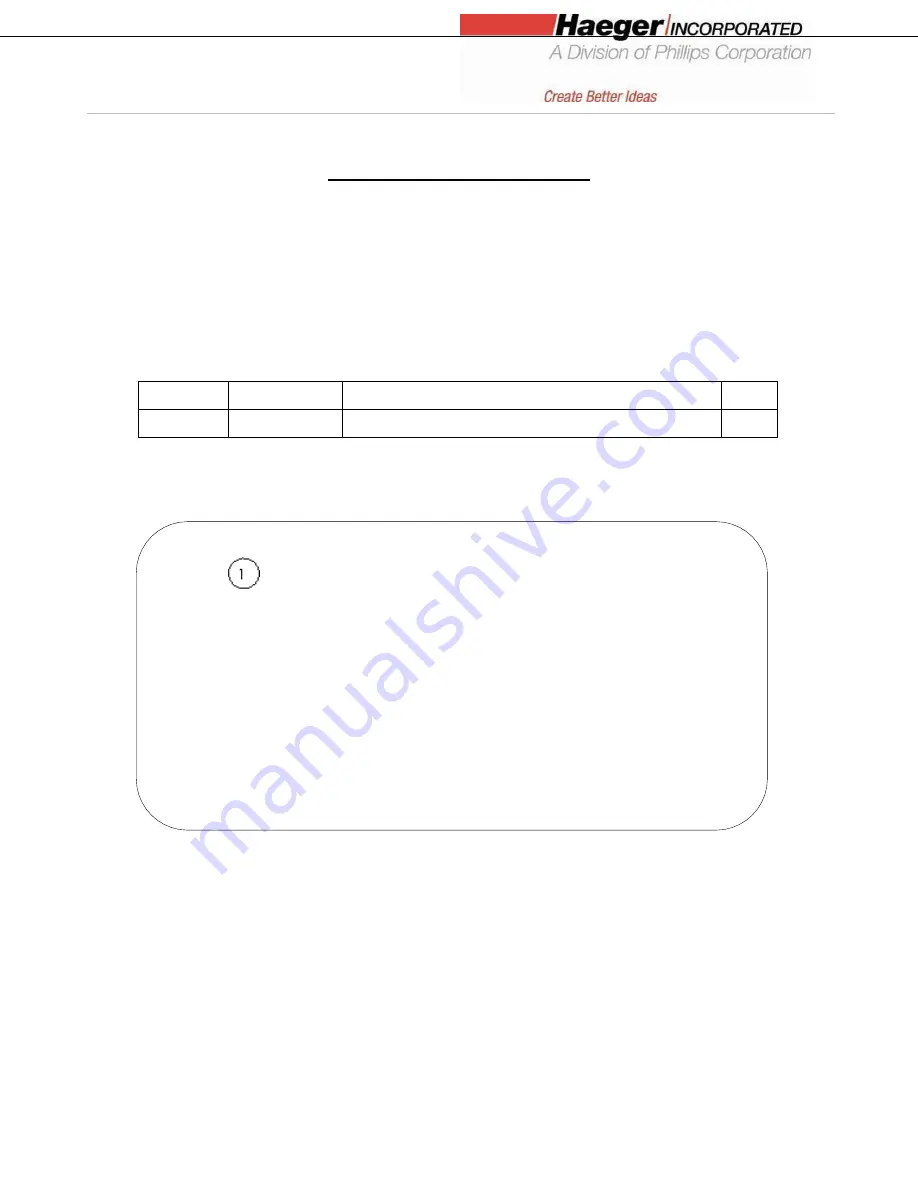
61
SECTION 7 – PARTS LIST
Description
The
Parts
in this section of the manual are listed by
Item Number
,
Part Number
,
Description
and
Quantity
.
ITEM NO.
PART NUMBER
DESCRIPTION
QTY.
1
XX-XXXXX
XXXXXXXXXX
X
Item Numbers
:
Are depicted with in a circle with an arrow pointing to the specific
part
or
assembly
.
Part Number:
This is the most important number on the page. It identifies a specific item in Haeger’s
inventory. To avoid delays when ordering parts, be very sure the
Part Number
and
Quantity
are stated
correctly!
Description:
This is Haeger’s brief description of the part. For purchased parts, it may also include the
manufacturer and their part number.
Quantity:
This represents the total quantity of the particular
Part
which is used in the complete assembly.
When ordering
Parts
, it may not always be necessary to order the number of parts listed. Order only the
quantity that is required to make the repairs.
Содержание 618 MSPe
Страница 1: ...618 MSPe Operation Manual ...
Страница 66: ...62 Main Assembly ...
Страница 69: ...65 Sheet Metal ...
Страница 72: ...68 Dual Safety Sensor Assembly ...
Страница 78: ...74 Electrical Cabinet ...
Страница 81: ...77 Hydraulic Reservoir Assembly ...
Страница 83: ...79 Hydraulic Manifold Subassembly ...
Страница 87: ...83 MAS 9 Autofeed Optional ...
Страница 89: ...85 MAS 350 Autofeed Optional ...