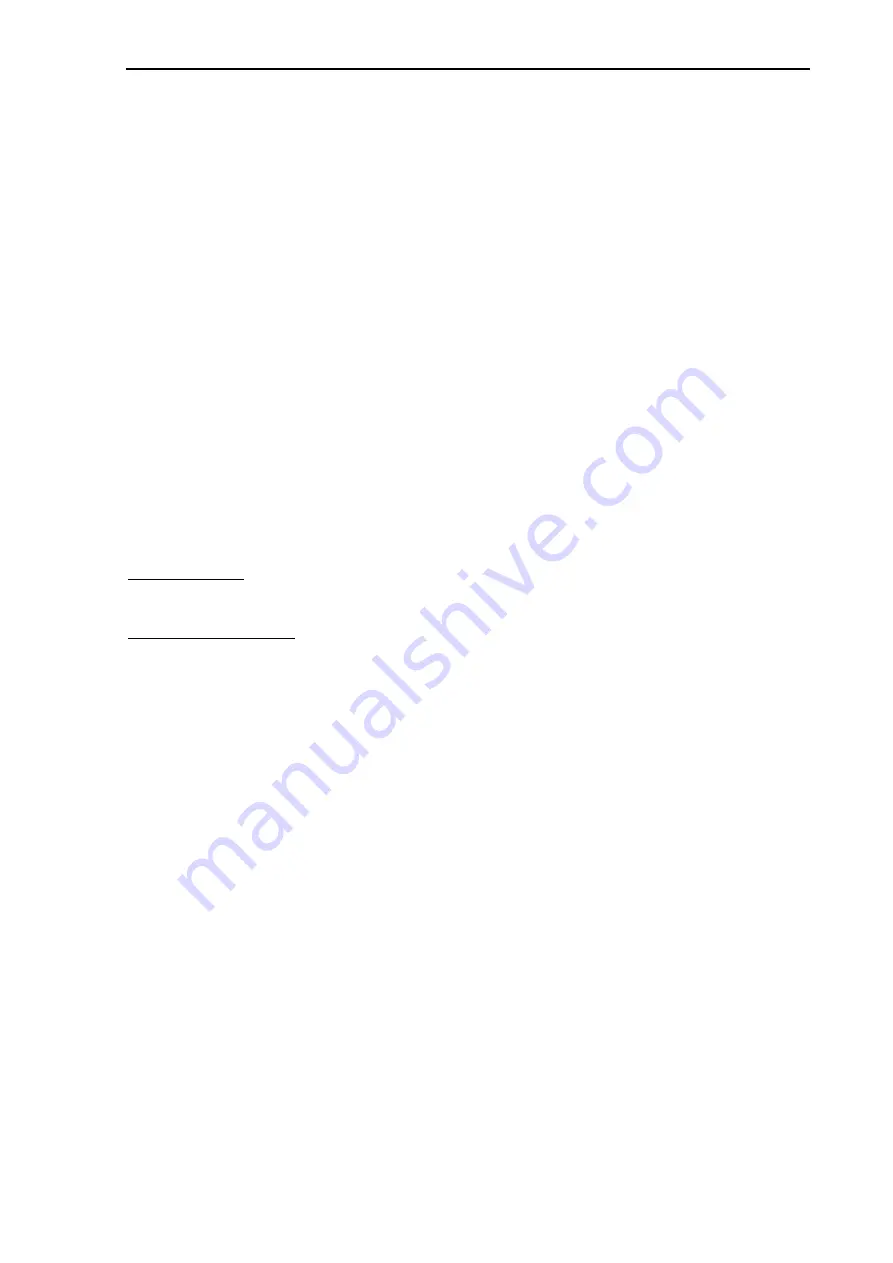
PR1713 Operating manual
Batching
Page 27
6.1.2.2 SPM output address
Output address function: Component handling activates this output bit. The default value of -1 must
be set to the correct value during component definition. -1 means that there is no output address.
The output address is a bit address (integer number up to 8191) in marker area M (storage capacity
for 1024*8 bits), which is activated by component handling. The real allocation to output area Q de-
pends on the PLC program in which it can be programmed.
See section: Address layout of signals.
6.1.2.3 SPM input address
Input address function: Component handling is activated only when this enable bit is set. The default
value of -1 must be set to the correct value during component definition. With address -1, the compo-
nent is always enabled.
The input address is a bit address (integer number up to 8191) in marker area M (memory capacity for
1024*8 bits), which is read by component handling. The real allocation to input area I depends on the
PLC program, where it is programmable.
See section: Address layout of signals.
6.1.2.4 Preset Point
Normal batching: The preset point determines the moment at which (set-point - preset point -
overshoot) the coarse batching valve is closed.
During discharging (B8): After weight below preset value, the hopper is considered as discharged.
Only the adjusted discharge time must elapse before the valve closes. The selected time value should
ensure that all material is still discharged.
6.1.2.5 Overshoot
All material which reaches the hopper after valve closing is called overshoot. The default value must
be selected so that it is slightly below the preset point. Only the overshoot part flown before elapse of
the calming time is included in the report.
The overshoot is determined only with tolerance check. It is optimized for the batching process and
corrected in the table, dependent of restart mode (1-4; 0=no correction). The next batch of this com-
ponent works with corrected values.
6.1.2.6 + Tolerance, - Tolerance
The tolerance is specified as a weight and can be determined independently with + for weight above
set-point and with - for weight below set-point.
Exceeded tolerances are followed by post-batching and overshoot correction for the component.
Tolerance errors generate a tolerance alarm which must be acknowledged. Moreover, an exceeded
set-point tolerance causes a production stop for a process step.
No tolerance check is made with a zero in both fields. In this case, overshoot correction and post-
batching are omitted. The overshoot value remains fixed, the restart mode remains without effect on
batching.
Содержание PR 1713/00
Страница 5: ...PR1713 Operating manual Operating concept Page 3...
Страница 14: ...Operating concept PR1713 Operating manual Seite 12...
Страница 16: ...Operating concept PR1713 Operating manual Seite 14...
Страница 18: ...Operating concept PR1713 Operating manual Seite 16...
Страница 20: ...Operating concept PR1713 Operating manual Seite 18...
Страница 50: ...Batching PR1713 Operating manual Seite 48...
Страница 52: ...Setup PR1713 Operating manual Seite 50...