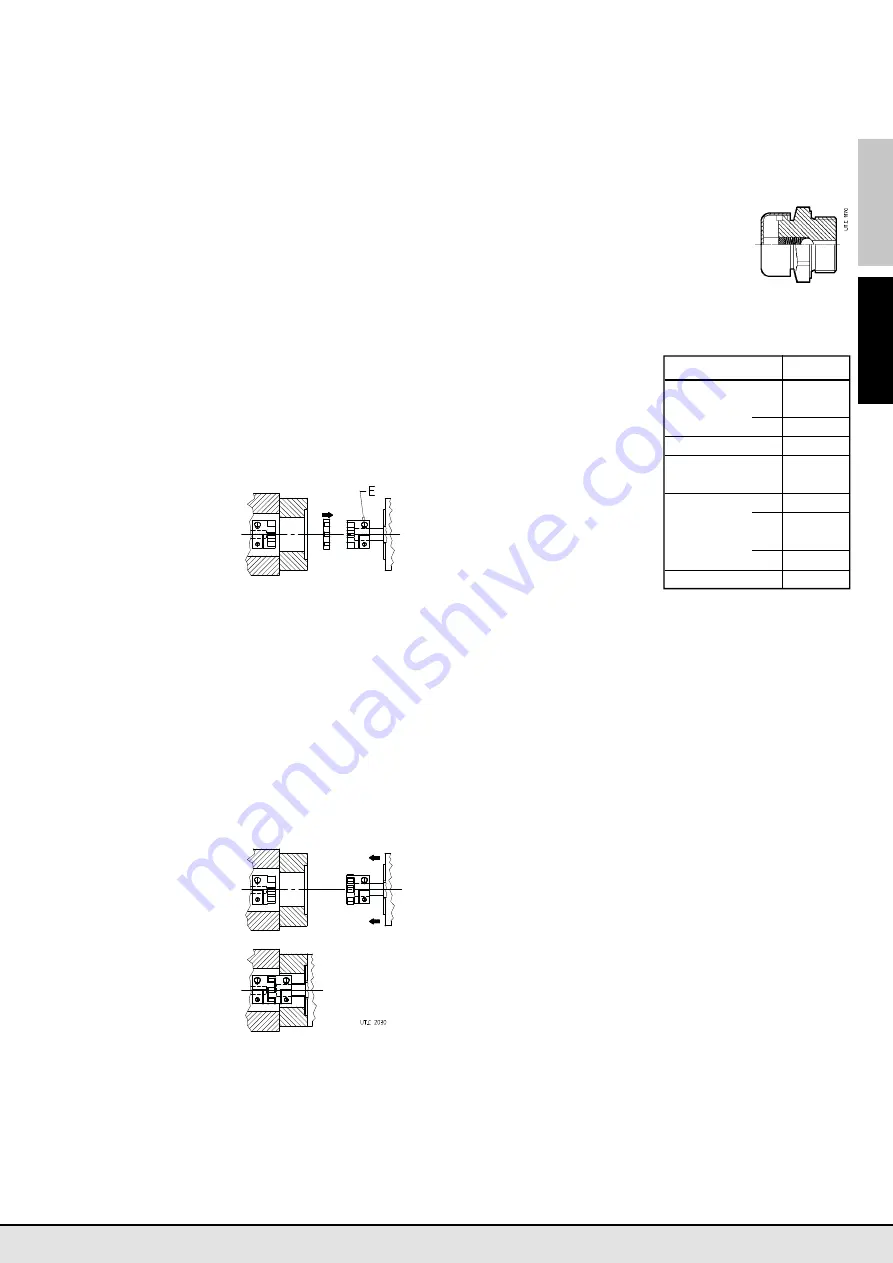
23
Rossi
Operating instructions − UTD.045.06-2013.00_TR_EN
TR
EN
of the parallel key is to be at least 0,9 times the pinion face width;
– mount onto the servo motor shaft end, in the following order:
– the
spacer
pre-heated at
65 °C
treating the relevant motor shaft
area with
adhesive type LOXEAL 58-14
and checking that
between keyway and motor shaft shoulder there is a cylindrical
part ground by 1,5 mm at least; pay attention not
to damage the
external surface
of spacer;
– the
key
in the keyway, making sure that a contact length of at
least 0,9 times the pinion width is present;
– the
pinion
pre-heated at
80 ÷ 100 °C
;
– the
axial fastening system
when foreseen (self locking screw
on motor shaft butt-end with washer and spacer or hub clamp
with 1 or more dowels, fig. a); for the cases foreseen
without
axial fastening
(fig. b), apply adhesive type
LOXEAL 58-14
also on the motor shaft part laying under the
pinion
;
– in case of axial fastening system with hub clamp and dowels,
make sure that they do not overhung from spacer external surface:
screw the dowels completely and, if necessary, imprint the motor
shaft with a point;
– grease (with grease type KLÜBER Petamo GHY 133N) the pinion
teeth, the seal ring rotary seating and the ring itself, and assemble
carefully,
paying particular attention not to damage the seal
ring lip due to an accidental impact with the pinion toothing
.
