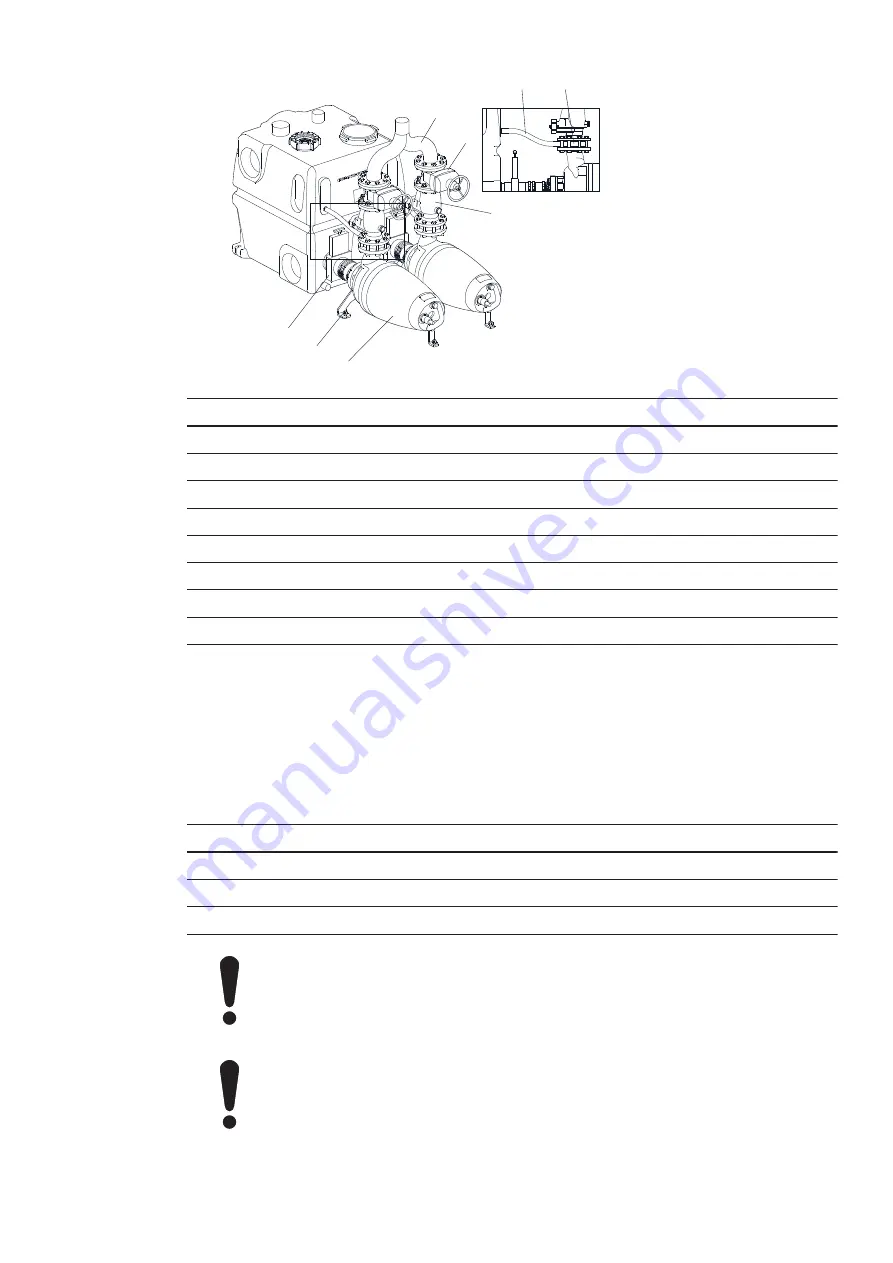
1
2
3
4
6
5
7
8
Pos.
Description
1
Isolating valve, accessory
2
Dowels and screws
3
Pump
4
Non-return valve, accessory
5
Breeches pipe, accessory
6
Isolating valve, accessory
7
Vent hose
8
Vent flange
Related information
• 3.2.2.3 Connecting the outlet pipe
3.2.2.2 Connecting the inlet pipe
•
All pipe connections must be flexible to reduce resonance.
•
Install an isolating valve in the inlet pipe.
Many installations require an inlet below the standard inlet 700 mm above the floor. You can fit a
lip seal on site. Use the following accessories:
Product number
Description
91713755
Hole saw,
∅
177
91712026
Centring drill
91071939
Lip seal, DN 150, internal
∅
160
Make sure that the weight from the inlet, outlet and vent pipes does not rest on
the tank. Long pipe sections and valves must be supported.
Never stand on the lifting station.
The internal diameter of the inlet pipe must be the same as the internal diameter of the inlet port.
1. Cut open one of the inlet ports to be used and/or connect pipes to the second tank.
Multilift MD1, MDV | |
11