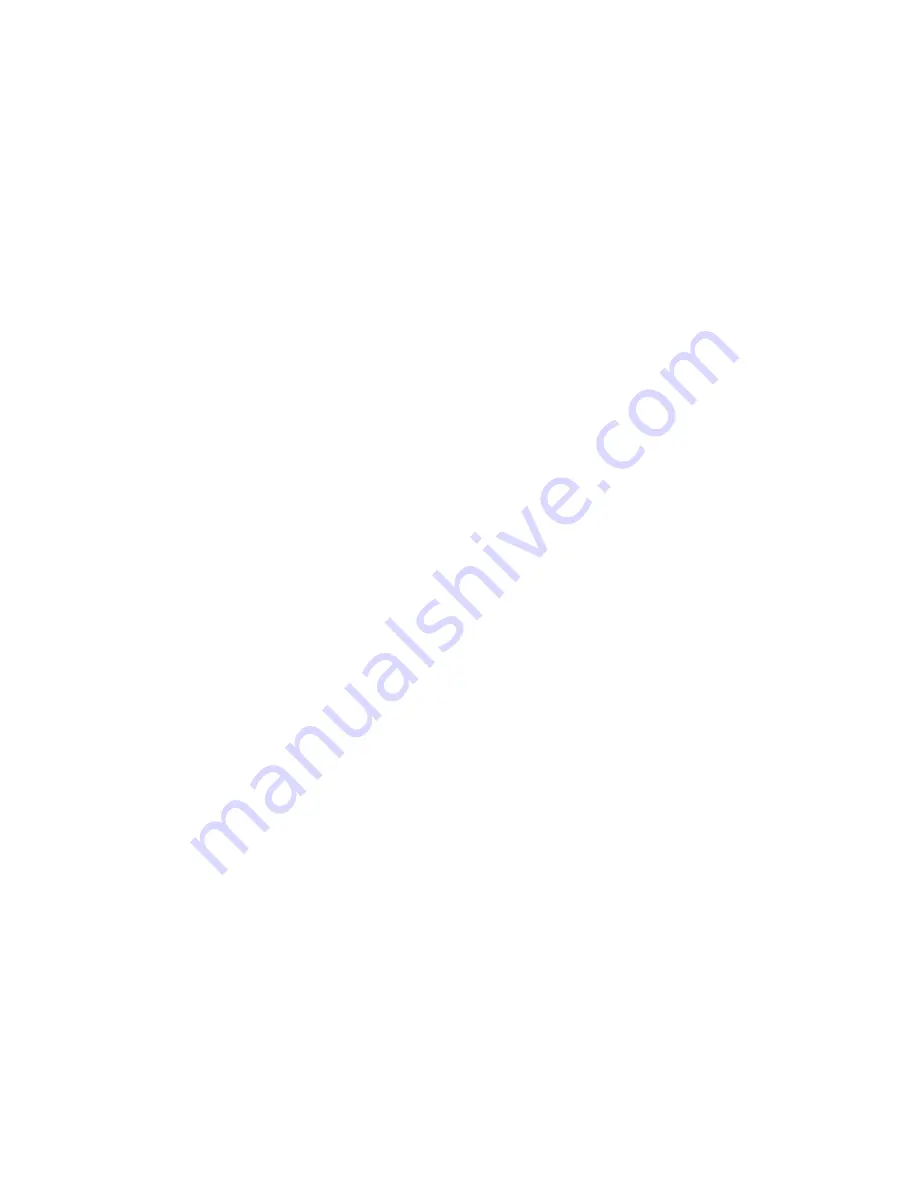
10
I. Compartmentized Probe only: Cut & install one 5’-0” length of vacuum hose between the probe tip & the
inner telescoping vacuum tube. Clamp in place using the worm screw clamps provided in the hardware
package.
