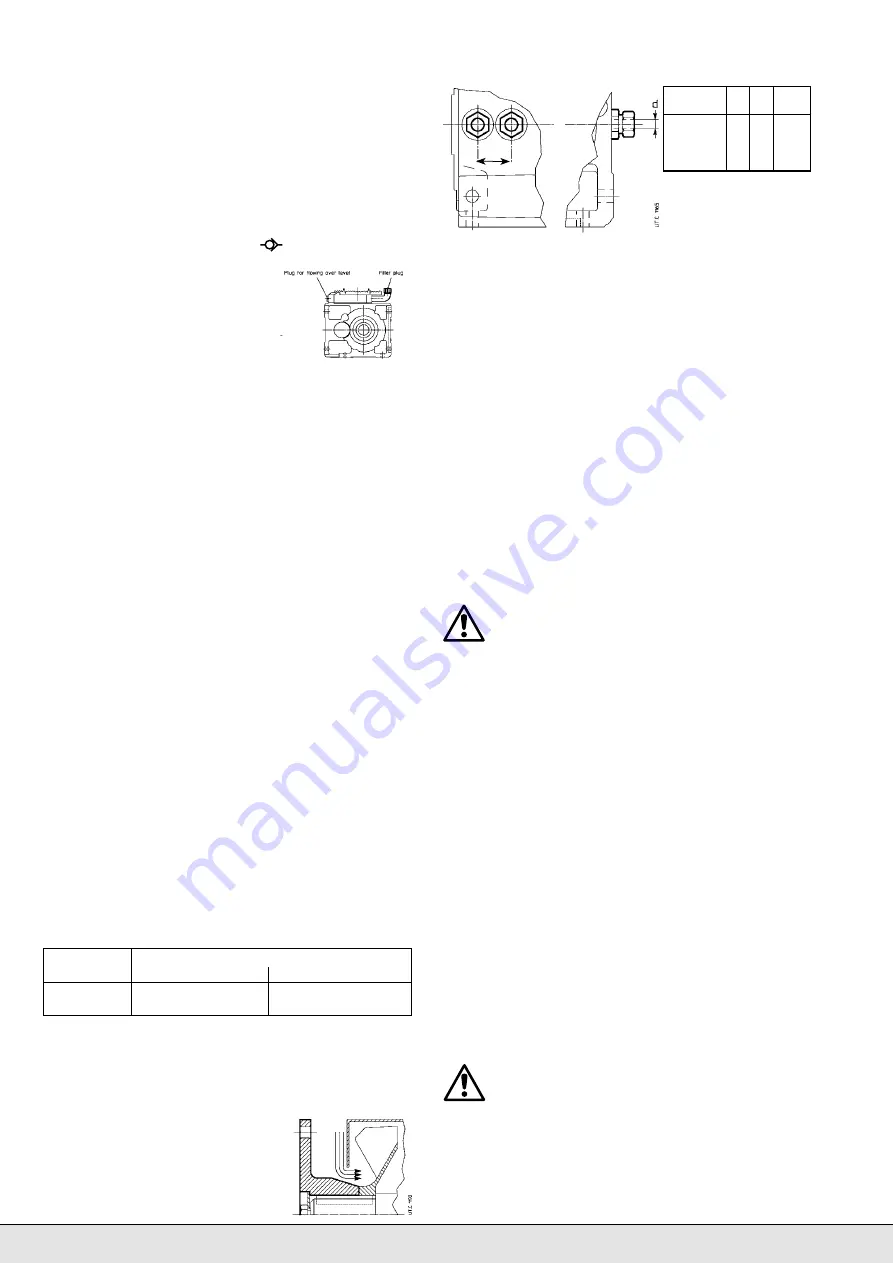
16
ROSSI
GEARMOTORS
UT.D 045 rev. 5
6 - Lubrication
6.1 - General
Depending on type and size, gear reducers and gearmotors may be
grease-lubricated and supplied FILLED WITH GREASE, or (synthetic
or mineral) oil-lubricated and supplied FlLLED WlTH OlL or WlTHOUT
OIL depending on type and size (see ch. 6.2). When supplying
WITHOUT OIL, the filling up to specified level (normally stated by
means of transparent level plug) is Buyer’s responsibility.
Every gear reducer has a
lubrication plate.
Concerning lubricant type and quantity, gear reducer type, how sup-
plied, plugs, filling instructions, oil-change interval, etc. see lubrica-
tion table (6.2).
Be sure that for gear reducers and gearmotors size
100, the filler
plug is provided with a valve (symbol
); otherwise, replace it
with the one normally supplied with.
When gear reducer or gearmotor is provi-
ded with a
spilway plug
(red colour) fill
after unscrewing a.m. plug in order to
check the obtained level by oil outlet.
When gear reducer or gearmotor is provi-
ded with a
level plug with rod
, fill with oil
up to specified level on rod.
When gear reducer or gearmotor is supplied with a level plug (size
100), the necessary lubricant quantity is that which
reaches a.m.
Ievel in center line of plug (gear reducer at rest)
and not the
approximate quantity given on the catalogue.
Usually bearings are automatically and continuously lubricated
(bathed, splashed, through pipes or by a pump) utilising the main
gear reducer lubricant. The same applies for backstop devices, when
fitted to gear reducers.
In certain gear reducers in vertical mounting positions V1, V3, V5 and
V6, and right-angle shaft gear reducers in horizontal positions B3, B6
and B51 (though not gearmotors in this case, for which the above
indications hold good) upper bearings are independently lubricated
with a special grease «for life», assuming pollution-free surroun-
dings. The same applies for motor bearings (except some cases in
which relubrication device is adopted) and backstop devices when
fitted to motors.
