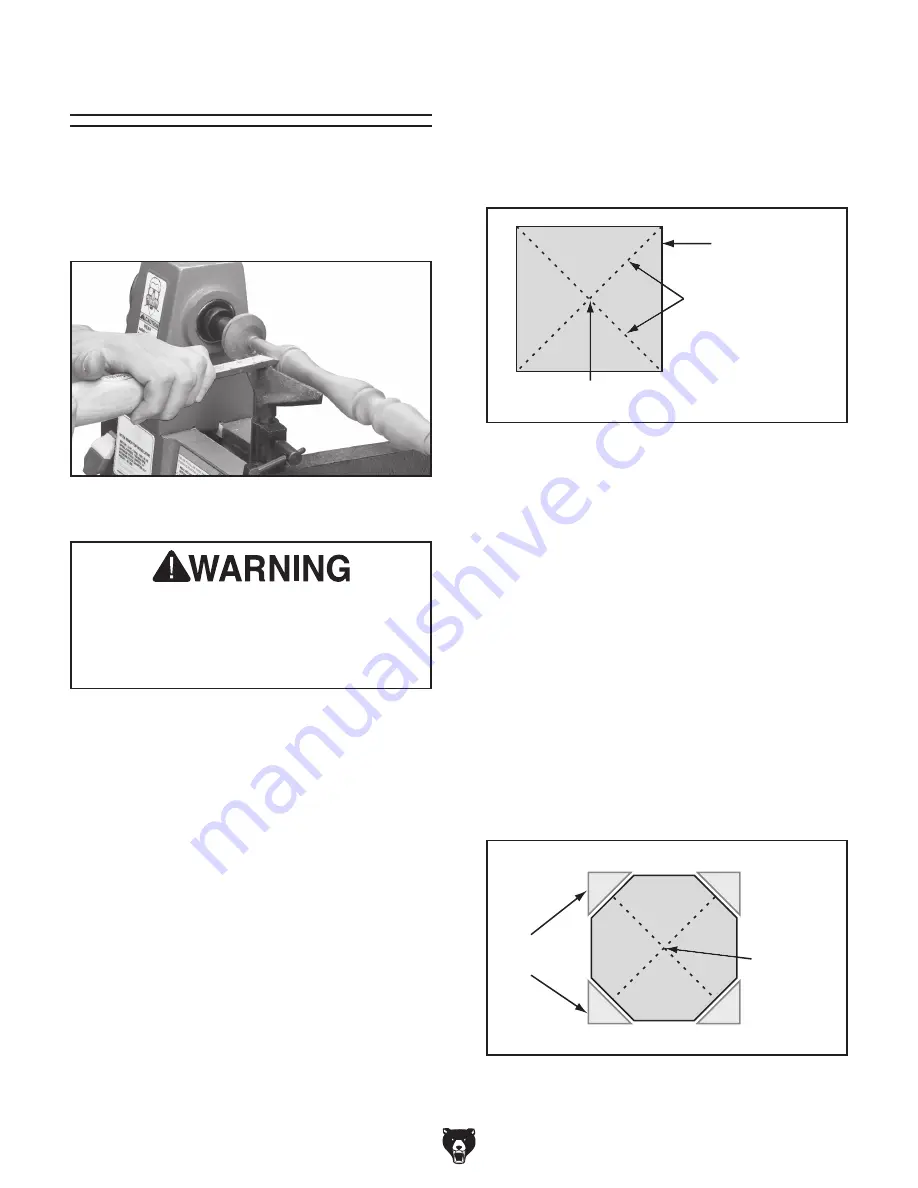
Damage to your eyes and lungs could result
from using this machine without proper pro-
tective gear. Always wear safety glasses, a
face shield, and a respirator when operating
this machine.
Figure 21. Example of typical spindle turning
operation.
Figure 22. Workpiece marked diagonally from
corner to corner to determine the center.
Workpiece
Workpiece
Center
Pencil Lines
Marked Diagonally
Across Corners
Workpiece
Center
Corners
Removed
Figure 23. Corners of workpiece removed.
-24-
Model T32536 (Mfd. Since 10/20)
Spindle Turning
To set up a spindle turning operation:
1. Find center point of both ends of your
workpiece by drawing diagonal lines from
corner to corner across end of workpiece, as
shown in
Figure 22.
2. Make a center mark by using a wood mallet
and tapping point of spur center into center of
workpiece on both ends.
3. Drill a
1
⁄
4
" deep hole at center mark on end of
the workpiece to be mounted on headstock
spur center.
4. To help embed spur center into workpiece,
cut
1
⁄
8
" deep saw kerfs in headstock end of
workpiece along diagonal lines marked in
Step 1.
5. If your workpiece is over 2" x 2", cut cor-
ners off workpiece lengthwise to make turn-
ing safer and easier when roughing out
workpiece (see
Figure 23).
Spindle turning is the operation performed when
a workpiece is mounted between centers in the
headstock and tailstock, as shown in
Figure 21.
Bowls, table legs, tool handles, and candlesticks
are typical projects where this operation is used.
Tools Needed
Qty
Precision Ruler .................................................. 1
Wood Mallet....................................................... 1
Drill Bit
1
⁄
4
" .......................................................... 1
Tablesaw/Bandsaw ............................................ 1
Содержание T32536
Страница 44: ......