Servo gear reducer type R
(servo motor coupling with bell and torsionally stiff coupling)
–
Worm servo gear reducer R V, R IV
–
Helical servo gear reducer R 2I, R 3I
–
Bevel-helical servo gear reducer R CI, R ICI
The servo gear reducer
type R input face has
a flange (
bolts not
included
) for servo
motor mounting and a
torsionally stiff coupling.
A half-coupling hub is to
be fitted onto the servo
motor keyless shaft end (if present, remove it; see fig. 1). In case of
high starts/hour and heavy loads, it is necessary to request the non-
standard design
«Coupling with keyway»
.
All mounting surfaces (shafts, bores, keys and keyways), must be
clean and free of burrs, nicks and dents.
Check the servo motor shaft diameter, coupling bore diameter, key
and keyway dimensions and tolerances.
All coupling bores are machined to tolerance H7
.
Assembling clearance between the servo motor shaft diameter and
half-coupling hub diameter has to be maintained within 0,01 and
0,05 mm.
A light coating of oil is recommended to ease the mounting process
and will not affect the clamping force of the hub.
Do not use molybdenum disulphide or equivalent lubricants.
Insert the half-coupling onto the servo motor shaft, as shown
in fig. 1, abutting with elastomer ring seat
.
Tighten the clamp
screw
E
, using a
dynamometric wrench,
to the appropriate
torque stated in the
table
1)
(see page 24).
Clean the elastomer
ring and the seats into
the coupling hubs
and apply a light film
of oil to facilitate the
assembly process, see
fig. 2 (use polyurethane
compatible lubricants
such as e.g. vaseline).
Insert the elastomer ring
(fig. 2) and assemble the
servo motor on the servo gear reducer, tightening the screws (fig. 3)
on the servo motor flange.
The achievement of the zero angular backlash is ensured by
the squeezing of the elastomer ring interposed between the
two parts of the coupling
.
1) In some cases, a spacer to be interposed between the half-coupling and the servo
motor shaft shoulder is provided
9.6 - Bearings
Since there are many different types of bearings in a gear reducer
(roller, tapered roller, straight roller, etc.) and each bearing works
fi g. 1
fi g. 2
fi g. 3
with different loads and speeds depending on the input speed, the
nature of the load of the driven machine, the transmission ratio,
etc., and with different lubricants (oil bath, oil splash, grease, oil
circulation, etc.), it is not possible to define any periodical mainte-
nance and replacement of bearings in advance.
If a precautionally maintenance is required,
undertake periodical
checks to verify noise level and vibration with the help of
appropiate diagniostic equipment and instruments
. If the
measured values worsen even slightly it is necessary to stop gear
reducer or gear motor and after having inspected inside the unit
replace the bearings which are subject to breakdown.
9.7 - Metal filler plug with filter and valve
When the gear reducer or gearmotor (size ≥ 100)
is equipped with metal filler plug with filter and
valve (see fig. beside), in order to clean it, it is
necessary to unscrew it from the gear reducer
(preventing any debris or other foreign items
from entering the reducer, disassemble the
cover, wash it with solvent, dry with compressed
air and reassemble it).
This operation is to be made according to environment conditions.
10 - Sound levels
Most of the Rossi product
range is cha
racterised
by
sound pressure levels L¯
pA
(mean value of mea-surement,
assuming nominal load and
input speed
n
1
= 1 400 min
-1
,
at 1 m from external profile of
gear reducer standing in free
field on a reflecting surface,
according to draft proposal
ISO/CD 8579)
lower or equal
to 85 dB(A).
The table indicates the pro-
ducts which
can exceed
a.m.
threshold. For further informa-
tion about sound levels of every
single product see Rossi tech-
nical catalogs.
Machine/Train of gears
i
N
Size
Helical
R I
<
3,15
>
160
>
4
>
200
R 2I
all
>
320
R 3I
all
>
400
R 4I
<
160
>
500
>
200
>
630
Bevel helical
R CI
all
>
320
R C2I <
63
>
400
>
71
>
500
R C3I
all
>
630
Bevel helical
R C
1
>
250