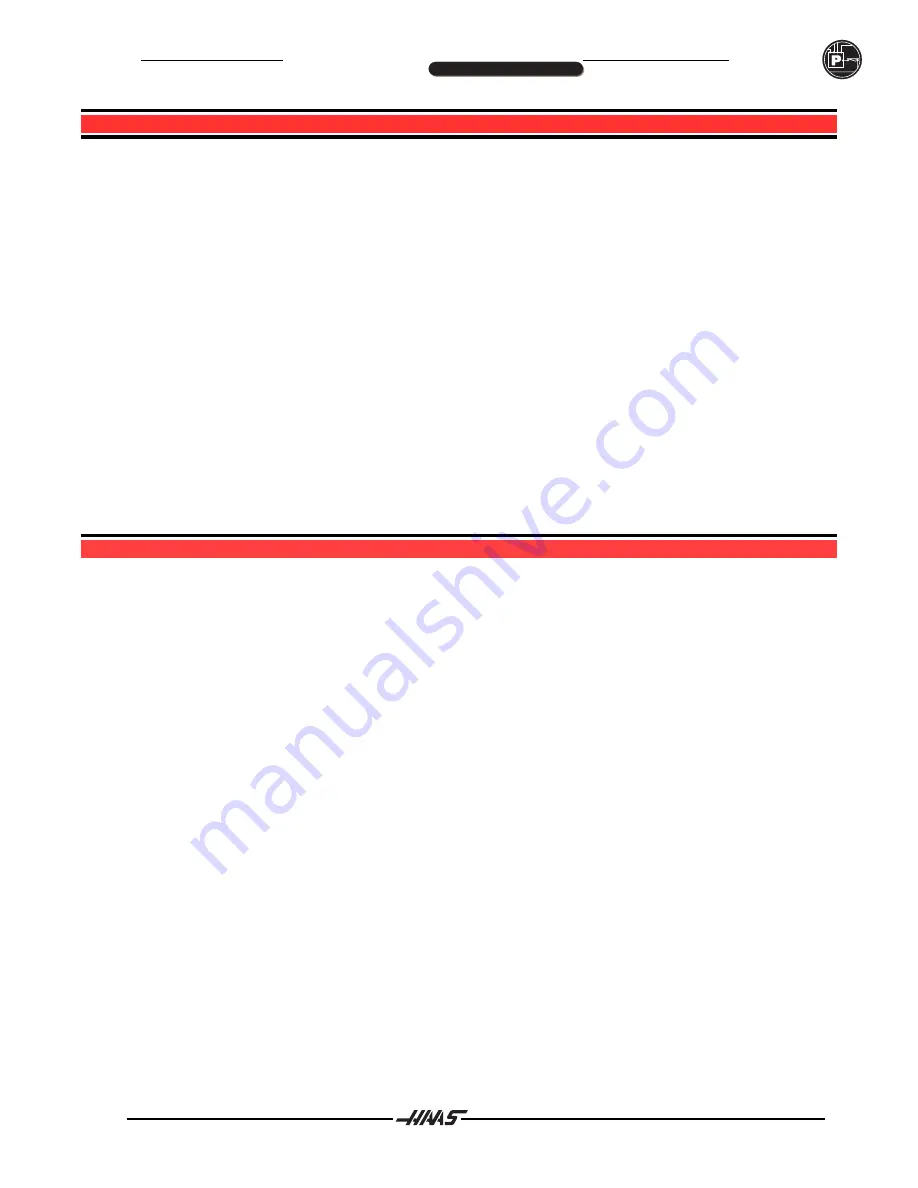
55
TRT
TILTING ROTARY
TABLE
TRT
O
M
PERATOR’S
ANUAL
TILTING ROTARY
TABLE
96-5048 rev E
June 2002
7. PROGRAMMABLE PARAMETERS
There are 38 stored parameters associated with each servo axis. There is a battery in the controller which will
keep the parameters (and the stored program) saved for up to eight years. These parameters are used to
change the way the controller and servo loop operate. To change a parameter, go to the PROGRAM mode by
pressing the MODE button if not already in PROGRAM mode. Then press the
up
arrow and hold it at step 1 for
three seconds. After three seconds, the display will change to the parameter entry mode. The display will
indicate:
01 PP n
where
n
is the value of Parameter 1. Parameters are one to five digits in length and are decimal integers. If
changing parameters associated with the servo loop, it is safest to do this with the servo loop off. Turn the
servo loop off by pressing EMERGENCY STOP. To exit from parameter entry mode, either press the MODE
button to go to RUN mode or push the down arrow key until you return to step 1.
The
up
arrow key is used to select the next higher numbered parameter and the
down
arrow key is used to
select the next lower numbered parameter. The
right
arrow key is used to alternate between parameters for the
A
and
B
axes. Pressing the
up
arrow,
down
arrow,
right
arrow, or MODE keys will cause an entered param-
eter to be stored.
Some of the parameters are protected from being changed by the user. This is because they could result in
unstable or unsafe servo operation. If you need to change any of these parameters, call HAAS.
7.1 G
EAR
C
OMPENSATION
The control has the ability to store a compensation table to correct for small errors in the worm gear. The gear
compensation tables are part of the parameters. While parameters are displayed, press the
right
arrow button
to select the gear compensation tables. There is a separate plus direction table from the minus direction table.
Use the
right
arrow button to display the plus or minus table. The gear compensation data is displayed as:
gP Pnnn cc
for plus table
G- Pnnn cc
for minus table
The
nnn
value is the machine position in degrees and the
cc
is the compensation value in encoder steps.
There is a table entry every two degrees starting at 001 and going to 359. If your control has non-zero values in
the gear compensation tables, it is recommended that you do not change them.
When the gear compensation tables are displayed, the
up
and
down
arrow button will select the next two
degree (2
o
) entry and the minus (-) and numeric buttons will enter a new value. In addition to this, the JOG
button may be used to adjust the compensation value. If the servo is on when changes are made, and the table
is at the position corresponding to the entry changed, the servo motor will move by the adjustment amount.
This is valuable in that the JOG button can be used to move the motor to a desired position.
Clearing of parameters will set all of the gear compensation tables to zero. To exit the gear compensation
display, press the MODE button; this returns the control to RUN mode.
When a table is using gear compensation, the values in Parameter 11, for the A axis, or parameter 57, for the
B-axis, must be set to "0".
PARAMETERS
Содержание TRT210
Страница 2: ...Haas Technical Publications Manual_Archive_Safety_Pages Rev A June 6 2013...
Страница 6: ...MILL WARNING DECALS Haas Technical Publications Manual_Archive_Safety_Pages Rev A June 6 2013...
Страница 7: ...LATHE WARNING DECALS Haas Technical Publications Manual_Archive_Safety_Pages Rev A June 6 2013...