J. Core Probe only: Install the core vacuum tube kit provided. Refer to the kit installation drawing and the
already installed vacuum tube assembly for proper placement. Cut & install two 5’-0” lengths of vacuum
hose between the core probe vacuum ports & the inner telescoping vacuum tubes. Clamp in place using the
worm screw clamps provided in the hardware package.
K. Route the vacuum hose from the outer telescoping vacuum tube(s) to the Sample Collection Cabinet and the
vacuum power unit. Route the sample hose along the most direct and shortest path. Avoid tight bends and
joints that may become locations that plug. Make all connections airtight and make sure all interior surfaces
of joints are smooth and flush. Any ragged or raised tube ends will collect dust and debris as well as retard
material flow. Escaping sample material can contaminate surrounding atmosphere and equipment. Clamp
in place using the worm screw clamps provided in the hardware package.
L. Install the 1” x 1.5” x 1.5” rotational stops. The two stops must be field-welded to the 1” thick top plate of the
probe stand beneath the driven sprocket of the pivot tube. These stops limit clockwise and counter-
clockwise (right and left) probe rotation. The probe rotation must be limited to 180 degrees for single lane or
300 degrees for dual lane operation. This will prevent the probe from being swung around and hitting the
hydraulic hoses. Reduce the amount of rotation if other obstructions such as buildings, poles, etc. are
nearby. First lightly tack weld the stops to the plate on top of the probe stand. Then swing the Probe
through the entire range of travel to verify that it does not hit any obstruction. When proper stop placement is
determined, weld the stops in their permanent position.
NOTE:
WHEN WELDING THE STOPS, CAREFULLY SHIELD THE DRIVE SPROCKET AND OTHER DRIVE
COMPONENTS FROM WELD SPATTER.
M. Remove the pump shipping bracket from the hydraulic power unit. Install the drive coupling & spider from
the hardware kit on the motor provided, but do not tighten yet. Place the motor in the cabinet, slide the pump
mount onto the motor shaft and fasten the motor to the cabinet & the pump mount. Access the coupling
through the hole in the pump mount. Make sure the motor coupling is almost fully engaged, (there should be
about 0.03” to 0.06” end clearance within the coupling, so that no force is pushing on the pump shaft).
Tighten the coupling set screw and replace the pump mount cover.
N. The hydraulic power unit is furnished with the valves pre-wired to an electrical junction box. Have a qualified
electrician complete the probe field wiring. This includes bringing the required power supplies to the
hydraulic unit electrical junction box, motor starter, motor, tank heater, vacuum motor(s), and the operators
control panel. Refer to the certified electrical drawings.
3.5 Initial Startup
A. On the operators control panel, turn the POWER switch on. The hydraulic power unit motor should start,
building system pressure. Verify proper hydraulic pump motor rotation. Correct wiring if necessary.
B. Use the push-buttons or joy-sticks to move the probe around. Make sure the air is removed from all
hydraulic lines. It may be necessary to loosen a hose where it connects to a cylinder, motor, or actuator to
bleed off trapped air.
Содержание InterSystems STP
Страница 5: ...4 FIGURE 1 1 TRUCK PROBE SAFETY LABEL LOCATIONS ...
Страница 32: ...31 FIGURE 7 1 MAIN STAND ASSEMBLY ...
Страница 33: ...32 FIGURE 7 2 TELESCOPING BOOM ASSEMBLY FIGURE 7 3 COMPARTMENTIZED CORE PROBES ...
Страница 34: ...33 FIGURE 7 4 SAMPLE CABINETS ...
Страница 35: ...34 FIGURE 7 5 VACUUM MOTOR UNITS ...
Страница 36: ...FIGURE 7 7 6 HYDRAU ULIC POWER R UNIT ASSEMBLY 35 ...
Страница 37: ...36 FIGURE 7 7 HYDRAULIC POWER UNIT FITTINGS HOSES ...
Страница 38: ...37 FIGURE 7 8 HYDRAULIC HOSES FITTINGS ...