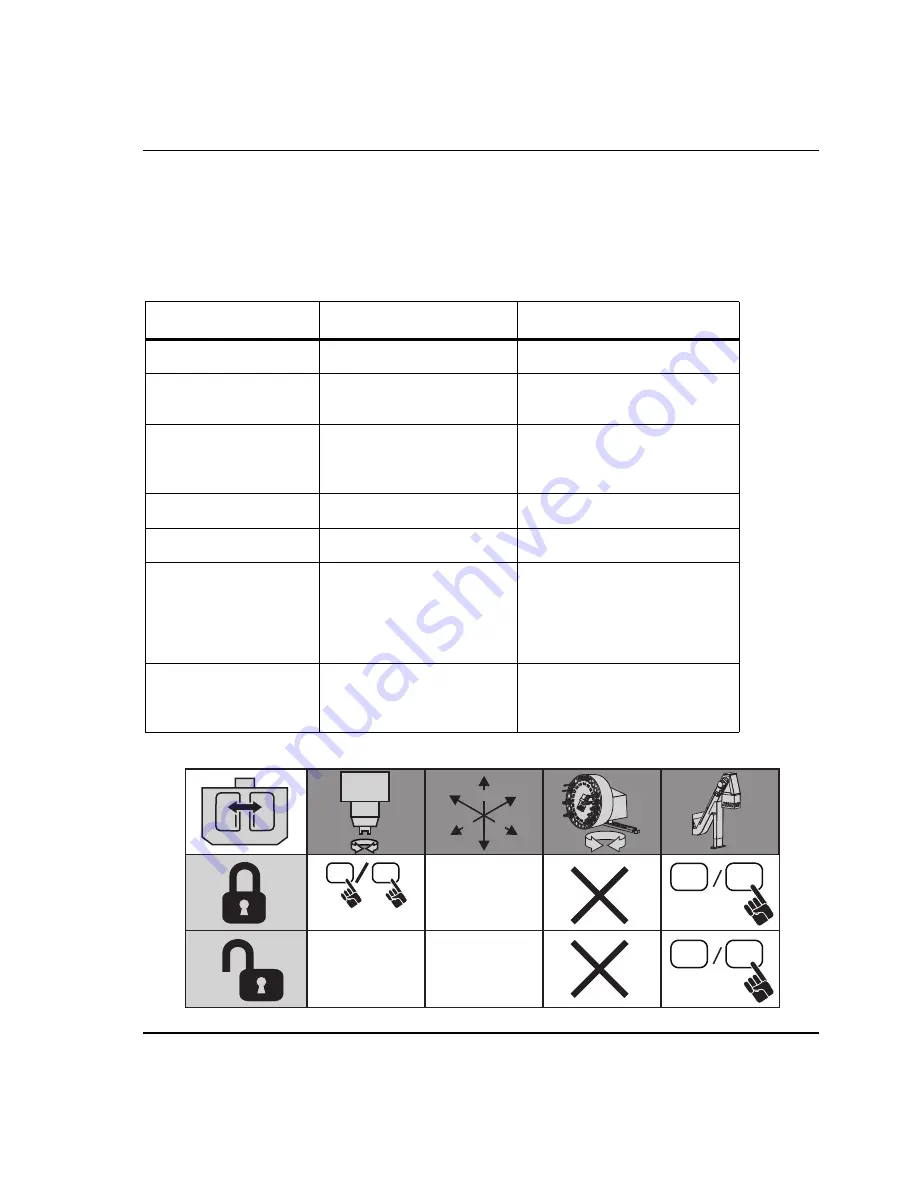
Safety
9
1.3.1
Machine Behavior with the Door Open
For safety, machine operations stop when the door is open and the setup keyswitch is
locked. The unlocked position allows limited machine functions with the door open.
T1.2:
Setup / Run Mode Limited Overrides with the Machine Doors Open
Machine Function
Keyswitch Locked
Keyswitch Unlocked
Maximum Rapid
Not allowed.
Not allowed.
Cycle Start
Not allowed. No machine
motion or program execution.
Not allowed. No machine motion
or program execution.
Spindle
[CW]
/
[CCW]
Allowed, but you must press
and hold
[CW]
or
[CCW]
.
Maximum 750 RPM.
Allowed, but maximum 750 RPM.
Tool Change
Not allowed.
Not allowed.
Next Tool
Not allowed.
Not allowed.
Opening the doors while a
program runs
Not allowed. The door is
locked.
Allowed, but axis motion stops
and the spindle slows to a
maximum of 750 RPM. The doors
lock during tool changes and
some canned cycles.
Conveyor motion
Allowed, but you must press
and hold
[CHIP REV]
to run
in reverse.
Allowed, but you must press and
hold
[CHIP REV]
to run in
reverse.
CW
CCW
750 RPM Max.
750
RPM Max.
0%
0%
CHIP
FWD
CHIP
REV
CHIP
FWD
CHIP
REV
Y
X
Z
G00
G01
Содержание UMC-750
Страница 2: ......
Страница 10: ...viii ...
Страница 35: ...Introduction 19 F2 3 This diagram illustrates the 5 axes available on the UMC 750P A B B 45 45 ...
Страница 40: ...UMC 750P Specifications 24 ...
Страница 44: ...Coolant Tank Clean Out 28 ...
Страница 48: ...Machine Rotary Zero Point MRZP Offsets 32 ...
Страница 66: ...247 Simultaneous XYZ Motion in Tool Change 50 ...
Страница 72: ...56 ...