Always be sure that the gear reducer is located as per the mounting
position ordered, which appears on the name plate. When no indica-
tion is given, the gear reducer may be used in horizontal mounting
position B3 or B5 (B3, B8, worm gear reducers size
64), or vertical
position V1 (in the case of right angle shaft gear reducers in the
design incorporating flange FO1...).
Combined gear reducer units.
Lubrication remains independent,
thus data relative to each single gear reducer hold good.
6.3 - Extruder support lubrication (parallel
and
right angle
shaft)
The lubrication
of
extruder support
is
separate
from the gear redu-
cer, except:
– for designs HA ... HC;
– in presence of the independent cooling unit, if applied to lubricate
both the gear reducer and the support.
The
separate lubrication
of extruder support sensibly improves the
reliability and real life of the axial bearing; the separation between
gear reducer and support is granted by a seal ring.
With separate lubrication, for the extruder support, use polyalphao-
lephines based synthetic oil (MOBIL SHC XMP 680, CASTROL Tribol
1510/680) with
ISO 680 cSt
viscosity grade.
With
common
lubrication
(designs HA ... HC in presence of inde-
pendent cooling unit, if applied to lubricate both the gear reducer
and the support), lubricant ISO viscosity grade must be according to
the instructions given in ch. 6.2 «lubrication table» and oil must be
polyalphaolephine based synthetic type.
For the filling up of oil of extruder support, see the table below.
For the lubrication of gear reducer refer to ch. 6.2, lubrication table.
7 - Cooling system
7.1 - Cooling by fan
If there is fan on the gear reducer verify
that there is sufficient space allowing for
adequate circulation of cooling air also
after fitting coupling protection. If a cou-
pling protection is fitted (drilled case or
wire netting), smooth, the coupling hub, if
necessary.
7.2 - Water cooling by coil
The presence of coil is given by water inlets (pipes DIN 2353) protru-
ding from the casing as shown in the following figure.
Attention:
Do not tamper with the eventual stop plate in order to keep
the pipes them locked; in particular keep the pipe locked while tighte-
ning the nut of connection pipe. Water fed into the system must:
– be not too hard;
– be at max tempe20 °C;
– flow at 10
20 dm
3
/min;
– have a pressure 0,2
0,4 MPa (2
4 bar).
Where ambient temperature may be less than 0 °C, make provision
for water drain and compressed air inlet, so as to be able to empty
out the coil completely and avoid freezing up.
When risking high input pressure peaks, install a safety valve set to
a proper operating threshold.
7.3 - Independent cooling unit
See specific documentation supplied together with the unit.
8 - Commissioning
Carry out an overall check, making particularly sure that the gear
reducer is filled with lubricant.
Where star-delta starting is being used, input voltage must match
the motor lower voltage (
connection).
For asynchronous three-phase motor, if the direction of rotation is
not as desired, invert two phases at the terminals.
Before running gear reducers fitted with
backstop device
, make
sure that the
direction of rotation in machine, gear reducer and
motor all correspond correctly.
Attention!
One or more startings in the false direction,
even if short, could irremediably damage the backstop
device, the coupling seats and/or the electric motor.
A
running-in
period is advisable:
– of approx. 400
1 600 h for gear reducers with worm gear pairs
in order to reach maximum efficiency;
– of approx. 200
400 h for gear reducers with bevel and/or cylin-
drical gear pairs in order to reach maximum functionality.
The temperature of both gear reducer and lubricant may well rise
beyond normal values during running-in. After the running-in period it
may be necessary to verify the gear reducer fastening bolt tightness.
Note: worm gear reducer efficiency is lower in the
first running
hours
(about 50) and at every cold starting (efficiency will be better
with oil temperature increasing). For further information consult
ROSSI MOTORIDUTTORI technical catalogues.
9 - Maintenance
9.1 - General
At machine rest, verify at regular intervals (more or less frequently
according to environment and use):
a) all external surfaces are clean and air passages to the gear redu-
cer or gearmotors are free, in order that cooling remains fully
effective;
b) oil level and deterioration degree (check with cold gear reducer at
rest);
c) the correct fastening screws tightening.
During the operation check:
– noise level;
– vibrations;
– seals;
– etc.
Attention!
After a running period, gear reducer (excluding
the shaft mounted gear reducers) is subject to a light inter-
nal overpressure which may cause burning liquid dischar-
ge. Therefore, before loosening whichever plug wait until
gear reducer has become cold; if not possible, take the necessary
protection measures against burning due to warm oil contact. ln all
cases, always proceed with great care.
Maximum oil temperatures indicated in lubrication table (see ch.6.2)
do not represent a hindrance to the gear reducer regular running.
During the oil change, after having unscrewed also the filler plug in
order to improve the discharge, it is recommended to clean inter-
nally the gear reducer casing using the same oil type suitable for the
air
U
T.C
764
Size
d A
1)
spanner
Ø
≈
125 ... 180 12
1
40 22
200 ... 280 12
1
50 22
320 ... 360 16
1
60 30
400 ... 631 16 200 30
A
1) These values for some mounting
positions and designs can vary.
Gear reducer
Lubrication of extruder support
size
Separate lubrication
1)
Joint lubrication
2)
125 ... 451
Filling up
Filling up
to the level (of support) to the level (of gear reducer)
1) Support with metal filler plug with filter and valve, level and draining plug.
2) The level is metal only in the gear reducer casing.